کنترل کیفی مخلوط ها و مواد SCC
ایجاد یک طرح کنترل کیفی جامع در فرآیند SCC از اهیمت ویژه ای برخوردار است و به منزله دستیابی به اهداف عملی درست و یا بهبود ویژگی های مناسب مخلوط می باشد. در چنین شرایطی ممکن است تولید کننده یا پیمانکار، طرح کنترل کیفی را به عنوان یک منبع بی ارزش تلقی کنند و آن را برای فرآیند تولید SCC ضروری ندانند.
این نگرش به خاطر این است که آنها تنها از داده ها استفاده می کنند و از آنها مطالبی می آموزند. واژه ACI بیان کننده کنترل کیفی به عنوان فعالیت انجام شده توسط پیمانکار و یا تولید کننده جهت ایجاد کنترل بر آنچه در حال انجام است و یا آنچه در دست تهیه است، بطوری که استانداردهای لازم و مناسب در فرآیند فعالیت ها و عملکردها قابل اجرا باشد، می باشد.
کنترل کیفی مطلوب در SCC شامل انجام آزمایش های متعدد و دستیابی به نتایج، تبدیل یافته ها به دانش و اطلاعات و استفاده از این دانش برای اصلاح و توسعه برنامه های SCC می باشد. این موضوع به ویژه در مراحل نخست تولید و زمان استفاده از SCC دارای اهمیت است. به خصوص زمانی که میزان سطح تجربه ما پایین باشد، نیاز به فعالیت کنترل کیفی در این مرحله بیش از بتن معمولی است. باید دقت فراوانی در مواد، ویژگی های تازه مخلوط و نیز تاثیر آنها بر کیفیت نهایی بتن در حمل مبذول داشت. چه میزان دقت و توجه در کنترل کیفی در تولید SCC ضروری است تا شرایط مورد نیاز برای عملکرد مناسب SCC فراهم شود؟
مشابه عملکرد بالای مخلوط در ایجاد مقاومت و یا دیگر عملکردهای بالای SCC، چنانچه میزان دقت و توجه افزایش یابد، شرایط لازم برای عملکرد مخلوط نیز افزایش یافته، در نتیجه اشتباه کاهش می یابد. برای مثال زمانی که جریان اسلامپ در مخلوط SCC به میزان بالایی افزایش می یابد. تفکیک اتفاق می افتد. بنابراین افزایش بالای میزان جریان اسلامپ باید تحت مراقبت و نظارت بیشتری (در مقایسه با مخلوط های مشابه با جریان اسلامپ پایین) انجام شود تا از ایجاد ثبات در مخلوط اطمینان حاصل کرد. به تدریج تجربیات بیشتری در مورد SCC حاصل می شود و تولید کنندگان نیز درک بیشتری نسبت به رابطه متقابل مواد اولیه و عملکرد مخلوط پیدا می کنند. زمانی که تولید کنندگان به تخصص کافی در این زمینه دست یابند، کنترل کیفی اهمیت ویژه ای پیدا می کند و کار کنترل و نظارت هوشمند بر متغیرهایی که نقش اساسی در عملکرد خاص را دارند، عهده دار خواهد بود، این همان سطح مهارت و تخصصی است که بدان نیاز دارید.
به منظور ایجاد سرفصل هایی برای طرح های کنترل کیفی در حوزه SCC، باید قبل از شروع پروژه، بررسی کرد که آیا این طرح در توسعه مخلوط مفید و موثر است؟ و آیا تمام اعضای گروه با این طرح رابطه خوبی برقرار کرده اند؟ آیا کنترل کیفیت، وظیفه تمام اعضای ساخت و ساز است؟ عرضه کنندگان سنگدانه ها، افزودنی ها، سیمان و دیگر پودرها باید به تولید کننده بتن در مورد مواد اولیه و نیز فراهم کردن نیازها، تضمین لازم را بدهند. در عوض تولید کننده نیز مسئول کنترل و هماهنگی بتن پیمانه شده و ارسال شده می باشد و بالاخره زمانی که بتن به محل پروژه می رسد و مورد استفاده قرار می گیرد، این وظیفه پیمانکار است که در مورد کیفیت مواد در محل پروژه اطمینان دهد و چنانچه هر فرد مسئولیت های خود را در ابتدای کار به نحو احسن انجام دهد، پروژه به موفقیت های سرشاری دست خواهد یافت و این برداشت کلی در بتن SCC و بتن معمولی هیچ تفاوتی با هم ندارند. همه کسانی که به دنبال ارائه یک طرح کنترل کیفی خوب و مناسب هستند، از مزایای زیر بهره مند خواهند شد:
- یک پروژه با درصد موفقیت بالا و ایجاد کیفیت های نهایی برای محصول
- افزایش سطح مواد داخلی و نیز افزایش مهارت عملکرد SCC
- حذف و یا کاهش مشکلات پس از بچینگ و یا پس از بتن ریزی
- ارائه طرح اقتصادی تر برای مخلوط SCC و یا روش های بتن ریزی
- افزایش فروش و نیز افزایش تعداد مصرف کنندگان SCC
- افزایش اعتبار به خاطر مهارت دقیق فنی و تخصصی بتن
پیشنهادات ارائه شده در این فصل، به منظور افزایش برنامه کنترل کیفی تبیین شده است و هدف از آن مشخص کردن محدوده های خاصی از SCC می باشد که قبل از تولید و نیز طی تولید باید تحت نظارت قرار گیرند، همچنین مواردی که باید به آن افزوده شود تا طرح جامع به وجود آید. این محدوده های خاص شامل نظارت بر مواد اولیه مانند سنگدانه ها و پودرها، مرور موارد مطالعاتی و دستورالعمل های منتشر شده در مورد نظارت بر عملکرد بتن و ارائه یک معیار قابل قبول و در آخر یک فرآیند ارزیابی داخلی به وسیله تولید کننده توصیه می شود.
در اینجا شایان ذکر است که بگوییم هدف از آزمایش کنترل کیفی این است که از عملکرد، ثبات و عمر مفید سازه نهایی اطمینان حاصل کنیم. اما کنترل کیفی همچنین قادر به ایجاد فرصت هایی مناسب برای درک بهتر تاثیر مواد بر عملکرد SCC نیز می باشد. چنانچه بچینگ دچار اختلال شود (بیش از میزان مورد نظر بتن بریزد)، تولید کننده باید زمانی را صرف یافتن علت آن نماید. اگر این فرآیند نیازمند صرف وقت و سرمایه است، عقیده نویسنده این است که دستیابی به علل و عواملی که باعث می شوند بعضی از کارها به خوبی پیش برود و بعضی دیگر دچار اختلال شود بسیار مهم است. همچنین برای دستیابی به این علل باید از تجهیزات نظارت بر تولید و ابزار پیشرفته استفاده کرد و همیشه نقص ها و اشتباهات موجب ایجاد فرصت می شوند.
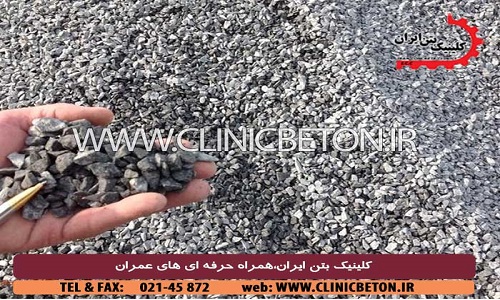
کنترل کیفی مواد خام
بطور ��لی، هر نوع اطلاعاتی که در طی فرآیند کنترل کیفی جمع آوری می شود چه از مواد خام و چه از انجام آزمون بتن، دو هدف مشخص به دنبال دارد:
- ارائه شاخصی که تضمین کننده مواد (مصالح) و کیفیت بتن باشد.
- بین عملکرد بتن و ویژگی های مواد ارتباط برقرار کند.
بررسی تاریخچه عملکردها و آزمایش ها همواره یک هدف دراز مدت بوده است. تحلیل و بررسی داده های تاریخی در انتخاب مواد خام و نسبت بندی آنها برای آینده پروژه همواره مفید بوده و همچنین ممکن است نیاز به تنظیم نسبت بندی مخلوط ها را مورد تاکید قرار دهد.
