عیب یابی بتن
یک فناوری جدید، تکنیک یا قطعه ای از دستگاه در داخل فرآیند فعلی وجود دارد و به صورت غیرقابل اجتناب یک نتیجه غیرقابل پیش بینی رخ می دهد. زمانی که این مورد اتفاق می افتد، می توان به یکی از 3 روش اساسی زیر عمل کرد:
- بلافاصله کاربرد فناوری جدید را متوقف و به فرآیند قدیمی بر گردید، بدون قصد آزمون مجدد فناوری جدید.
- استفاده مستمر از تکنولوژی به همان روش قبلی و امید داشتن به اینکه نتیجه پیش بینی نشده (اگر منفی باشد) مجدداً اتفاق نم یافتد.
- بررسی اینکه چرا این نتیجه به دست آمده، جهت جلوگیری از تکرار آن (اگر منفی باشد) یا نحوه تکرار، آن را با هدف اجرای کامل فناوری بیاموزید.
از این گزینه ها، گزینه نخست حقیقتاً زمانی که تکنولوزی مقادیر واقعی را به کاربر ارائه دهد، گزینه مورد نظر نیست. بدین صورت، عدم توجه به یک مسئله به این امید که حل خواهد شد گزینه ی درستی نیست. در موردی که تکنولوزی دارای مقادیر است، بهترین واکنش حرکت رو به جلو و ادامه کاربرد فناوری است، زیرا که نتایج مطلوب، پیوسته قابل دستیابی است.
هر فردی که SCC را اجرا می کند ناگزیر نتایجه پیش بینی شده ای را در بعضی موارد تجربه خواهد کرد. کسب آمادگی برای بررسی یک نتیجه پیش بینی شده ضروری است. این بخش به ارائه فرآیند کلی عیب یابی، بررسی مطالعات موردی عیب یابی و در نهایت ارائه یک دستورالعمل کاربردی برای مسائل مشترک عیب یابی SCC می پردازد.
فرآیند عیب یابی
بازنگری فرآیند عیب یابی ممکن است در ظاهر برای گروهی یک بازنگری مقدماتی باشد. به هر حال، هر چقدر که در موضوع خدمات فنی میدانی بیشتر وارد شویم، بیشتر متوجه خواهیم شد که نتیجه گیری بطور مستمر صورت می گیرد و تصمیمات براساس شواهد سطحی اتخاذ می شوند و نهایتاً منجر به طرح سوالی می شود که هنوز به آن پاسخ داده نشده است. زمانی که یک نتیجه غیر منتظره به بار می آید، یک روش سیستماتیک، براساس روش علمی، غالباً یه صورت کارآمد علت را مشخص خواهد کرد.
موارد زیر مراحل کار فرآیند عیب یابی می باشند:
- گردآوری تمام داده های کمی و کیفی مرتبط با نتیجه، این شامل (اما نه صرفاً محدود به این موارد) داده های تولید بتن و آزمون بتنی، داده های مربوط به بتن ریزی از قبیل تغییرات فشار پمپ در طول بتن ریزی و تفاوت های عملکرد مخلوط مشاهده شده (که از سوی کارگران در محل بتن ریزی گزارش شده) می گردد. در مورد اهمیت هر یک از بخش هایی که در داده ها ارائه شده قضاوت نکنید. احتمالاً اطلاعاتی که در ظاهر امر در ابتدای فرآیند عیب یابی اهمیت ندارند ممکن است در نتیجه گیری پایان این فرآیند موثر و مفید باشد.
- این سوال را مطرح کنید: «دلایل کلی بالقوه این مسئله چیست؟» و یک لیست از تمامی دلایل بالقوه آماده نمایید. اهمیت این موضوع به این دلیل است که (تا جایی که همیشه دوست داریم یک علت وجود داشته باشد) در بعضی از موارد احتمالاً چندین عامل در نتیجه پیش بینی نشده دخیل هستند.
- از داده های جمع آوری شده و دلایل بالقوه، یک یا چند فرضیه را برای توصیف رویداد طرح کنید.
- در موردی که داده های جمع آوری شده در طول تولید ناکافی باشد، آزمایشی برای ارزیابی فرضیه انجام دهید، آزمایش می تواند به اندازه ایجاد تغییر در فرآیندهای میدانی ه کار رفته و مشاهده نتایج ساده باشد، یا می تواند به اندازه انجام آزمون آزمایشگاهی کنترل شده دقیق باشد. در مواردی که داده های کافی جمع آوری شده باشد، ممکن است نیازی به آزمایش نباشد و توصیف منطقی و دستورالعمل به جا میتواند اعمال گردد. در هر صورت باید یک رویکرد سیستماتیک به کار گرفته شود مگر اینکه علت ضرب المثل (Smoking Gun) بلافاصله یافت شود که در مورد عیب یابی موضوعات عملکرد بتن پدیده ی کاملاً نادری است.
- تایید یا رد این فرضیه و در صورت لزوم ایجاد یک نمونه جدید مبتنی بر داده های جدید.
جمع آوری داده ها و اطلاعات
خواه یک آزمایش انجام شود یا خبر، داده ها باید هر نوع مشکلی را حل کنند. فرآیند کنترل کیفیت که قبلاً بحث و بررسی شد، فرد را برای عیب یابی نتایج پیش بینی نشده آماده می کند. با این وجود داده های کنترل کیفیت جمع آوری شده باید به اندازه کافی متنوع باشند تا امکان شناسایی مشکل را فراهم آورند. در این صورت تمام اطلاعات به صورت بالقوه مفید است بطوری که فرد محقق باید تمامی اطلاعات موجود را جمع آوری کند (خواه کمی بوده یا کیفی). این فرآیند مترادف با حل یک پازل تصویری است. اگر فرد صرفاً دارای یک قطعه واحد از پازل باشد، توصیف کل تصویر دشوار است. هر چقدر که قطعات پازل بیشتری گردآوری شود، احتمال هماهنگی آنها بیشتر می شود و مشخصاً یک بخش از کل تصویر را به نمایش می گذارد. در ابتدای تحقیق، زمانی که داده ها در ابتدا در دسترس نباشند، بسیاری از سوالات در زمینه ماهیت کلی مطرح می شود، از قبیل اینکه آیا این مسئله قبلاً اتفاق افتاده بود؟ اگر پاسخ مثبت باشد باید به سابقه زمانی، علت و نحوه وقوع آن پرداخت. ضمناً فرد باید بداند که یک مسئله چگونه رخ می دهد، آیا در هر پیمانه بتن یا در طول هر بتن ریزی اتفاق می افتد؟ آیا در یک زمان مشخص روز یا سال رخ می دهد یا بعد از بارندگی یا زمانی که هوا خشک و آفتابی است؟ آیا صرفاً به صورت منقطع رخ می دهد؟ مشکلات منقطع یا ناهماهنگ اغلب به دشواری حل می شوند. زمانی که یک مشکل به صو��ت ثابت ایجاد می شود، بدین معنی است که علت آن به احتمال زیاد ثابت بوده و نهایتاً یافتن علت آن تا حدودی ساده تر است. فرآیند طرح سوال به تعیین چهارچوب و ایجاد مرزهایی برای حل مشکلات کمک می کند. زمانی که مرزها ایجاد می شوند سوالات مشخصی مطرح می شود، برای نمونه " آیا اخیراً انتقال مصالح یا مواد خام جدید صورت گرفته است (سیمان، سایر پودرها، مصالح ریز، مصلح درشت، ماده افزودنی)؟ " مشابه با یک مکانیک خودرو و یا یک پزشک، کارشناس از طرح سوال در یک فرآیند حذف، بهره می برد. اگر دلایل بالقوه بتوانند از طریق طرح سوال با یک میزان منطقی اعتماد حذف شوند، فرآیند یافتن دلیل نهایی، کوچکتر شده و به راحتی قابل کنترل می گردد.