پودرها و سنگدانه هایی که برای تولید مخلوط SCC مورد استفاده قرار می گیرند باید بطور مرتب تحت نظارت و کنترل باشند. نظارت بر این مواد خام به وسیله گردآوری اطلاعات از عرضه کننده مواد و همچنین نتایج حاصل از یک برنامه آزمایش داخلی انجام می شود. بعد از انجام آزمایش ها، اطلاعات جمع آوری شده باید مشابه اطلاعات به دست آمده از انجام فعالیت شناسایی مواد خام در فاز توسعه مخلوط در آزمایشگاه باشد. در این روش، چنانچه نوساناتی در عملکرد مخلوط SCC ایجاد شود فرصت برای ایجاد تغییرات لازم در مواد خام در نتیجه تغییر در عملکرد بتن، پدید می آید. در نتایج حاصل از بررسی مبنایی کیفیت، که توسط اتحادیه ملی ساخت بتن آماده در آمریکا اخیراً منتشر شده است، از افرادی که در این بررسی شرکت کردند سوالاتی در مورد برنامه کنترل کیفی و عملکرد آنها مطرح شد. موضوع بررسی صرفاً در مورد مخلوط SCC نبود و همه تولیدات بتنی را در بر داشت. وقتی از آنها در مورد تعداد دفعات آزمایش درجه بندی سنگدانه ها در کارخانه ها سوال شد، 25 درصد پاسخ دادند که صرفاً از اطلاعات ارائه شده در مورد سنگدانه ها توسط فروشنده، استفاده می کنند، 54 درصد پاسخ دادند هفته ای یک بار آزمایش انجام می دهند،
14 درصد ماهی یک بار و 7 درصد اعلام نمودند 3 ماه یک بار و یا کمتر. زمانی که از آنها سوال شد که آیا از اطلاعات به دست آمده در مورد سیمان اولیه استفاده می کنند یا نه؟ 4 درصد پاسخ دادند که هیچ اطلاعاتی در این زمینه جمع آوری نمی کنند. 64 درصد گفتند آنها اطلاعات ارائه شده توسط کارخانه های سیمان را جمع آوری می کنند، 25 درصد پاسخ داده که از اطلاعات ارائه شده توسط کارخانه ها و دیگر منابع استفاده می کنند و 7 رصد اظهار کردند که از اطلاعات ارائه شده توسط کارخانه های دیگر سیمان استفاده می کنند. زمانی که از آنها در مورد آزمایش منبع اولیه مواد سیمانی سوال شد، 57 درصد پاسخ دادند هیچ آزمایشی در این زمینه انجام نداده اند. 4 درصد گفتند که این آزمایش ا هفته ای یک بار انجام می دهند، 7 درصد پاسخ دادند ماهی یک بار و 32 درصد از آنها اعلام کردند که هر سه ماه یک بار یا کمتر. بعد از گفتگوهایی که نویسنده با تولید کنندگان بتن پیش ساخته و بتن آماده انجام داد مشخص شد که آمارها به معیار تولیدات SCC نزدیک است.
سرفصلی جامع از مراحل و فعالیت های نظارتی در مورد هماهنگی سنگدانه های بتن، سیمان و مواد خام دیگر که برای تولید بتن مورد استفاده قرار می گیرد در مقالات و نشریات صنعتی ارائه شده است. به هر حال، در بخش آینده این خصوصیات مواد اولیه مورد تاکید قرار خواهد گرفت، زیرا زمان تولید SCC باید به این ویژگی ها توجه داشت، در غیر این صورت این نظارت (توجه به ویژگی مواد اولیه) را باید در برنامه کنترل کیفی جا داد.
سیمان C | سیمان B | سیمان A | |
385 | 351 | 391 | حد وسط (m2/kg) |
23 | 17 | 54 | انحراف معیار (m2/kg) |
67 | 47 | 161 | محدوده (m2/kg) |
335 | 321 | 300 | حداقل (m2/kg) |
402 | 368 | 461 | حداکثر (m2/kg) |
6% | 5% | 14% | ضریب تغییر |
8 | 7 | 11 | تعداد |
جدول-1 آنالیز آماری داده ها در مورد سنگدانه های ریز بلین برای سه ASTM C 150 نوع یک سیمان پرتلند
نظارت بر پودرها
برخی از پودرها که در تهیه بتن SCC به کار می روند در مقایسه با دیگر مصالح از تنوع بالایی برخوردارند. برای مثال: ممکن است منشا پودر مورد استفاده در SCC از وزش ضایعات صنعتی باشد مانند خاک سنگ حاصل از دستگاه سنگ شکن (در تولیدات سنگدانه) یا موادی که تحت کنترل و نظارت تولید می شوند مانند سیمان پرتلند. مواد متنوع جهت استفاده باید همواره تحت نظارت دقیق و آزمایش های مکرر قرار گیرند. اما معمولاً این آزمایش ها توسط تولید کنندگان بتن انجام نمی شوند (همان طور که قبلاً نیز در نتایج حاصل از بررسی ها مشاهده شد). شناسایی درست و دقیق پودرها نیازمند تجهیزات تخصصی و صرف وقت و انرژی فراوانی است. اصولاً یک تولید کننده، پودرهایی را که عملکرد مخلوط بتن را تحت تاثیر قرار می دهند، کنترل می کند. داده های ارائه شده در این روش، دستورالعمل های روشنی را در رابطه با عملکرد پودرها ارائه نمی دهند (به علت اینکه انجام آزمون ها نیاز به دقت خاصی دارد).
چنانچه تولید کننده قادر به انجام آزمایش شناسایی پودرها نباشد، باید از گزارشات ارائه شده توسط عرضه کنندگان مربوطه در مورد ویژگی های فیزیکی و یا شیمیایی پودرها استفاده کند. تولید کننده همچنین باید از صحت اطلاعات ارائه شده در مورد بسیاری از مواد مورد استفاده خود، اطمینان حاصل کند. جمع آوری داده ها جهت ثبت سوابق ویژگی های مواد نیز دارای اهمیت است. به عنوان مثال: جدول-1 نشان دهنده داده های مربوط به سنگدانه های ریز بلین در تعدادی از انواع سیمان است که از سه عرضه کننده سیمان تهیه شده است.
چنانچه یک نفر داده هایی را در مورد مواد مرتبط با داده های بتنی جمع آوری کند روند تاریخی مشخصی نمایانگر می شود. برای مثال استفاده از یک سیمان با سنگدانه های ریز مختلف مانند سیمان A در جدول -1 منجر به کاهش پایداری ویژگی های تازه، نوسان در میزان نیاز به آب و مقدار HRWR می گردد.
داده های ارائه شده در مورد سوابق گذشته نوع مصالح (براساس ثبات آنها) برای استفاده در آینده پروژه آینده کمک خواهند کرد. یا اگر امکان انتخاب مصالح وجود نداشته باشد، آنگاه نسبت بندی تنظیم خواهد شد، مانند افزایش استفاده از پودرهای جانشین یا افزایش مقدار افزودنی های اصلاح کننده ویسکوزیته جهت بالا بردن قدرتمندی و کاهش تلاش های لازم برای کنترل کیفی.
ابزارهای معمول برای کنترل کیفی ویژگی های مواد مانند هیستوگرام ها روش خوبی برای نظارت دائمی هستند.
نظارت بر سنگدانه ها
چنانچه ویژگی سنگدانه ها بطور چشمگیری تغییر کند، این امر موجب تغییر در ویزگی مخلوط تازه خواهد شد. احتمالاً تا زمانی که فرآیند تولید و ترکیب سنگدانه ها تغییر نکند، سنگدانه هایی که منشأ و منبع یکسانی دارند، شکل ذراتشان نیز ثابت خواهد بود. ویژگی های اصلی سنگدانه هایی که تحت کنترل می باشند شامل درجه بندی یا توزیع اندازه ذرات و میزان فضاهای خالی می باشد و چنانچه میزان جذب بالا باشد فرآیند تغییر نظارت بر ویژگی جذب اعمال خواهد شد. علاوه بر این، ویژگی های آماری میزان رطوبت آزاد سنگدانه ها باید مورد نظارت و کنترل قرار گیرند.
نظارت بر توزیع اندازه ذرات
با تفکیک الک می توان اندازه سگدانه ها را درجه بندی کرد، از این روش اصولاً در تفکیک سنگدانه های ریز و درشت که در ساخت SCC کاربرد دارند استفاده می شود. براساس دستورالعمل کنترل کیفی متعلق به انجمن ملی بتن پیش ساخته، لازم است که آزمایشات جداسازی (تفکیک) برای تقریباً 1360 متریک تن سنگدانه های ریز و 1800 متریک تن سنگدانه های درشت انجام می شود. اما چگونه اطلاعات حاصل از درجه بندی سنگدانه ها برای ارتقاء کیفیت و ثبات SCC مورد استفاده قرار می گیرد؟ غربالگری با الک های 75 و 300 میکرومتر پیشنهاد شد و پس از نظارت نتایج زیر به دست آمد که کل مواد مخلوط از یک الک 300 میکرومتری عبور داده شد (شامل سنگدانه ها و پودرها) که برای ارزیابی میزان آب دهی مخلوط مورد استفاده قرار می گرفت. اگر چه میزان آب دهی مخلوط بستگی به نسبت بندی مخلوط دارد، نظارت بر این ویژگی به ما کمک می کند که زمان تنظیم مخلوط را پیش بینی کنیم. مثلاً آیا افزودن VMA و یا افزایش مقدار آن ضروری است. برای مثال شکل -1 جداسازی بیش از 100 مجموعه مجزا از سنگدانه های ریز با منبع یکسان که از یک الک 300 میکرومتری عبور داده شده اند را ترسیم کرده است.
توجه کنید که در برخی از نمونه ها، کاهش و یا افزایش چشمگیری از گروهی به گروه دیگر مشاهده می شود، برای مثال گروه 52 و 53 به ترتیب 15 و 4 درصد از الک عبور کرده اند. این تغییر چشمگیری می باشد و به خاطر چنین تغییر رادیکالی، آزمایش روی گروه 53 برای چندین بار تکرار می شود که از صحت آن اطمینان حاصل شود (قبل از اینکه نسبت بندی مخلوط را تغییر دهیم). فرض کنید نتیجه آزمایش معتبر است، چگونه این عامل می تواند بر روی عملکرد مخلوط SCC تاثیر بگذارد. حال فرض کنید تولید کننده ای مخلوط خود را با سنگدانه های ریز به میزان 850 کیلوگرم توسعه داده است، اگر شاخص تولید را با گروه 52 آغاز کند و سپس گروه 53 را جانشین آن کند، این امر منجر به کاهش 100 کیلوگرم در هر مترمکعب از مواد عبوری از الک 300 میکرومتر می باشد.
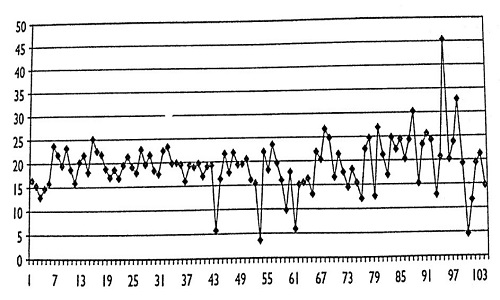
تصویر -1 درصد عبوری سنگدانه های ریز از الک 300 میکرومتر
با توجه به نسبت بندی مخلوط اصلی، این تغییر و تحول منجر به ایجاد تغییرات زیادی در میزان آب دهی مخلوط می گردد. همچنین قدرتمندی مخلوط پیمانه شده با نسبت بندی مشخص، کاهش می یابد و تفاوت در ویژگی به دلیل تفاوت در منشأ و منبع مواد می باشد. بنابراین، جمع آوری و تجزیه و تحلیل این داده های زمانی در این ویژگی ها و در مورد منابع مختلف، بسیار ارزشمند است. جدول 11-2 نشان دهنده یک تحلیل مقایسه ای بین دو سنگدانه ریز که از الک 300 میکرومتر عبور داده شده اند، می باشد. سنگدانه ریز شماره 2 نسبت به شماره 1 دارای ضریب تغییرات پایینی است. اما یکی از آنها می تواند در عملکرد نوسان ایجاد کند و این جایی است که نظارت و مرور داده های تاریخی جمع آوری شده، از نظر نسبت بندی مخلوط می تواند ارزشمند باشد. اگر چه سنگدانه های ریز شماره 1 متنوع تر است، درصد مواد ریز در آن بیشتر از سنگدانه های ریز شماره 2 می باشد، بدین معنی که میزان سنگدانه های ریز افزوده شده به مواد که دارای منشأ متفاوتی هستند کاهش می یابد و این می تواند بر ارزش کل مواد در مخلوط تاثیر بگذارد. در هر حال تولید کننده باید بین ارزش مصالح، توانایی نظارت بر مصالح و تنظیم نسبت بندی آنها تصمیم گیری کند. اگر تولید کننده ای داده های تاریخی (زمانی) را در طی نسبت بندی اولیه در اختیار نداشته باشد، فرآیند نظارت و در نتیجه تنظیم مخلوط می تواند به بهبود عملکرد کمک کند. از آنجایی که تفاوت و تنوع در سنگدانه شماره 1 بیشتر است، این سنگدانه باید بیش از سنگدانه شماره 2 مورد آزمایش قرار گیرد و تا زمانی که به ثبات مورد نظر دست نیافته، آزمایشات باید ادامه یابد.
سنگدانه ریز 2 | سنگدانه ریز 1 | |
14.10 | 19.20 | حد وسط |
2.10 | 5.40 | انحراف معیار |
8 | 41.7 | محدوده |
10.2 | 3.6 | حداقل |
18.2 | 45.3 | حداکثر |
25 | 104 | تعداد |
15% | 28% | ضریب تغییر |
جدول -2 آنالیز مقایسه ی درصد عبوری دو مجموعه از سنگدانه های ریز از الک 300 میکرومتر
موادی که از الک 75 میکرومتر عبور می کنند بخشی از پودرها بوده و نیز محتوای خمیری یک مخلوط SCC را تشکیل می دهند. اطمینان از همسان بودن پودرها و خمیرها در عملکرد هماهنگ مخلوط نقش اساسی دارد. تصویر -2 درصد عبور از الک 75 میکرومتر را برای 90 گروه از سنگدانه های ریز شماره 1 نشان می دهد.
در تغییرات گسترده ای در بین گروه های متوالی براساس این ویژگی ها دیده شده است. برای مثال گروه 50 و 51، درصد عبور از الک 70 میکرومتر به ترتیب 2/3 درصد و 3/0 درصد بوده است، اختلافی برابر با 9/2 درصد. دوباره یک مخلوط 850 کیلوگرم در هر مترمکعب را فرض کنید، به همان ترتیب وقتی از گروه 50 به گروه 51 می رسیم، کاهش تقریبی 25 کیلوگرم در هر متر مکعب در میزان پودر مشاهده می کنیم. با چگالی 6/2 سنگدانه های ریز، تقریباً 1% کاهش در میزان حجم خمیر خواهیم داشت. با توجه به ویژگی های بیشتر سنگدانه های ریز که در نسبت بندی اولیه مخلوط مورد استفاده قرار می گیرند، باید با افزایش میزان مواد ریز شاهد افزایش ویسکوزیته، آب، نیاز به افزودنی ها و همچنین کاهش در میزان جریان اسلامپ باشیم. برعکس، اگر میزان مواد ریز افزایش یابد، پایداری در مخلوط، میزان نیاز به آب یا افزودنی ها و میزان جریان اسلامپ همگی افزایش می یابند.
جمع آوری و مرور داده های تاریخی در این مورد نیز ارزشمند است، جدول -3 یک تحلیل مقایسه ای از مواد عبوری از الک 75 کیلوگرم در هر متر مکعب ارائه می دهد که براساس آیین نامه استاندارد
ASTM C 117 الک مرطوب، برای دو نوع سنگدانه های ریز به دست آمده است. براساس ضریب تغییرات، تنوع این سنگدانه ها مشابه یکدیگر است. از آنجایی که میزان سنگدانه های ریز (2) در مواد کمتر است، تاثیر آنها نیز به مراتب کمتر از تاثیر سنگدانه های شماره (1) است.
در طی مرحله نسبت بندی مواد، چنانچه مواد ریز (که از سنگدانه ریز به دست آمده است) به صورت محتوای پودری در مخلوط داشته باشیم باید از اهمیت تغییر پذیری آن آگاه باشیم. گام های اساسی برای نسبت بندی مخلوط باید با در دست داشتن مقدار کافی از دیگر پودرها آغاز شود بطوری که نباید حجم خمیر از میزان حداقل مشخص شده کمتر شود، گذشته از این شرایط، سنگدانه های ریز شماره (1) به دلیل تغییرات بالقوه عمده باید بیشتر مورد آزمایش قرار بگیرند.