همانند بتن معمولی، عیب یابی ممکن است برای SCC در حالت تازه یا سخت شدگی ضرورت داشته باشد، بنابراین داشتن شناخت و اطلاعات از متغیرهایی موثر و مفید است که بر ویژگی های معین SCC تاثیر میگذارند. ضمناً داشتن تجربه در تجهیزات تولید بتن و فرآیند آن و همچنین فرآیند بتن ریزی و کاربرد آن مفید است. داشتن تجربه گوناگون، نگرش چندگانه ای را به محقق ارائه می دهد که از طریق آنها به مشکل نگاه می کند.
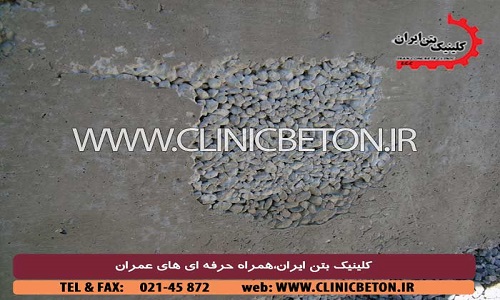
عیب یابی ویژگی های SCC تازه
ویژگی های تازه SCC برای استفاده موفق از آن اهمیت فراوانی دارد. زمانی که یک موضوع مطرح می شود، یکی از مراحل نخست، گردآوری برچسب پیمانه و تایید این نکته است که مخلوط به درستی پیمانه شده است. این باید شامل تاییدیه تنظیمات رطوبت مصالح انجام شده باشد. این بخش به بازنگری بعضی از مشکلات عملکرد تازه می پردازد. در موضوع عیب یابی فرض بر این است که SCC با ویژگی های خوب ارائه شده و در حال حاضر در فرآیند تولید قرار دارد.
جریان اسلامپ زمانی افزایش نمی یابد که HRWR بیشتری اضافه شود. در بعضی از نمونه ها، بعد از آنکه یک مخلوط نسبت بندی گردید، تولید کنندگان یک عدم توانایی در افزایش جریان اسلامپ را گزارش نموده اند (بدون توجه به میزان افزایش HRWR). دو مورد اصلی باید در این موقعیت مدنظر قرار گیرد: نخست HRWR سیالیت خمیر سیمان را افزایش می دهد و دوم اینکه، ارتباط بین حجم خمیر و خواص سنگدانه ها تعیین کننده سیالیت مخلوط بتن است. اگر حجم خمیر این مخلوط بسیار پایین باشد، ممکن است در معرض نوسان کیفی قرار داشته باشد که باعث تماس بین ذره ای اضافی خواهد شد و مانع سیالیت بتن می گردد. در این فرآیند افزایش HRWR صرفاً یک خمیر گسسته را شکل می دهد و همین امر منجر به ناپایداری مخلوط می شود، به علاوه اگر اساساً با یک محتوی آب بسیار کمتر و یک مقدار بالای HRWR طراحی گردد، می توان به نقطه ای دست یافت که مخلوط نمی تواند با مواد افزودنی اضافی پراکنده گردد. این مخلوط ممکن است تحت تاثیر محاسبات غلط رطوبت قرار داشته باشد. در هر یک از این موارد، این موضوع مربوط به نسبت بندی مخلوط است. این مخلوط ها با قدرتمندی ناکافی ساخته شده اند. قدرتمندی باید در طول فرآیند ساخت مخلوط ارزیابی شود، طوری که SCC قادر باشد تا عملکرد مطلوبی را در زمان ایجاد تغییر نرمال در مواد داشته باشد.
جریان اسلامپ از کارخانه تا محل پروژه در حال افزایش است
مقدار HRWR نیازمند یک جریان اسلامپ معین است که در طول فرآیند ساخت مخلوط تعیین می شود. اگر در طول تولید این مقدار به میزان قابل توجهی بیش از طرح مورد نظر افزایش یابد، می تواند منجر به افزایش جریان اسلامپ در طول انتقال شود. دلایل یک افزایش مقدار شامل تغییرات مواد، تغییرات دما و رطوبت های نادرست می باشد که متعارف ترین آن مقادیر رطوبت پیش بینی نشده است. اگر رطوبت سطحی آزاد بیش از حد برآورد شود، میزان کمی آب شکل خواهد گرفت که احتمالاً نیازمند مخلوط سازی طولانی تر برای پایدار سازی ویژگی های مخلوط است. اگر این مدت زمان اضافه پیش بینی نشود، پس جریان اسلامپ اندازه گیری شده در کارخانه ممکن است کمتر از جریان اندازه گیری شده در محل پروژه (بتن ریزی) باشد.
یک مخلوط پایدار قبلی در حال حاضر علائم تفکیک را نشان می دهد
اغلب جداشدگی به عنوان مشکل SCC تازه گزارش شده است. اگر یک مخلوط در حال تفکیک باشد باید به نوع جدا شدن توجه کرد، بعضی از مخلوط ها بلافاصله جداشدگی را نشان می دهند، درحالی که سایر مخلوط ها با تاخیر دچار تفکیک می شوند. اگر مخلوط بلافاصله جدا شود (کمتر از 30 ثانیه) بیانگر ویسکوزیته پایین خمیر است که بطور معمول ناشی از آب اضافی است. در این نقطه محتویات آب و رطوبت های مصالح باید کنترل شود. جداشدگی با تاخیر می تواند زمانی مشاهده شود که جداشدگی سریع رخ نمی دهد و مخلوط در فرغون به صورت بی حرکت قرار دارد. ظرف 2-1 دقیقه قسمت فوقانی بتن با خمیر یا ترکیب بدون رنگ پوشانده می شود. این جداشدگی با تاخیر اغلب مربوط به خمیر با ویسکوزیته بالا و افزایش مقدار بالای HRWR می باشد. اگر مخلوط حاوی جریان اسلامپی بالاتر از حد ماکزیمم باشد، باید مقدار HRWR را کاهش داده و آن را اندازه گیری کرد. اگر مخلوط حاوی جریان اسلامپی باشد که در حد نرمال قرار دارد، باید رطوبت را کنترل کرد که در حد نرمال باشد، اگر همه آنها در شرایط نرمال باشند، ممکن است در مصالح تغییراتی رخ داده باشد و تنظیم در نسبت بندی مخلوط ممکن است ضروری باشد.
عیب یابی ویژگی های SCC سخت شده
یک پرداخت سطحی شکل دار درست، یکی از مزایای پیش بینی شده کاربرد SCC است. از نقطه نظر تجربه مولف، مشکل اصلی گزارش شده در خصوص SCC در حالت سخت شدگی نواقص در پرداخت سطحی است. این مشکل می تواند به روش های گوناگون مشاهده شود و هر یک از آنها در بخش های زیر مورد بحث و بررسی قرار خواهند گرفت.
رگه ای شدن شن و ماسه و مجاری آبدهی
این رویدادها در اجرای بتن ریزی رخ می دهند، جایی که آثار تراوش آب می تواند به صورت عمودی در سطح قالب گیری شده مشاهده شود. این اثر معمولاً فاقد خمیر است و صرفاً مصالح (به ویژه سنگدانه های ریز) قابل مشاهده هستند. این رفتار نیازمند آب زیادی یا در درون مخلوط است که بتواند به سطح قالب برسد و یا در درون قالب (قبل از بتن ریزی).
اگر رگه ای شدن ماسه به دلیل آب اضافی در مخلوط رخ دهد، SCC ظاهراً به تفکیک نزدیک می شود و احتمالاً در حیطه زمانی T50 بسیار پایین (سریع) رخ می دهد. در یک مورد که در آن خود مولف حضور داشتند، یک دیوار ماکت از طریق پمپاژ بتن ریزی شد، قبل از پر کردن پمپ با SCC، یک ملات بسیار سیال از درون پمپ عبور داده شد. مقداری از آن ملات در شیلنگ پمپ در شروع پمپاژ باقی مانده بود که به درون قالب تخلیه شد. زمانی که بتن در مرکز قالب قرار گرفت، ملات بسیار سیال بتن را به بخش انتهایی دیوار ماکت رساند که منجر به آبدهی در هر یک از بخش ها گردید. رگه ای شدن ماسه می تواند حاصل تاخیر طولانی در گیرش بتن باشد، جایی که مخلوط برای مدت زمان طولانی بعد از جایگیری سیال باقی می ماند.
حفره های سطحی
حفره های سطح قالب ریزی شده یک بخش عمودی می تواند ناشی از علل متعددی باشد از جمله ویژگی های مخلوط، عامل رها ساز قالب و تکنیک بتن ریزی. در بعضی از موارد، یک آنالیز ویژگی های حفره ها موثر است. حفره های نامنظم می توانند در سطح به دام بیافتند (به دلیل ویژگی های جریان ضعیف مخلوط SCC یا تکنیک های بتن ریزی ضعیف). ویزگی های جریان ضعیف می توانند نتیجه یک جریان اسلامپ بسیار پایین، ویسکوزیته بسیار بالا یا خمیر ناکافی باشند. بتن ریزی سریع و سقوط آزاد SCC می توانند هوا را به درون مخلوط بکشند و این هوا نیز در سطح قالب محبوس می شود. بازنگری تکنیک بتن ریزی، اهداف عملکرد مخلوط و نسبت های تعیین شده، بسته به تعداد این رویداد، می توانند ضروری باشند. SCC با عملکرد خوب هرگز منجر به این نوع حفره های سطحی نمی شود حتی زمانی که پرداخت های سطحی یا کیفیت بالا مدنظر نباشند.
حفره های متقارن مدور کوچک معمولاً نتیجه حباب های هوا بوده که بر روی سطح بتن می آیند. براساس تجربه مولف، دلیل اصلی این پدیده، ناپایداری است. به تعداد زیاد حباب های متقارن در سطح نیز توجه کنید. اگر این بتن درون یک قالب ریخته شود، حباب ها می توانند به سطح قالب هدایت شده و حفره های مدور و کوچک را بر جای گذارند. در بعضی از نمونه ها حفره های سطحی به واسطه مدل سازی قابل مشاهده نیستند و زمانی مشاهده می شوند که اجزاء، شن زنی شده یا اسیدشویی شده باشند. این ممکن است یک عملکرد ماده رهاساز قالب باشد و نه تفاوت در مخلوط SCC. گزارش حاکی از این است که عامل رهاساز قالب با پایه آب می تواند در بعضی از موارد عامل تشکیل یک لایه خمیر نازک در میان قالب بتن باشند. این لایه نازک، حفره ها را می پوشاند و زمانی که این لایه برداشته می شود حفره ها مشاهده می شوند. اگر این حفره ها ظاهر شوند، مخلوط باید برای پایداری مورد ارزیابی قرار گیرد.
خطوط بتن ریزی
مشابه با بتن معمولی، خطوط موجود روی یک سطح در صورتی می تواند رخ دهد که دو بتن ریزی متوالی یکدیگر را همپوشانی نکنند در بدترین این شرایط، اتصالات سرد می تواند رخ دهد اما بیشتر اوقات این خطوط بتن ریزی از ماهیت تزئینی برخوردارند، گرچه این باید در تمام موارد ارزیابی شود.
خطوط بتن ریزی معمولاً ناشی از ترکیب های تاخیر در بتن ریزی و یا یک ویژگی تیکسوتروپیک یا حفظ جریان اسلامپ ناکافی مخلوط SCC می باشد. مخلوط هایی با نسبت پودر به آب پایین (W/P) و محتویات بالای پودر ممکن است، تمایل به تیکسوتروپیک داشته باشند. به همین دلیل، SCC برای ویژگی های قالبیت عبور وابسته به زمان، در طول مرحله آماده سازی مخلوط، آزمایش شود. اگر مخلوط بتن ریزی رخ دهد، مخلوط باید برای تیسکوتروپیک و برای حفظ جریان اسلامپ مجدداً مورد آزمایش قرار بگیرد. اگر این ویژگی ها وجود داشته باشند اما در طول مرحله ماده سازی مشاهده نشوند، می توان آنچه را که تغییر کرده مورد بررسی قرار داد. محیط بالاتر از میزان پیش بینی شده و درجه حرارت بتن می توانند بر این رفتار تاثیر گذار باشند و باید ثبت شوند. درجه حرارت خود قالب ها بخصوص اگر بتن ریزی در بیرون انجام گیرد می تواند به سفت شدن سریع بتن کمک کند.
لانه زنبوری شدن یا حفره های بزرگ این حالت ها به طور معمول ناشی از توانایی انتقال ضعیف و یا فقدان سیالیت مخلوط است. این مخلوط باید برای هر دوی این ویژگی ها به علاوه برای حفظ جریان اسلامپ مجدداً ارزیابی شود. اگر درجه بندی سنگدانه های درشت تغییر یافته باشد طوری که یک میزان بالاتر از حال حاضر در الک های بزرگتر حفظ شود، ممکن است تنظیم نسبت مخلوط جهت کاهش میزان سنگدانه های درشت (از طریق متدولوژی نسبت بندی CBI) ضروری باشد.