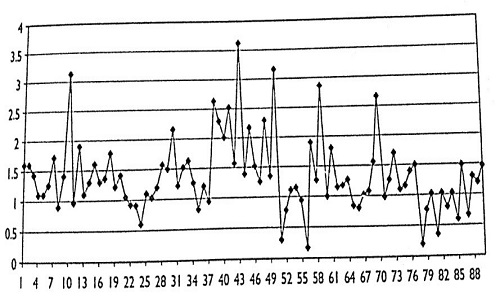
تصویر -2 درصد عبوری سنگدانه های ریز از الک 75 میکرومتر
سنگدانه ریز 2 | سنگدانه ریز 1 | |
0.47 | 1.37 | حد وسط |
0.23 | 0.63 | انحراف معیار |
0.95 | 3.45 | محدوده |
0.11 | 0.17 | حداقل |
1.06 | 3.62 | حداکثر |
23 | 90 | تعداد |
48% | 46% | ضریب تغییر |
جدول -3 درصد عبوری از الک 75 میکرومتر برای دو مجموعه سنگدانه های ریز
در بیشتر مواردی که طرح کنترل کیفی وجود دارد، درجه بندی سنگدانه ها بطور مرتب انجام می شود. پیشنهاد نویسنده ایجاد یک هیستوگرام درصد عبوری از الک های 75 و 300 میکرومتر جهت کنترل و نظارت می باشد. اگر چه در حال حاضر هیچ معادله و توازنی میان عملکرد مخلوط و اندازه گیری های موجود پیش بینی نشده است، اما همان طور که قبلاً بیان شده و با توجه به تجربیات زیاد تولید کننده در توسعه SCC با افزایش و یا کاهش بعضی از این مقادیر به مشکلاتی در عملکرد مخلوط پی می بریم.
از آنجایی که قابلیت عبور مسئله مهمی است، تولید کننده باید درصد سنگدانه های بزرگ تر باقیمانده در الک را کنترل کند. افزایش تعداد خرده سنگ های درشت تر موجب افزایش انسداد و کاهش در توانایی عبور مخلوط می شود، برآورد میزان لازم مواد از طریق معادله بیلبرگ امکان پذیر است.
نظارت بر فضای خالی سنگدانه ها
در SCC ویژگی سیالیت و روان بودن مخلوط موجب ایجاد حجم خمیر می شود. فضای خالی سنگدانه ها بر حجم خمیر مورد نیاز تاثیر می گذارد. افزایش در حجم فضای خالی باعث تاثیر در کاهش میزان خمیر آزاد مورد استفاده در ارتقاء سیالیت مخلوط می شود.
می توان فضای خالی بین سنگدانه های درشت و سنگدانه ریز را بطور جداگانه کنترل و نظارت کرد یا می توان بر فضای خالی بین ترکیب سنگدانه ها (ریز و درشت) که در تولید مخلوط SCC مورد استفاده قرار می گیرد نظارت کرد و البته مورد آخر (نظارت بر ترکیب سنگدانه ها) در مورد SCC از اهمیت ویژه ای برخوردار بوده و بسیار مفید می باشد. در شرایط یکسان، تغییر در فضای خالی ترکیب سنگدانه ها رابطه مستقیمی با عملکرد بتن دارد. چنانچه فضای خالی افزایش یا کاهش یابد جریان روانی مخلوط کاهش یا افزایش می یابد. انجام آزمایشات مکرر بستگی به طرح کنترل کیفی در محل پروژه داشته یا با شناسایی قابلیت تغییر پذیری منابع و منشأ مواد خام مشخص می شود.
نظارت بر رطوبت سطح آزاد
بیشتر تجهیزات مدرن در بخش تولید، نظارت مستمر و دقیقی بر میزان رطوبت دارند (چه در سیلوی شن و ماسه و چه در مخزن مخلوط). کنترل رطوبت به صورت دقیق و مستمر برای تولید SCC بسیار دارای اهمیت است.
براساس آیین نامه کنترل کیفی که توسط انجمن ملی بتن پیش ساخته ارائه شده، میزان رطوبت سطح باید از نظر فیزیکی روزی یک بار و قبل از اولین بچینگ SCC کنترل شود، حتی زمانی که از رطوبت سنج استفاده می شود. اگر از رطوبت سنج خطی استفاده نشود، دستورالعمل های PCI و NPCA اظهار می دارند که رطوبت باید بصورت دستی و در ابتدای شروع هر عملیات بچینگ و هر 4 ساعت یک بار در طی این مرحله آزمایش شود، حتی زمانی که از رطوبت سنج استفاده می شود. یک مخلوط قدرتمند که توسط تجهیزات پیشرفته تولید می شود نیازی به استفاده از رطوبت سنج خطی ندارد.
نظارت بر عملکرد
برای اینکه از کارایی و تاثیر یک طرح آزمایش بتن اطمینان حاصل کنیم باید قبل از شروع پروژه همه چیز مکتوب شود. باید مشخص شود که چه آزمایش هایی مورد نیاز این طرح است، تعداد دفعات تکرار آزمایش و وظایف آنها ذکر شود، بخشی از ویژگی های SCC و یا تمام آن از جمله سیالیت، قابلیت عبور، مقاومت بتن و ثبات و ویسکوزیته با هدف کنترل تولید و یا پذیرش آن در محل پروژه اندازه گیری می شود و هنگام انجام آزمایش به این ویژگی ها (به عنوان بخشی از برنامه کنترل کیفی) باید توجه خاصی مبذول داشت.
سیالیت
تامین حداقل میزان سیالیت و حفظ این میزان از ابتدای تولید تا بتن ریزی لازم و ضروری است. آزمون جریان اسلامپ، اندازه گیری استاندارد این ویژگی (سیالیت) می باشد. اگر چه این همواره در طرح های کنترل کیفی SCC وجود ندارد. محدوده حداقلی و حداکثری، همچنین دامنه پذیرش برای میزان جریان اسلامپ بستگی به ماهیت پروزه دارد. در فصل قبل رابطه بین جریان اسلامپ با دو ویژگی ثبات و پرداخت سطحی مورد بررسی قرار گرفت. در بعضی موارد باید حداکثر میزان جریان اسلامپ به منظور ایجاد اطمینان از پایداری در مخلوط مورد نظر بطور دقیق کنترل شود و این در مورد میزان بالای جریان اسلامپ مورد نظر بسیار اهمیت دارد. برای مثال اگر در یک پروژه میزان اسلامپ مورد نظر 600-500 میلی متر بوده و در پروزه ای دیگر این میزان 800-700 میلی متر باشد مخلوط با اسلامپ بالاتر قابلیت نوسان بالاتری داشته و باید بطور دقیق نظارت و کنترل شود. چنانچه یک پرداخت سطحی با کیفیت بالا مورد نیاز باشد باید مطمئن باشیم که میزان جریان اسلامپ به کمتر از حداقل میزان استاندارد کاهش پیدا نکند.
چنانچه میزان جریان اسلامپ از میزان هدف نیز پایین تر باشد فضاهای خالی در حین انجام پرداخت سطحی محبوس می شوند. دامنه ماکزیمم و مینیمم جریان اسلامپ باید در طی مرحله ی نسبت بندی مخلوط و ارزیابی، تعیین شود که در این صورت مخلوط با کیفیت مورد نظر تولید می شود. سه گروه ارائه شده در دستورالعمل های اروپایی SCC در زمینه میزان جریان اسلامپ شامل 180، 160 و 160 میلی متر برای کلاس های SF1 و 2 و 3 به ترتیب می باشد. این بدین معنی است که اگر میزان اسلامپ هدف در یک مخلوط در حد میانگین باشد میزان جریان هدف به ترتیب 90، 80 و 80 میلی متر خواهد بود.
قابلیت عبور
در صورت نیاز، آزمایش قابلیت عبور باید بخشی از طرح کنترل کیفی در پروژه باشد. روش های مختلفی از آزمایش قابلیت عبور انجام شد، شامل جعبه U، جعبه L و حلقه J. کلیه این آزمایش ها در این زمینه (قابلیت عبور) مورد استفاده قرار می گیرد. نویسنده قبلاً (در بخش روش های آزمون مورد نیاز) فهرستی ارائه نموده است. از آنجایی که کسانی که مشخصات آزمون را ثبت می کردند به جزئیات روش این آزمایش ها آشنا نبودند، لیست های متعددی ارائه می کردند که این برای تولید کننده و پیمانکار خشته کننده بود. در این موارد تحقیق و بررسی قبل از انجام پروژه در کنترل کیفی، مانع از بروز چنین مشکلاتی خواهد شد.
علاوه بر این آزمون ها، ابزاری شامل چندین مانع (در نقش آرماتور) برای انجام آزمایش قابلیت عبور جریان، در ژاپن طراحی شد. این وسیله بر روی یک قیف پمپ قرار می گیرد و مخلوط SCC از یک کامیون به داخل این وسیله تخلیه می شود و بتن باید از داخل این ابزار (وسیله) عبور کند. مزیت این روش استمرار آزمایش در انواع مخلوط SCC است که در بتن ریزی به کار می روند.