دستیابی به اطلاعات حاصل از ویژگی های سخت شدگی و تازه
تفکیک علت یک نتیجه پیش بینی نشده از طریق ارزیابی ویژگی های معین تازه و سخت شده (به صورت توأم) ممکن است امکان پذیر باشد. برخلاف بتن معمولی، در SCC اطلاعات بیشتری در مورد ویژگی های رئولوژیکی مخلوط جمع آوری شده است. به ویژه روش های آزمون معین که یک برآورد منطقی ویسکوزیته مخلوط را ارائه می کند. ما می دانیم نسبت آب به پودر یک مخلوط (W/P)، یک متغیر اصلی تاثیر گذار
بر ویسکوزیته مخلوط است، درحالی که نسبت آب به سیمان (W/C)، عامل تعیین کننده اصلی مقاومت تراکمی است. با توجه به این مورد، می توانیم ار ارزیابی ویسکوزیته و مقاومت تراکمی جهت جداسازی نوسان آب در یک مخلوط استفاده کنیم.
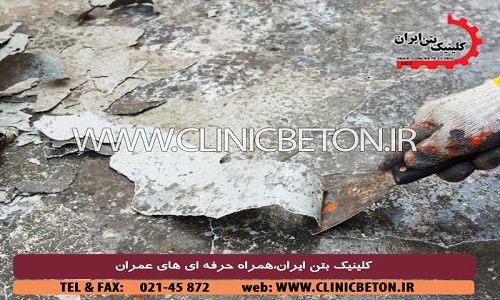
مطالعات موردی عیب یابی SCC
این بخش به معرفی 5 مطالعه موردی در جایی که SCC مورد استفاده قرار گرفته و نتایج پیش بینی نشده ای رخ داده می پردازد که نیازمند تحقیقات و دستورالعمل هایی برای اصلاح است.
مطالعه موردی 1
SCC برای استفاده در دیوارهای سازه ای با بتن ریزی درجا برای توسعه موزه هنری معین شد. یک تولید کننده معروف بتن آماده به تامین SCC برای این پروژه ها می پردازد. این تولید کننده قبلاً SCC را برای سایر پروژه های دیگر تامین می کرد، بنابراین از سابقه عملکری در حوزه مخلوط های SCC برخوردار است. در این پروژه، الزامات آزمون کنترل کیفیت اولیه صرفاً برای جریان اسلامپ بودند.
در یک بتن ریزی خاص، کارشناس تولید کننده SCC برای شروع بتن ریزی در دسترس نبود زمانی که وی وارد محل پروژه شد، 3 بار SCC بارگیری و انتقال یافته و از طریق پمپ بتن ریزی شده بود. هنگامی که پیمانه بعدی برای جریان اسلامپ مورد آزمون قرار گرفت، نماینده مشکلات موجود در مخلوط SCC را عنوان کرد. مخلوط، مرطوب به نظر می رسد و سریع تر جریان می یابد (همانند آب). نماینده با بچینگ بتن کارخانه تماس گرفت، میزان آب را کاهش و مقدار HRWR را افزایش داد. با این تغییر، عملکرد مخلوط نرمال شد. با این وجود 3 میکسر در دیوار بتن ریزی شده بود. در پایان بتن ریزی، زمانی که دیوار پر شد، پیمانکار باید چند اینچ خمیر آب دار از قسمت فوقانی دیوار بردارد، زیرا اولین پیمانه ها (که قبلاً بتن ریزی شده بودند)، تفکیک شده بودند. در گفتگوهای بعدی با پیمانکار، وی عنوان نمود که بتن حاصل از 3 بار اولیه در اطراف دیوارها سریع تر از بتن ریزی های اخیر جریان یافت. از طریق بازنگری سوابق بچینگ و مصاحبه با پرسنل کارخانه، عرضه کننده بتن مشخص کرد که محتویات سنگدانه درشت در طول بچینگ متعادل نشده بود. به واسطه عدم انجام تنظیمات ضروری، تقریباً 20 لیتر آب در هر متر مکعب بتن به صورت ناخواسته به مخلوط اضافه شده بود. با این وجود بخش سردرگم کننده فرآیند این بود که سطح جریان اسلامپ آزمایش شده در محل پروژه در سطح قابل توجهی تغییر نکرده بود.
پیمانکار و عرضه کننده تصمیم گرفتند که بتن ریزی را متوقف نمایند تا اینکه در نحوه ی عملکرد مخلوط بتن به هماهنگی برسند. این بدین معنی است که سرکارگرهای پیمانکار، پرسنل آزمایشگاهی و نمایندگان فنی با عرضه کنندگان بتن و مصالح افزودنی در خصوص مواردی که SCC قابل قبول را ارائه می دهد هماهنگ باشند.
برای تحقق این امر، جلسه و تمرین آموزشی در کارخانه تولید بتن برگزار شد. این نشست شامل بچینگ مخلوط طراحی شده اولیه، آزمون آن برای جریان اسلامپ، T50، VSI و حلقه J، افزایش آب در محتویات 10 لیتر در هر مترمکعب، آزمون مجدد و تکرار آن تا یک کل تجمعی 30 لیتر در هر مترمکعب می باشد.
این تمرین برای نشان دادن تایید آب اضافی به کارکنان پروژه می باشد، تعیین معیار SCC خوب و بد و در نهایت ایجاد یک مجموعه کامل از پارامترهای کنترل کیفی می باشد. جدول 13-1 نشان دهنده نتایج حاصل از این تمرین است. همانطور که به پیمانه آب اضافه می شود نتیجه در هر پارامتر تغییر می کند. باید توجه کرد که زمانی که به پیمانه آب اضافه می شود، جریان اسلامپ و زمان T50 افزایش می یابد، تغییرات ایجاد شده در مورد جریان اسلامپ و T50 مخلوط قابل پیش بینی است.
اما آزمایش VSI و حلقه J تا افزایش آب نهایی هیچ تغییری نشان نمی دهند. در طی مرحله تمرین، باید توجه کرد که نمونه موجود در فرغون، حاصل یک عمل آوری نهای با محتوای 30 لیتر آب اضافی است در حال تفکیک با سنگدانه هایی که در ته آن نشست کرده اند و دارای خمیر آبکی که در حال بالا آمدن بر روی سطح است. این آزمایش نشان می دهد که این نمونه درست شبیه 3 پیمانه اولیه است که به محل پروژه انتقال یافت و بتن ریزی شد، به خصوص با نگاه کردن به درون فرغون به این شباهت پی می بریم. این قضیه حتی زمانی که میزان VSI جریان اسلامپ لایه ای 1 باشد نیز اتفاق می افتد. جالب توجه است که آزمایش VSI اولیه نه تنها به تنهایی وابسته به آزمایش چشمی جریان اسلامپ لایه ای می باشد بلکه به ترکیب آزمایش چشمی بتن در میکسر و یا فرغون با جریان اسلامپ لایه ای نیز وابسته است. گاهی اوقات تفکیک در جریان اسلامپ لایه ای به علت عمق کم قابل مشاهده نیست (در فرغون).
اما در نمونه همین مخلوط، که دارای عمق بیشتری می باشد (در باکت، فرغون و غیره) می توان تفکیک را مشاهده کرد و همچنین فرصتی برای نشست ذرات جامد نیز به وجود خواهد آمد.
آخرین سوال بی پاسخ مربوط به میزان جریان اسلامپ قابل پذیرش در محل بتن ریزی است. زمانی که تمام آزمون های اولیه انجام شد و آزمون دوم جریان اسلامپ بر روی نمونه نهایی انجام شود تا تاثیر روش نمونه گیری را در ارزش آزمون تفکیک SCC نشان دهد. برای تمام آزمایش های جریان اسلامپ قبلی در این تمرین، یک نمونه (با حداقل مخلوط سازی مجدد) از فرغون برداشته شد. برای آخرین بار، متخصصین سعی کردند بتن را به صورت هدفمند مجدداً مخلوط سازی کنند و یک نمونه از مواد را از ته فرغون بردارند. نتیجه آزمایش جریان اسلامپ این نمونه 650 میلی متر بود (در حالیکه میزان جریان اسلامپ نمونه ای که مخلوط سازی اضافه نشده بود 735 میلی متر بود). این موضوع قابلیت تغییر پذیری آزمون ویژگی تازه را در زمانی که میزان تفکیک مخلوط بالا باشد مورد تاکید قرار می دهد. گرفتن نمونه مخلوط در این شرایط مشکل است. از این رو لازم است تا آزمایش های دیگری علاوه بر تست جریان اسلامپ انجام شود.
30 l/m3 | 20 l/m3 | 10 l/m3 | As-Batched | |
735 | 660 | 620 | 570 | Slump Flow (mm) |
0.7 | 0.9 | 1.9 | 2.3 | T50 (s) |
75 | 25 | 15 | 25 | J-Ring Difference (mm) |
1 | 0 | 0 | 0 | VSI |
جدول -1 پارامترهای SCC زمان افزودن آب به یک پیمانه واحد
راه حل نهایی/ پیشنهاد
مشاهدات کارگران بتن ریزی در مورد سرعت جریان SCC، تایید پرسنل نمونه گیری در مورد مشاهده تفکیک و نتیجه آزمون بچینگ همگی این موضوع را تایید می کنند که لازم است تولیید کننده در مورد میزان کنترل رطوبت دقت بیشتری به عمل آورد و این کاری است که تولید کننده باید انجام دهد که با انجام این فرآیند باقی تنظیمات عمل بتن ریزی با موفقیت انجام خواهد شد.
آموزه های عملی
قبل از شروع یک پروژه SCC، باید یک بررسی و تبادل نظر میان تولید کننده، پیمانکار و مسئولین آزمون انجام گیرد، یعنی جایی که همه طرف ها موافق انجام آزمایش و نیز شاخص SCC مناسب هستند.
- همواره از کنترل رطوبت سنگدانه ها در SCC اطمینان حاصل کنید.
- کسانی که تجربه ای در زمینه SCC ندارند باید تحت آموزش قرار گیرند، این آموزش ها شامل مشهده عملی SCC خوب یا بد می باشد.
- از بتن هایی که ظاهراً دچار مشکل هستند چشم پوشی نکنید، حتی اگر نتیجه صریح و دقیق باشد.
- مخلوط های تفکیک شده قابلیت تغییر پذیری بیشتری (در مقادیر) در مقایسه با مخلوط های پایدار، در آزمایش از خود نشان می دهند. بنابراین یک آزمون تنها، مانند آزمایش جریان اسامپ، به تنهایی جهت اطمینان از یک SCC خوب، کافی نیست. برای کنترل کیفیت همواره تست VSI و T50 همراه با آزمایش جریان اسلامپ انجام دهید. این آزمایش ها عملکرد خوبی را تضمین نمی کنند، اما چنانچه مشکلی در پیمانه ها وجود داشته باشد، احتمال مشخص شدن آنها توسط این نمونه ها (قبل از جایگیری) افزایش می یاد.
- روش نمونه گیری مشخص شده در ASTM C 172 بیان می کند که نمونه های تولید بتن که برای آزمایش گرفته می شود، باید با یک بیل، ترکیب و مخلوط سازی مجدد شود (جهت کسب حداقل اطمینان از یکنواختی).
متخصصین جهت مخلوط سازی مجدد نمونه ها، قبل از آزمون پر کردن قالب و تجهیزات، آموزش دیده اند. زمانی که یک مخلوط SCC ناپایدار باشد، موجب منحرف شدن نتیجه آزمایش می گردد. متخصصین باید آموزش ببینند تا ننمونه هایی از بتن داخل ظرف را بردارند و زمانی که مخلوط یکنواخت نیست درصدد یکنواخت کردن آن نباشند.
- تولید کننده باید همواره یک آزمون قدرتمندی را بر روی SCC مورد استفاده انجام دهید. این از طریق آزمایش که در جدول -1 ارائه شده انجام می پذیرد مخلوط را پیمانه و آن را آزمایش کنید، به آن آب اضافه کنید، بعد از هر افزایش، مجدداً اندازه گیری نمایید.
هر تغییر کیفی را که ملاحظه می کنید بهمراه نتایج آزمون ثبت کنید. این سوابق می تواند به عنوان دستورالعمل های کنترل کیفی در زمان اجرای پروژه مورد استفاده قرار گیرد.
مطالعه موردی 2
تولید کننده پیش ساخته، جهت قالب گیری کامل قطعات دیواری رنگ شده از بتن SCC استفاده می کند (توسط کامیون میکسر حمل شده و بتن ریزی می شود). قطعه ها به عنوان اجزاء سازه ای و همچنین به عنوان یک پرداخت معماری در ساختمان ها به کار گرفته می شوند.
قطعات در قالب های فولادی افقی بیرونی، در زیر نور خورشید مستقیم قرار دارند. قطعات متعدد در یک خط مستقیم قرار می گیرند و فرآیند بتن ریزی شامل پر کردن هر قطعه به صورت منظم (از یک پنل به پنل دیگر) می باشد. بعد از شکستن قالب رویه قطعات سند بلاست سطحی می شود تا به پرداخت مطلوب نهایی دست یابد.
بعد از فرآیند سندبلاست بود که تولید کننده به مشکلات توجه کرد. سندبلاست بیانگر نواحی تصادفی شامل خوشه های کوچ حفره (از 10 تا 20 میلی متر) است. ظاهر سطح به دلیل وجود این سطوح قابل قبول نبود. در تلاش برای حل این مشکل، تولید کننده زمان قابل توجهی در ایجاد تغییرات چندگانه در مخلوط SCC و مقدارهای مواد افزودنی صرف نمود، هیچ کدام از آنها موفقیت آمیز نبودند، مولف یک روز را برای مشاهده آماده سازی بچینگ و فرآیند بتن ریزی اختصاص داد. با این وجود هیچ موضوعی در فرآیند آماده سازی بچینگ مشاهده نمی شد، بخش های متعددی در طول فرآیند بتن ریزی مورد توجه قرار گرفتند.