پایداری (مقاومت)
آزمون پایداری در محل یا در کارخانه، محدود به روش هایی است که با سرعت منطقی و بدون تاخیر در بتن ریزی انجام می شود. به همین دلیل ASTM اشاره می کند که آزمون تفکیک ستون در آزمایشگاه انجام می شود نه د رمحل بتن ریزی، شاخص ثبات بصری (چشمی) باید بخشی از برنامه کنترل کیفی باشد. اگر چه این روش آزمون محدود است، اما روشی آسان بوده و تجهیزات و زمان اضافی نیاز ندارد. اگر یک تکنسین آموزش دیده آزمایش VSI (شاخص ثبات بصری) را انجام دهد، می تواند اطلاعات مفیدی در رابطه با عملکرد مخلوط و یا مشکلاتی که ممکن است ایجاد شود به دست آورد. هدف اصلی VSI دقیقاً تحقق همین اهداف است و این آزمون ابزاری برای توصیف و سا سنجش کیفی پایداری نیست (حتی اگر اعداد و ارقامی به عنوان میزان شاخص چشمی ارائه شده باشد). این نتایج براساس مشاهدات صدها مخلوط SCC و آزمایش چشمی مخلوط، اطلاعات کاملاً واقعی را ارائه می دهد و ادعای دقیق نبودن این آزمون را باید فراموش کرد.
VSI یک روش ارزشمند برای نظارت بر تداوم ویژگی های تازه مخلوط می باشد. چنانچه VSI در طی مرحله تولید تغییر کند نشان دهنده این است که چیزی در حال تغییر است مخصوصاً زمانی که میزان جریان اسلامپ ثابت باشد.
ویسکوزیته
تغییر در ویسکوزیته مخلوط را می توان به وسیله استفاده از آزمایش T50 یا سایر آزمایش ها از قبیل قیف V و یا قیف O، تحت کنترل و نظارت قرار داد. در بین همه این آزمایش ها، آزمایش T50 از دقت کمتری برخوردار است، اما برای بتن ریزی در محل به زمان، کارگر و نیز تجهیزات کمتری نیاز دارد. آزمایش T50 ابزاری مناسب برای نظارت و کنترل بتن تولید و ارائه شده می باشد.
تحلیل مطالعات موردی
تعداد متعددی از آزمون ها می توانند به عنوان بخشی از برنامه های کنترل کیفی به کار گرفته شوند. اما چگونه می توان تشخیص داد که در یک پروژه کدام آزمایش را باید به کار برد؟ در بررسی تعداد متعددی از مطالعات موردی، برخی از آنها استفاده از برنامه آزمایش پذیرش در محل بتن ریزی را شرح می دهند. جدول -4 نشان دهنده نتایج حاصل از این بررسی است که به وسیله ارزیابی ویزگی ها و استفاده از روش ها برجسته می شود. با توجه به نمونه هایی از این مطالعات موردی، در می یابیم که ویژگی سیالیت و ویسکوزیته از جمله دو ویژگی مهمی هستند که بطور گسترده برای کنترل در محل کار مورد استفاده قرار می گیرند و از جمله آزمایش های معتبر تلقی می شوند. پایداری به ندرت از طریق روش آزمون ارزیابی کمی در محل اندازه گیری می شود. یکی از علل آن این است که قبلاً روش سریع و قابل اعتمادی برای ارزیابی کمی پایداری مخلوط در محل وجود نداشت تا اینکه آزمون ابزار نفوذ در این مورد معرفی شد. حال می توان کمیت پایداری یک مخلوط را با تلاش منطقی و دقیق به دست آورد. تا قبل از این VSI یکی از روش های اصلی برای سنجش کیفیت پایداری مخلوط SCC در طی مرحله تولید بوده و هست.
همان طور که قبلاً نیز ذکر شد، هر دو ویژگی جریان اسلامپ و ویسکوزیته با ثبات مرتبط هستند و برخی برای اطمینان از ایجاد پایداری به این رابطه تکیه می کنند.
علاوه بر مطالعات موردی، بیشتر دستورالعمل های منتشر شده در رابطه با SCC در راستای انجام آزمون بتن در کارخانه های تولیدی و یا در محل بتن ریزی است. موارد برجسته زیر از الزامات برای انتخاب دستورالعمل های قابل قبول در صنعت می باشد:
- توصیه برای بتن خود متراکم، انجمن دولتی مهندسین ژاپن (JSCE) توصیه می کند که تست جریان اسلامپ، T50 یا قیف V و تست جعبه U جهت کنترل تولید در کارخانه و همچنین در محل پروژه قبل از بتن ریزی انجام شود.
- دستورالعمل های اروپایی برای بتن خود متراکم، براساس این دستورالعمل ها توصیه می شود که تولید کننده، تست جریان اسلامپ بتن را در محل تولید بر روی هر بچینگ SCC انجام دهد تا به یک نتیجه ثابت برسد و بقیه تست ها را در هر زمان که مورد نیاز پروژه بود انجام دهد (مانند تست قابیلت عبور). بررسی چشمی در هر بچینگ قبل از حمل و ارسال بتن (حتی زمانی که جریان اسلامپ به پایداری رسیده باشد) انجام شود. ارزیابی تست های جریان اسلامپ و VSI در محل پروژه به عنوان نشانگر تفکیک توصیه می شود.
- کنترل آیین نامه کنترل کیفی برای کارخانه های بتن پیش ساخته/ پیش تنیده انجمن ملی بتن پیش ساخته (NPCA).
براساس این دستورالعمل ها توصیه می شود هر دو تست جریان اسلامپ و VSI برای تولید و آزمون پذیرش انجام شود. تست های جریان اسلامپ و VSI هر روز و بر روی اولین بچینگ مخلوط SCC و نیز بچینگ های بعدی در حیطه مشخصات فنی انجام شود.
پس از آن تست های جریان اسلامپ و VSI هر 50 یارد و یا 25 Batches (هر کدام زودتر پیش بیاید) و یا هنگام تغییر در طراحی ترکیب و یا مواد خام و یا زمانی که مشکلی پیش آید و یا مورد مشکوک در مخلوط دیده شود، انجام می گردد. باید تست های متعددی در کارخانه ها انجام شود (در کارخانه هایی که از تجهیزات اتوماتیک کنترل رطوبت سنگدانه ها استفاده نمی کنند).
- دستورالعمل های داخلی برای استفاده از بتن خود متراکم در کارخانه های عضو انجمن بتن پیش ساخته PCI, (PCI) توصیه می کند که برای تولید و آزمون پذیرش، آزمایش جریان اسلامپ و VSI انجام شود. تست T50 نیز یک تست گزینشی است که در یک ماه دو بار انجام می شود. تعداد دفعات لازم برای انجام تست های جریان اسلامپ و VSI همانند تعداد دفعات لازم انجام تست جریان اسلامپ در دستورالعمل های کنترل کیفی می باشد که شامل انجام تست در اولین روز شروع تولید، زمانی که نمونه ها تحت مقاومت فشاری قرار می گیرند و نیز زمانی که پایداری بتن دچار تغییر شود. در هر سه مورد، تست درصد هوا حداقل یک بار انجام شود.
دیگر موارد | فرکانس | ویسکوزیتی | استقامت | توانایی عبور | سیالیت | Ref |
| | | | | Slump flow | 14 |
| | | | | Slump flow | 14 |
| | | | | Slump flow | 14 |
| | | | | Slump flow | 14 |
آمپر متر برای کنترل تولید استفاده می شود | هر 70 مترمکعب | O-funnel | | Testing apparatus | Slump flow | 15 |
آمپر متر برای تولید استفاده می شود. | | T50 | | | Slump flow | 16 |
| هر 70 مترمکعب | O-funnel | | | Slump flow | 17 |
آمپر متر برای تولید استفاده می شود. | | T50 | | | Slump flow | 18 |
| | T50 | | | Slump flow | 19 |
| | T50 | | | Slump flow | 19 |
آمپر متر برای تولید استفاده می شود. | | T50 | | | Slump flow | 20 |
| | | | | Slump flow | 21 |
| | | | | Slump flow | 22 |
همچنین رئومتر برای بتن نیز استفاده می شود | | V-funnel | | Caisson test | Slump flow | 23 |
| | | Sieve and/or column segregation | | Slump flow | 24 |
| | T50 | | L-box | Slump flow | 25 |
| | V-funnel | | Kajima test | Slump flow | 26 |
یکی از L-box or J-ring یا V-funnel ها درخواست خواهند شد | | V-funnel | VSI | L-box or J-ring | Slump flow | 27 |
یکی از L-box or J-ring یا V-funnel ها درخواست خواهند شد | | V-funnel | VSI | L-box or J-ring | Slump flow | 27 |
یکی از L-box or J-ring یا V-funnel ها درخواست خواهند شد | | V-funnel | VSI | L-box or J-ring | Slump flow | 27 |
یکی از L-box or J-ring یا V-funnel ها درخواست خواهند شد | | V-funnel | VSI | L-box or J-ring | Slump flow | 27 |
جدول -4 روش ها و آزمون پذیرش سایت منتشر شده در موارد مطالعاتی
پیشنهادات بیشتر
دستورالعمل ها و مطالعات موردی که مورد بحث قرار گرفتند، همگی از جریان اسلامپ به عنوان بخشی از تولید و نیز آزمون پذیرش در محل کار استفاده کردند. بعضی از ارزیابی های ویسکوزیته بتن و آزمایش چشمی بتن به عنوان علائم ناپایداری اصولاً پیشنهاد می شود. عقیده نویسنده این است که وقتی جریان اسلامپ مورد آزمایش قرار می گیرد باید T50، VSI و نیز جریان اسلامپ همگی با هم گزارش شوند. زیبایی این عمل در این است که هنگام انجام تنها یک آزمایش جریان اسلامپ، سه ارزیابی با هم انجام می شوند. اگر میزان دقیقی از ویسکوزیته مورد نیاز باشد، آزمایش قیف O و یا V انجام می شود، مشابه زمانی که نیاز به اطلاعات دقیق در مورد پایداری بوده که از آزمایش ابزار نفوذ استفاده می شود.
وقتی این آزمایش ها با هم انجام می شودف یک ماتریس جریان اسلامپ، T50 و VSI می تواند مورد استفاده قرار گیرد. شکل -3 مثالی از یک ماتریس را ارائه می دهد که شامل یک محدوده هدف کلی جریان اسلامپ 650 تا 750 میلی متر و T50 با زمان s 5/2-1 می باشد و بیانگر این است که کنترل کیفی همراه با مشاهدات چشمی پی در پی توسط متخصص انجام گرفته و مورد تایید می باشد و بیانگر عملکرد خوب مخلوط است (تا زمانی که پایداری قابل پذیرش باشد). به منظور نشان دادن پایداری، 4 مورد از نتایج تست ارائه شده و اعداد در هر مرحله منطبق بر VSI مخلوط می باشد. VSI یک شاخص مهم ارزیابی در فرآیند عیب یابی در پروژه محسوب می شود. با استفاده از این ماتریس، تولید کننده قادر به مشاهده یک رابطه مناسب و دقیق میان سیالیت، ویسکوزیته و پایداری می باشد.
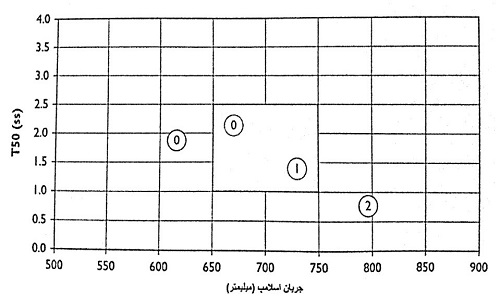
تصویر -3 ماتریس کنترل کیفی جریان اسلامپ، T50 و VSI
همان طور که تولید کننده این روابط را ایجاد کرده و داده ها را در تمام مدت جمع آوری می کند، این اطلاعات می تواند جهت خلق یک نمودار از تنظیمات مورد نیاز در مخلوط مورد استفاده قرار گیرد. این نمودار شامل همه مخلوط های SCC نمی شود. این وظیفه تولید کننده است که ابزاری مرتبط با مخلوط و مواد ایجاد کند. در این شرایط، چنانچه نتیجه پیمانه های آزمایش شده در مورد جریان اسلامپ و T50 به یک محدوده سایه روشن نزول کند، مخلوطی توسعه یافته و متمایز خواهیم داشت که در بخش تولید مورد استفاده قرار خواهد گرفت. (در این مورد میزان کمی کیفیت نیز خواهیم داشت). اما سایه متوسط بیانگر وجود توانایی برای تفکیک می باشد و محدوده سایه پر رنگ نشان دهنده این است که قدرت تفکیک نسبتاً بالا است.
جایی که مجموعه نتایج به دست آمده از آزمایش های مرتبط با محدوده هدف، دچار افت شده باشد، دستورالعمل های بیشتری جهت تنظیم پیمانه های بعدی برای دستیابی به جریان اسلامپ و T50 هدف ارائه شده است. این دستورالعمل های کلی، محدوده هدف را در داخل این نمودار در بر می گیرد. در ارتباط با محدوده (ناحیه) هدف، نواحی بالا، پایین، بالا به سمت راست و پایین به سمت چپ، نمایانگر محدوده هایی است که متغیرهای متعددی در آنجا فعل و انفعال انجام می دهند که موجب اختلال در رسیدن به هدف می شود و ممکن است ارائه راهکارهایی برای حل مشکل ضروری باشد. نواحی چپ، راست، بالا به سمت چپ و پایین به سمت راست نمایانگر محدوده ای است که توانایی انجام صریح تنظیمات به صورت بالقوه در آنجا وجود دارد و این جایی است که میزان دامنه VSI بیانگر این است که تنظیم ایجاد شده در مخلوط منطقی است. بنابراین آزمایش VSI بیانگر این است که تنظیم ایجاد شده در مخلوط منطقی است. بنابراین آزمایش VSI از این نقطه نظر بسیار مفید است.
برای مثال چنانچه یک پیمانه در محدوده بالا سمت چپ که باید پایدار باشد، علائمی از ناپایداری بروز دهد، پس تنظیمات ارائه شده در این ماتریس دقیق نمی باشد و لازم است بررسی های مفصلی در مورد وزن پیمانه، میزان رطوبت یا دیگر متغیرها انجام داد.
هر تولید کننده در صورتی که داده ها را بطور مستمر جمع آوری کرده و آنها را مرور کند قادر به ترسیم این نمودارها در مخلوط SCC می باشد. هنگام انجام آزمون جهت پایداری تولید، جریان اسلامپ، زمان T50 و VSI همگی شاخصی برای نشان دادن تغییرات مهم در عملکرد مخلوط می باشند. دیگر آزمون ها مانند تست هایی که ویژگی قابلیت عبور را نشان می دهند و یا آزمون هایی که پایداری را بطور دقیق تایید می کنند و یا آزمون ویسکوزیته مخلوط، همگی می توانند به برنامه کیفی به عنوان ملزومات پروژه اضافه شوند.
ارتباط میان آزمون کنترل کیفی و تولید
با کمی تلاش، تولید کننده قادر است اطلاعات برگرفته از ماتریس آزمایشات کنترل کیفی را با ماتریس پذیرش تولید که در فصل 10 معرفی شد مرتبط سازد.
در این ماتریس، میزان مصرف برقی که از میکسر بتن به دست می آید و میزان نسبت آب به سیمان که به وسیله دستگاه رطوبت سنج مشخص می شودبه ترتیب بر روی نمودار X و Y ترسیم شده است. مجدداً در این فرآیند کنترل کیفی، فرض کنید که تنها از یک گروه از نسبت های مخلوط استفاده می کنیم (بدون تنظیمات رادیکال و یا افزودن ترکیبات) و ویژگی مصالح نسبتاً ثابت است. در این مورد، این تصور کاملاً منطقی است که نسبت آب به پودر، زمان T50 (که نشانگر ویسکوزته مخلوط است) را به میزان قابل توجهی تحت تاثیر قرار می دهد. زمانی که میزان نسبت آب به پودر افزایش یا کاهش می یابد، زمان T50 (ویسکوزیته) به ترتیب کاهش و یا افزایش می یابد. برق کشیده شده توسط میکسر برای محاسبه جریان اسلامپ استفاده می شود. از آنجایی که ما تغییرات ویسکوزیته را پیش بینی و ارزیابی می کنیم، می توان تصور کرد که چنانچه برق کشیده شده در میکسر افزایش یابد، میزان جریان اسلامپ به ترتیب کاهش و یا افزایش می یابد. ارتباط میان یک میزان هدف T50 با نسبت آب به پودر و یا میزان آب، (بسته به بچینگ و سیستم ترکیب) و سپس ارتباط میان میزان هدف جریان اسلامپ و میزان برق کشیده شده توسط میکسر، اهداف مشخص و دقیقی را برای تولید و نیز کارکنان بخش مخلوط، ارائه می دهد.
داده ها حاکی از جایگاه متقابل در پذیرش تولید و ماتریس آزمایش کنترل کیفی می باشد.