قالب های فولادی در نوبت صبح آماده سازی شدند و بتن ریزی نزدیک ظهر شروع شد (در طول گرم ترین ساعات روز). قبل از جایگیری بتن در قالب ها، دمای سطحی روی قالب ها مورد بررسی قرار گرفت که تقریباً C°49 (F°120) بود. ه کامیون میکسر، حجمی از بتن را حمل می کند که بیش از یک قطعه را پر کند. زمانی که یک قطعه بتن ریزی شد، بقیه بتن در کامیون باقی می ماند تا اینکه فعالیت جایگیری در قطعه قبلی تکمیل گردد، سپس بتن ریزی در قطعه بعدی شروع می شود. با این وجود بتن نه تنها در کامیون بلکه در شوت نیز باقی می ماند. در این موقعیت یک قطعه کاملاً پر می شود و سطح شوت نیز بالا آمده و بالای قطعه خالی (که در نوبت بعدی بتن ریزی می شود) تاب می خورد. این فرآیند برای اجتناب از پخش شدن بتن بر روی زمین اطراف سطح بتن ریزی انجام شد. SCC از شوت بیرون زده و از یک ارتفاع بالاتر از 1 متر، بالای قالب می افتد. زمانی که بتن به داخل قالب ریخته می شود، در بعضی از پروژه ها بر روی سایر سطوح اطراف C°49 قالب فولاد، پمپاژ می شود. بتن بر روی قالب برای 5 تا 10 دقیقه می نشیند درحالی که قطعه دیوار قبلی تکمیل شده است. در این دوره زمانی، بتن کافی از شوت جاری می شود، درحالی که به اندازه قطر 1 متر با SCC پوشیده شده است. بتن به راحتی بر روی قالب فولادی قرار می گیرد و درجا شروع به سفت شدن می کند. نهایتاً در زمان شروع بتن ریزی این قطعه، بتن تازه بر روی قسمت فوقانی مواد سخت شده جاری می شود و هیچ تلاشی برای ترکیب مواد با هم صورت نمی گیرد، موقعیت این سطح بزرگتر بر روی قالب علامت گذاری می شود و روز بعد قطعه سند بلاست می شود و در این سطح، یعنی جایی که بتن در آنجا سقوط می کند، اجازه داده می شود که بر روی قالب داغ بنشیند، یک خط خمیده از حفره های کوچک نمایانگر می شود.
راه حل نهایی/ پیشنهاد
بتن ریزی قطعات دیواری نیازمند توجه بیشتر به جزئیات است. ظاهراً بخش های کوچک، زمانی می توانند آشکار شوند که سندبلاست یا سایر رویه های نهایی اجرا شده باشند. معمولاً توصیه می شود که تولید کننده اطمینان دهد هر قطعه بدون توقف بطور کامل بتن ریزی می شود، مخصوصاً در طول ماه های داغ تابستان، زمانی که قالب ها به دمای بالا برسند. ضمناً توصیه شد که بتن هرگز از ارتفاع بیشتر از 300 میلی متر به درون قالب رها نشود.
آموزه های عملی
- همیشه از دمای سطح قالب ها زمان بتن ریزی در بیرون آگاهی داشته باشید.
- رویه موقعیت یابی شوت بر روی قالب بعدی و عدم فراهم نمودن شرایط برای جاری شدن بتن بر روی سطح بتن ریزی یک رویه خوب و قابل قبول است. رویه های خوب و قابل قبول که به صورت منظم اجرا شوند می توانند گاهی موجب نتایج نامطلوب باشند.
- زمانی که یک نتیجه پیش بینی نشده یا نامطلوب رخ می دهد، تمام دلایل ممکن را به دقت بررسی کنید.
مطالعه موردی 3
یک تولید کننده ی مطرح و شناخته شده بتن پیش ساخته، از SCC جهت بتن ریزی شبکه های قطعه پیش تنیده شده استفاده می کند. شبکه ها تقریباً دارای 2 متر عمق با کابل های پیش تنیده متراکم که از قسمت تحتانی عبور می کنند، می باشد. شکل آنها یک شکل تیر معمولی I است. زمانی که بخش تحتانی حاوی کابل در داخل بخش شبکه ای بلند قرار می گیرد، بر روی یک شیب داخلی از پایین به بالا امتداد پیدا می کند.
بتن ریزی SCC از طریق جرثقیل و باکت انجام می شود و بتن ریزی های چندگانه برای پر کردن هر قالب شبکه ضروری می باشد. بتن بوسیه کامیون میکسر از کارخانه بتن انتقال می یابد. مشکل موجود برای تولید کننده عبارت است از تراکم هر خمیر ضعیف در امتداد سطح قسمت زاویه دار داخلی، ارزیابی این سطح نشان داد که سطح ظاهر شده حاوی سطوح بسیار بالای هوا بوده (تقریباً تا نقطه مشابه خمیر فوم دار). این غلظت فوم در هیچ کجای دیگر تیر، مشاهده نشده و دارای میزان منطقی پایداری بود. بخش حمل و نقل نگران این بود که علت موضوع وجود مشکلات دیگر در مخلوط یا در شبکه باشد که قابل مشاهده نیست. هسته ها از موقعیت های استراتژیک برداشته شده و هیچ مشکل مقاومت تراکمی یافت نشد. هر چند محتویات هوا نرمال بود، این موضوع به عنوان یک مشکل برای مخلوط بتن تلقی می گردید، از آنجایی که غلظت بالای هوا درون بتن وجود داشت، هیچگونه تنظیمات مخلوط یا مواد افزودنی ایجاد نشد، اما نتیجه منجر به حذف سطح خمیر سطحی گردید.