ارزیابی داخلی ثبات تولید SCC
زمانی که SCC در مرحله تولید است، برنامه ریزی تولید کننده بتن برای ارائه طرحی در زمینه آزمایش، عملی بسیار ارزشمند است. زمانی که موسسه کنترل کیفیت به صورت تصادفی یک یا دو روز برای انجام آزمایش هایی در زمینه ویژگی های SCC از جمله سیالیت، پایداری، قابلیت عبور و نیز ویسکوزیته برای مخلوط مورد نظر، اختصاص می دهد. این اساساً به معنی ارزیابی تولید و فرآیند کنترل کیفی می باشد. نویسنده همراه با تولید کنندگان متعددی در چند مورد از این برنامه ها شرکت کرده است. این زیر مجموعه مثال هایی از میزان سطح ثبات مخلوط که هنگام استفاده و یا تولید SCC به راحتی تجربه می شود را تهیه می کند. سه مثال از تولید SCC در سه کارخانه تولیدات پیش ساخته مجزا (کارخانه A، B و C) نشان داده شده است.
برنامه آزمایش در دوره زمانی یک یا دو روزه و با حضور متخصصین انجام می شود. نمونه ها در تولید SCC به صورت تصادفی انتخاب شده اند. پیش از برنامه ارزیابی، هیچ ورودی به نسبت های مخلوط یا اهداف عملکرد اضافه نشده، اما بعد از برنامه ریزی توصیه هایی برای توسعه و بهبود مخلوط یا اهداف عملکرد اضافه نشده، اما بعد از برنامه ریزی توصیه هایی برای توسعه و بهبود مخلوط به تولید کنندگان ارائه شده است. آزمون های صورت یافته شامل جریان اسلامپ، T50، VSI، قیف V و ستون تفکیک می باشد.
کارخانه A قطعات دیواری پیش ساخته جهت ارائه در بازار مسکونی تولید می کند. قطعات به صورت قطعات افقی همراه با تعدادی باکس جهت پنجره ها و درگاه ها، ارائه می شود.
جدول -5 بیانگر اطلاعات جمع آوری شده در طی مرحله تولید است. اهداف عملکرد برای کارخانه A تنها به وسیله جریان اسلامپ با میزان هدف 550 تا 650 میلی متر تعریف می شود. در طی برنامه آزمایش در کارخانه A، امکان انجام آزمایش ستون تفکیک بر روی همان نمونه هایی که برای سایر ویزگی ها مورد آزمایش قرار می گیرند، وجود ندارد. بنابراین هیچ تحلیل بر روی این داده ها انجام نمی شود، به استثناء این مورد که بگوییم دو پیمانه آزمایش شده از پایداری خوبی برخوردارند.
جدول -6 یک آنالیز آماری از انسجام (پایداری) تولید و براساس یک سری از داده ها، ارائه می دهد. باید یادآوری کرد که نتایج حاصل از این تجزیه و تحلیل و نیز نتایج مطالعات بعدی، به وسیله تغییرپذیری آزمایش و تولید، تحت تاثیر قرار می گیرد. نتایج حاصل از آزمون قیف V در این مثال، نشان می دهد که میزان ثابت به اندازه سطح انتظار ما نیست، به هر حال براساس نتایج حاصل از آزمایش پایداری (ثبات) جریان اسلامپ و T50، تغییر پذیری تست قیف V بیشتر تحت تاثیر اشتباهات آزمایش است تا اشتباهات تولید. ارزیابی جریان اسلامپ و T50 بسیار منسجم و ثابت است. ترکیب نتایج حاصل از این تست ها با تست ستون تفکیک و VSI، کنترل تولید و کیفیت SCC در کارخانه A بسیار خوب است.
8 | 7 | 6 | 5 | 4 | 3 | 2 | 1 | Batch |
NA | NA | 585 | 560 | 570 | 595 | 585 | 595 | جریان اسلامپ (میلی متر) |
NA | NA | 0 | 0 | 0 | 0 | 0 | 0 | VSI |
NA | NA | 5.42 | 5.63 | 5.22 | 4.88 | 5.43 | 5.01 | T50 (s) |
NA | NA | 540 | 515 | 525 | 545 | 535 | 535 | J-ring (mm) |
NA | NA | 45 | 45 | 45 | 50 | 50 | 65 | J-ring difference (mm) |
NA | NA | 6.97 | 6.63 | 9.47 | 5.22 | 7.22 | 7.02 | V-Funnel (s) |
1.9 | 2.8 | NA | NA | NA | NA | NA | NA | تفکیک ستون (%) |
جدول -5 داده های تولید کارخانه A
کارخانه B تولید کننده قطعات دیواری برای ساختمان های تجاری، با میزان جریان اسلامپ 550 تا 650 میلی متر تنها هدف عملکرد SCC می باشد که برای تولید کارخانه B در نظر گرفته شده است. اولین Batch (پیمانه) در جدول -7 نشان داده شده است که میزان جریان اسلامپ پایین تر از میزان هدف است.
T50 (s) | J-ring difference (mm) | Slump flow (mm) | V-funnel (s) | |
5.27 | 50 | 582 | 7.09 | حد وسط |
0.28 | 8 | 14 | 1.37 | انحراف معیار |
0.75 | 20 | 35 | 4.25 | محدوده |
4.88 | 45 | 560 | 5.22 | حداقل |
5.63 | 65 | 595 | 9.47 | حداکثر |
5% | 15% | 2% | 19% | ضریب تغییر |
جدول -6 داده تولید SCC براساس آنالیز آماری کارخانه A
T50 (s) | J-ring difference (mm) | Slump flow (mm) | V-funnel (s) | |
5.27 | 50 | 582 | 7.09 | حد وسط |
0.28 | 8 | 14 | 1.37 | انحراف معیار |
0.75 | 20 | 35 | 4.25 | محدوده |
4.88 | 45 | 560 | 5.22 | حداقل |
5.63 | 65 | 595 | 9.47 | حداکثر |
5% | 15% | 2% | 19% | ضریب تغییر |
جدول -7 داده های تولید کارخانه B
تنظیمات پیمانه های بعدی انجام شده، دامنه جریان اسلامپ افزایش می یابد و به بیش از میزان سطح انتظار ما می رسد، زمان های T50 و قیف V کاهش می یابند و درصد تفکیک ستون و VSI افزایش می یابد. زمانی که جریان اسلامپ بسیار پایدار شود (پایداری بیش از حد) و به زیر دامنه هدف کاهش پیدا می کند، تنظیم دوم انجام می شود. به انتهای بتن ریزی که نزدیک می شویم، جریان اسلامپ به تدریج شروع به افزایش می کند و میزان قیف V و T50 پایین می آیند و این موجب می شود که پایداری مخلوط کمی کاهش یابد (همان طور که در تست تفکیک ستون و VSI نیز دیده می شود).
جدول -8 نشان دهنده یک آنالیز آماری از تولید SCC از کارخانه B می باشد. تجزیه و تحلیل کلی تولید کارخانه B نشان می دهد کنترلی منطقی در آنجا وجود دارد. اگر چه ضریب متغیر آزمون تفکیک ستون بالا می باشد اما میزان دامنه تغییر پذیری منطقی است. به هر حال به این کارخانه توصیه شده که فرآیند را مورد بررسی قرار دهند بطوری که زمان و نحوه انجام تنظیمات، پیمانه به پیمانه در طول مرحله تولید، مشخص شود. همچنین باید توجه خاصی به بچینگ های اولیه روزانه مبذول داشت.
کارخانه C تولید کننده Double-Tee پیش تنیده می باشد و تنها هدف عملکردی تولید آنها دامنه اسلامپ 500 تا 600 میلی متر می باشد و در این شرایط بتن از کارگاه تولید، به وسیله میکسر به داخل قالب بتن ریزی منتقل می شود. جدول 11-9 نشان دهنده اطلاعات جمع آوری شده از تولید می باشد. Batchهای اول، سوم و چهارم در بیرون از کارخانه تولید بتن به حداقل هدف جریان اسلامپ نرسیدند. در این شرایط جهت افزایش جریان اسلامپ بعد از انجام آزمایش ویزگی تازه بر روی نمونه ها و نیز قبل از بتن ریزی به این سه Batch (پیمانه) آب اضافه می شود. ولی این روند در مورد SCC توصیه نمی شود. چنانچه هر گونه تنظیم و تعدیل در جریان اسلامپ لازم باشد، توصیه می شود که این عمل همراه با افزودنی HRWR انجام شود و مجدداً مورد آزمایش قرار گیرد، بطوری که نتایج به دست آمده بطور دقیق ثبت گردد.
T50 (s) | J-ring difference (mm) | Slump flow (mm) | V-funnel (s) | درصد تفکیک ستون | |
1.12 | 30 | 613 | 1.9 | 7.63 | حد وسط |
0.15 | 7 | 54 | 0.15 | 2.32 | انحراف معیار |
0.40 | 15 | 160 | 0.45 | 6.5 | محدوده |
0.90 | 25 | 500 | 1.67 | 4.2 | حداقل |
1.30 | 40 | 660 | 2.12 | 10.7 | حداکثر |
13% | 24% | 9% | 8% | 30% | ضریب تغییر |
جدول -8 داده های تولید SCC براساس تحلیل آماری کارخانه B
7 | 6 | 5 | 4 | 3 | 2 | 1 | Batch |
570 | 585 | 545 | 440 | 470 | 510 | 380 | جریان اسلامپ (میلی متر) |
0 | 0 | 0 | NA | NA | 0 | NA | VSI |
3.05 | 2.87 | 3.11 | NA | NA | 3.23 | NA | T50 (s) |
525 | 535 | 470 | NA | NA | 430 | NA | J-ring (mm) |
45 | 50 | 75 | NA | NA | 75 | NA | J-ring difference (mm) |
4.11 | 3.58 | 4.42 | NA | NA | 4.68 | NA | V-Funnel (s) |
10.6 | 11.3 | 9.1 | NA | NA | 5.1 | NA | تفکیک ستون (%) |
جدول -9 داده های تولید کارخانه C
جدول -10 بیانگر یک تحلیل آماری از اطلاعات جمع آوری شده می باشد، از آنجایی که این سه پیمانه به عملکرد حداقل مورد نیاز دست نیافتند. تعدادی از نتایج به دست آمده از چندین مورد روش آزمون صرفاً به چهار نمونه محدود می شود.
بطور کلی پایداری تولید در کارخانه C پایین بوده و نیاز به بهبود دارد. توصیه می شود ارزیابی بیشتری
بر روی برنامه کنترل کیفی کلی از جمله کنترل مواد انجام شود.
توصیه دیگر اختلاط مجدد مخلوط SCC با آب می باشد و توصیه آخر این که همه کارخانه ها باید دارای VSI و T50 به عنوان اهدافی برای تولید باشند. عقیده نویسنده این است که جریان اسلامپ به تنهایی کافی نیست.
T50 (s) | J-ring difference (mm) | Slump flow (mm) | V-funnel (s) | درصد تفکیک ستون | |
3.07 | 61 | 500 | 4.2 | 9.1 | حد وسط |
0.15 | 16 | 74 | 0.47 | 2.76 | انحراف معیار |
0.36 | 30 | 205 | 1.1 | 6.13 | محدوده |
2.87 | 45 | 380 | 3.58 | 5.13 | حداقل |
3.23 | 75 | 585 | 4.68 | 11.26 | حداکثر |
5% | 26% | 15% | 11% | 30% | ضریب تغییر |
جدول -10 آنالیز آماری داده های تولید کارخانه C
نتایج حاصل از کارخانه C به وسیله لوزی های سایه دار مشخص شده اند. جهت تضمین پایداری، میزان جریان اسلامپ هدف 500 تا 550 میلی متر و زمان T50، s4-3 می باشد. این اهداف، به خصوص میزان 50 میلی متری جریان اسلامپ برای کارخانه C کاملاً محدود کننده است که در ترکیب با نتایج ارزیابی، پیشنهاد می شود کارخانه C فوراً زمانی را صرف بهبود برنامه SCC خود نماید. ایجاد تنظیمات مخلوط و همچنین توسعه فرآیند کنترل کیفی مخلوط نسبتاً ضروری می باشد.
خلاصه
فرآیند کنترل کیفی به معنی یک فرآیند یکپارچه و بدون شکاف است (از کنترل مواد خام گرفته تا آزمون پذیرش در محل بتن ریزی). این فرآیند عملکرد مورد انتظار بتن را در خصوص تازگی و سخت شوندگی تضمین می کند. علاوه بر برنامه های کنترل کیفی معمول، پیشنهادات در خصوص کنترل کیفی SCC شامل موارد زیر می باشد:
- نظارت و کنترل بر مواد، شامل سنگدانه های ریز و مواد پودری، درصد مواد عبوری از الک 75 و 300 میکرومتر در سنگدانه های ریز، اندازه فضای خالی بین ترکیب سنگدانه های مورد استفاده در مخلوط و نیز کنترل رطوبت در سنگدانه های ریز و درشت.
- کنترل ویزگی های تازه تولید شامل اندازه گیری مناسب و استفاده از تجهیزات کنترل تولید مانند آمپرسنج، میکسر و رطوبت سنج اتوماتیک (که یا سنگدانه را اندازه گیری می کند و یا رطوبت پیمانه های بتن را) می باشد. اولین بچینگ روزانه باید آزمایش شود و به دنبال آن همه بچینگ ها تا جایی که دو بچینگ متوالی به اهداف عملکرد تازه برسند.
داده های آزمون ها باید با گذشته نیز مرتبط باشند که شامل تجهیزات کنترل تولید در یک فرآیند مستمر به منظور اصلاح اهداف تجهیزات تولید می باشد.
- چنانچه تجهیزات اتوماتیک جهت کنترل رطوبت و یا تولید در دسترس نباشد، باید طرحی شامل آزمایش بتن اضافی جایگزین شود. در مورد بتن آماده در این شرایط میزان جریان اسلامپ باید قبل از افزودن HRWR اندازه گیری شود و بعد از افزودن HRWR میزان جریان اسلامپ، T50 و VSI (با مجموعه دیگری از تست ها، در حیطه کنترل سیالیت، ویسکوزیته و پایداری) باید قبل از این که میکسر کارخانه را ترک کند اندازه گیری شود. در مورد تولیدات پیش ساخته در این شرایط، بعد از تخلیه بتن امکان انجام تنظیمات وجود ندارد. کنترل و بازبینی بتن در میکسر، علیرغم صرف وقت زیاد، جهت حمل در مسیرهای طولانی ارزشمند است. هرگونه کنترل و بازبینی در این مسیر باید به منظور تضمین کامل ایمنی افرادی که در این زمینه فعالیت دارند، انجام شود. تعداد دفعات آزمایش بتن اضافی، باید به نحوی بوده که در ابتدا بیشتر باشد تا وقتی که یک سابقه زمانی در تولید و کنترل حاصل شود. اما مخلوط SCC باید حداقل روزانه دو یا سه بار بیشتر آزمایش شود تا زمانی که مخلوط به پایداری برسد.
- اگر قابلیت عبور، یک ویژگی عملکردی حیاتی برای پروژه است، پس کنترل و نظارت بر این ویژگی نیز لازم است.
- آزمون پذیرش در محل باید شامل آزمون هایی باشد که متعلق به ضروریات پروژه باشند، باید از انجام چندین روش آزمون که برای کنترل ویژگی های مشابه و یکسان به کار می رود خودداری کرد. مانند استفاده از هر دو تست حلقه J و جعبه L و در حال حاضر دست کم استفاده از ارزیابی جریان اسلامپ، T50 و VSI مورد تایید و مطلوب است و با این روش یک ارتباط مستقیم میان ارزیابی های کارخانه و محل بتن ریزی ایجاد می شود.
- یک برنامه ارزیابی تولید داخلی، جایی است که آزمایش های سیالیت، قابلیت عبور، پایداری و ویسکوزیته بر روی بتن تولیدی انجام می شود، همچنین ایمنی را در محل پروژه SCC و برنامه کنترل کیفی را نیز ارزیابی می کند.
جهت اطلاعات بیشتر در زمینه تولید و فروش بتن و محصولات مرتبط و همچنین اطلاع از قیمت روز بتن می توانید با شرکت مهندسین مشاور مهرازان پایدار با نام نشان تجاری ثبت شده کلینیک بتن ایران با شماره 02145872 واحد مهندسی تماس حاصل نموده و یا جهت اطلاعات بیشتر در این زمینه به وب سایت رسمی شرکت WWW.CLINICBETON.IRمراجعه فرمایید.
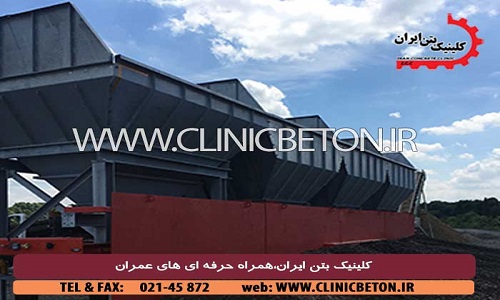