زمانی که مولف این موضوع را بررسی نمود، یکی از اولین سوالات مطرح شده این بود که آیا مخلوط موجود پایدار است؟ زمانی که بعضی از مخلوط های SCC بسیار ناپایدار باشند، کف تا سطح موجود بالا می آید. اگر یک مخلوط SCC ناپایدار درون این قالب های شبکه بتن ریزی شود، فوم ناپایدار بالا آمده و در برابر این سطح زاویه دار داخلی گیر می افتد. مطابق گزارش مدیر کنترل کیفی، هیچ نشانه ای مبنی بر تفکیک طول آزمون کنترل کیفی یا در طول بتن ریزی وجود نداشت. بنابراین، کل فرآیند بچینگ، انتقال، تست و بتن ریزی مورد تایید قرار گرفت و هیچ مشکلی مشاهده نشد تا اینکه جایگیری شد. قبل از بارگیری باکت با بتن از کامیون میکسر، یکی از کارگران بتن ریزی میزان بالایی از روغن قالب را در سراسر بخش های داخلی و بیرونی باکت سپری نمود. ترکیب شناخته شده نبود، این یک فرآیند معمول به کار رفته جهت کاهش ترکیب چند جزئی در باکت محسوب می گردید. با این وجود میدان اسپری شده بیش از حد بوده و مقادیر اضافی می توانست به صورت گل ورز داده متراکم در کنار لبه های تحتانی باکت مشاهده شود. هنگامی که مخلوط SCC (که هیچ علامت ناپایداری را نشان نمی داد) از کامیون به درون باکت ریخته شد، بتن و روغن قالب اضافی همزمان به حالت چرخشی در آمدند. زمانی که باکت پر شد، حجمی از فوم پایدار در کنار کل لبه باکت شکل گرفت. اندازه Band به میزان 75 در 75 میلی متر برآورد شد. این فوم شامل حباب های بزرگ ناپایداری که زمان تفکیک مخلوط SCC پدیدار می شود، نبود اما حباب ها کاملاً پایدار بوده و زمانی که باکت از بتن بیشتری پر می شد ناپدید نمی شدند. باکت بالا رفت و بتن در قالب ریخته شد. زمانی باکت برگشته و مجدداً پر می شود که کاملاً خالی شده باشد بدین معنی که هم بتن و هم فوم موجود در باکت در حال حاضر در قالب ریخته شده اند. این فرض مطرح بود که فوم تولید شده (زمان پر شدن باکت) احتمالاً در قالب با سطح بتن بالا می آید و در برابر سطح قالب فولادی زاویه دار داخلی گیر می افتد.
راه حل نهایی/ پیشنهاد
به کارگران جایگیری بتن توصیه شد که مقدار روغن قالب اسپری شده درون باکت خالی را کاهش دهند، بطوری که تولید فوم در کنار باکت کمتر شود. اگر این وضعیت تحقق نیابد، فومی که در امتداد بخش کنار باکت بالا می آید باید برداشته شود تا با بتن وارد قالب نشود.
آموزه های علمی
- فعالیت هایی که با بچینگ، مخلوط سازی، و تولید ارتباط ندارند می توانند به عنوان مشکلات مخلوط بتن محسوب گردند. در این مورد، وجود فوم نتیجه مشکل مخلوط بتن فرض شده بود اما در حقیقت چنین نبود.
- روغن اضافی قالب ممکن است منجر به تولید فوم و پایدار سازی آن گردد، چرا که همراه با بتن در طول بتن ریزی به اطراف پمپاژ می شود.
- باید از عملکرد روغن قالب مورد استفاده آگاهی داشت، کاملاً بدیهی است که این نوع پدیده مشابه، زمانی می تواند رخ دهد که روغن قالب اضافی در خود قالب وجود داشته باشد.
مطالعه موردی 4
یک مخلوط SCC بسیار سیال برای پر کردن فضای افقی باز و بزرگ در زیر زمین استفاده می شود. بتن از طریق باکت به محل بتن ریزی زیر زمین انتقال داده شده و از طریق لوله های افقی به دورترین نقطه گودبرداری شده افقی، پمپاژ می شوند. وقتی بتن جایگیری شد، لوله ها جمع می شوند و فضای افقی به آرامی با SCC پر می شود. (به خاطر اینکه فرآیند جایگیری آرام بوده و همچنین بتن ریزی حجیم بوده است). یک ترکیب از سیمان پرتلند تیپ 1 و سیمان سرباره در مخلوط SCC مورد استفاده قرار گرفت. میزان سیمان سرباره به اندازه 50% کل مواد سیمانی بود. پروژه با موفقیت طی و منجر به صرفه جویی در زمان و نیروی کار گردید، به علاوه روش های ایمن تر برای جایگیری را در اختیار پیمانکار قرار داد.
براساس موفقیت پروژه نخست، مهندس مربوطه، SCC را برای کاربرد در پروژه دوم، بیش از 1000 مایل (1600 کیلومتر) دورتر مورد استفاده قرار داد. نسبت های برابر با مخلوط پروزه نخست برای استفاده در پروژه دوم توصیه و تجویز شد. اما مخلوط با 50% خاکستر بادی نوع C نسبت بندی شد، زیرا این صرفاً پوزولان موجود محلی بود. این مخلوط SCC بسیار متفاوت تر از مخلوط اصلی (در پروژه اول) در این پروژه عمل کرد و در طول جایگیری به سرعت سفت شد، بطوری که پمپ بتن دچار انسداد شد و منجر به تاخیرهای مکرر و مشکلات جدی برای تمام افراد دخیل در پروژه گردید.
راه حل نهایی/ پیشنهاد
یک تست آزمایشگاهی برای بررسی واکنش پودرها و مواد افزودنی انجام شد. براساس این آزمایش، بدیهی بود که مقادیر خاکستر بادی نوع C باید کاهش یابد تا سفت شدن سریع را کاهش دهد. در این نقطه، تنظیماتی در نسبت های مخلوط ایجاد شد. یک مخلوط بازیابی شده آماده گردید و پروژه به صورت موفقیت آمیز استمرار یافت.
آموزه های عملی
- ترکیبات پودرهای متفاوت در ارتباط با ویژگی های جریان وابسته به زمان، رفتار بسیار متفاوتی خواهد داشت.
- انتقال یک مجموعه کامل از نسبت های یک مخلوط SCC از یک منطقه جغرافیایی به منطقه دیگر برای دستیابی به نتایج برابر، امکان پذیر نیست.
- SCC باید از طریق الزامات عملکردی تعیین شود نه از طریق نسبت های مخلوط.
مطالعه موردی 5
یک تولید کننده بتن پیش ساخته، سازه ای از SCC برای قطعات دیوار پیش ساخته با یک نمای اکسپوز بتن زبر استفاده کرد. بتن مخلوط شده به قالب بتن ریزی (از طریق یک باکت) انتقال داده شد. برای دستیابی به پرداخت مورد نیاز، حجم زیادی از سنگدانه ها الزامی بود. مصالح دانه درشت و مورد استفاده، دارای یک اندازه نسبتاً کوچک بودند، با بیش از 40% که در الک 75/4 میلی متر باقی ماندند. تولید کننده سه مشکل اصلی را تجربه کرد: دستیابی به سطح سیالیت مورد نظر جهت بتن ریزی مطلوب امکان پذیر نبود، مخلوط ناپایدار می شد، کاهش عملکرد تا حدی بود که بتن باید با ارتعاش از باکت بیرون می آمد.
مشکلات ایجاد شده و دلایل بالقوه آنها مورد بحث قرار گرفته و یک تحقیق آزمایشگاهی برای تفکیک دلایل و راه حل های پیشنهادی اجرا شد. جدول -2 به نمایش مشکلات و دلایل بالقوه می پردازد که ارزیابی شدند. زمان ارزیابی جریان اسلامپ مخلوط اصلی به کار رفته در تولید، غلظت بالای ذرات سنگدانه های درشت به خصوص در مرکز لایه ای جریان اصلامپ بلافاصله مشاهده شد. در فرآیند عیب یابی SCC، اگر این نوع جریان اسلامپ مشاهده شود، احتمالاً می توان این فرض را مطرح کرد که حجم خمیر برای ارتقاء جریان مناسب، کافی نبوده است. اگر HRWR اضافی به این مخلوط افزوده شود، احتمالاً افزایش کمی در این جریان اسلامپ خواهیم داشت. اما ممکن است خمیر شروع به جداشدگی از سنگدانه ها کند. این جداشدگی خمیر معمولاً در لبه بیرونی جریان اسلامپ لایه ای اتفاق می افتد.
یک تست آزمایشگاهی برای ارزیابی تنظیمات نسبت مخلوط و جایگزینی مواد خام انجام شد. زمانی که جمع خمیر مخلوط افزایش یافت (که نیازمند کاهش در حجم مصالح بود)، جریان اسلامپ به صورت قابل توجهی بهبود یافت (همان طور که در ثبات یا پایداری مخلوط دیدیم). در مورد جایگزینی مواد، سیمان مورد استفاده علت اصلی سفت شدن سریع بود. گرچه افزایش حجم خمیر نیز منجر به اصلاح نسبی در حفظ جریان اسلامپ گردید.
راه حل نهایی/ پیشنهاد
اعمال تغییرات در نسبت ها در این شرایط امکان پذیر نمی باشد، زیرا نمای اکسپوز بتن زبر (نمای شسته) تحت تاثیر قرار می گیرد.
مشکل | علل بالقوه |
عدم توانایی در دستیابی به سیالیت مطلوب | - برای سطح سنگدانه ای اکسپوز حجم بالایی از سنگدانه های درشت مورد نیاز است.
- سیمان گیرش آنی و یا کاذب موجب سفت شدن سریع بتن می شود.
|
ناپایداری مخلوط | - حجم بالای سنگدانه های درشت موجب حجم نامناسب خمیر شده که دچار مقدار زیاد HRWR می شود برای دستیابی به سیالیت مطلوب.
|
سفت شدن سریع | |
جدول -2 مطالعه موردی پنج مشکل و علل آن
بنابراین تولید کننده پیوسته از مخلوطی استفاده نمود که سفتی آن مشابه مخلوط SCC بوده و از ارتعاش سطحی برای مقاومت استفاده نمود. توصیه می شود برای بررسی مشکل سفت شدن سریع، تحقیقات بیشتری با عرضه کننده پودر انجام گیرد.
آموزه های عملی
- یک متغیر از قبیل حجم خمیر می تواند مشکلات متعددی چون جریان ناکافی، ناپایدار و افت جریان اسلامپ بوجود آورد.
- تعیین علت یک مشکل و سپس ارائه راه حل پیشنهادی همیشه امکان پذیر نمی باشد، مواد نمای اکسپوز بتن زبر (نمای شسته) از توانایی جایگیری راحت تر مخلوط اهمیت بیشتری دارد.
یک مخلوط SCC باید به صورت کامل آماده شود و قبل از اجرا ارزیابی گردد.
دستورالعمل های عیب یابی SCC
هیچ جدول واحدی نمی تواند ضمن استفاده از SCC به راحتی به ترسیم دلایل مربوط به تمام نتایج پیش بینی نشده بپردازد. در اکثر موقعیت های میدانی، غالباً این امکان وجود دارد که چندین عامل منجر به ایجاد یک مشکل شود یا این که مشکلات متعددی با هم و به صورت همزمان رخ دهند، بنابراین تنظیم یک متغیر بطور کامل مشکل را حل می کند.
جدول -3 به شفاف سازی بعضی از دلایل معمول می پردازد و باید به عنوان یک نقطه شروع برای تحقیقات عیب یابی مورد استفاده قرار گیرد.
مشکل | علت بالقوه | راه حل پیشنهادی |
اشکال نامنظم حباب سطحی یا فضای خالی بر روی سطحوح شکل دار | - تکنیک بتن ریزی احتمالاً مقدار زیادی فضای خالی محبوس کرده است. - میزان خمیر ناکافی است. - ویسکوزیته مخلوط ممکن است خیلی پایین باشد و امکان فرار هوای محبوس شده در طی بتن ریزی فراهم نشود. | - افزایش جریان اسلامپ - کاهش ارتفاع رهاسازی بتن - کاهش سرعت ریختن بتن جهت تطبیق با سرعت جریان بتن - کاهش ویسکوزیته مخلوط - تنظیم نسبت بندی سنگدانه ها جهت افزایش جریان - ایجاد ضربه و یا ویبره ملایم در طی بتن ریزی |
فضاهای خالی گرد متقارن بر روی سطوح شکل دار | - مخلوط ناپایدار - روغن قالب اضافی | - ایجاد اطمینان از پایداری مخلوط در زمان مخلوط سازی و نیز در تمام زمان ها - کاهش ضخامت روغن قالب |
لانه زنبوری | - جریان اسلامپ بسیار پایین - قابلیت عبور ناکافی به علت سنگدانه های نامناسب و یا حجم خمیر | - تنظیم نسبت بندی سنگدانه ها - افزایش جریان اسلامپ - افزایش میزان خمیر - تنظیم ویسکوزیته |
پر نشدن قالب ها به صورت کامل | - اگر این در زیر یک جعبه اتفاق بیافتد، پس علت آن انجام بتن ریزی از چندین جهت است. - جریان اسلامپ ناکافی | - افزایش جریان - تنظیم نسبت بندی سنگدانه ها - کاهش ویسکوزیته - کاهش سرعت بتن ریزی |
رگه ای شدن ماسه | - مخلوط ناپایدار است، وجود آب آزاد و یا سیال در قالب قبل از بتن ریزی - جریان اسلامپ ناکافی | - کاهش نسبت آب/ پودر - کاهش جریان اسلامپ - افزایش مقدار VMA - اطمینان از عدم وجود آب اضافی و یا سیال در قالب ها - چنانچه بتن پمپ شده، اطمینان از این که سر شیلنگ مستقیم به داخل قالب نرفته است. |
خطوط بتن ریزی | - تاخیر طولانی بین بتن ریزی های متوالی - حفظ جریان اسلامپ ناکافی (به علت مواد و یا تغییر دما) - مخلوط خاصیت تیکسوتروپیک دارد | - ارزیابی جهت خاصیت تیکسوتروپیک - افزایش نسبت آب/ پودر در صورت امکان - تاخیر زمان بندی شده بتن ریزی مناسب - افزایش مقدار افزودنی حفظ کارایی مخلوط - افزایش جریان اسلامپ |
انسداد تراکم | - طراحی ضعیف مخلوط | - تنظیم تناسب تراکم - افزایش میزان خمیر |
آبدهی زیاد | - جریان اسلامپ بسیار بالا - نسبت آب/ پودر بسیار بالا - VMA ناکافی | - کاهش جریان اسلامپ - کاهش نسبت آب/ پودر - افزایش مقدار VMA یا افزایش هوای وارد شده به مخلوط |
افت اسلامپ | - افزایش دمای محیط یا دمای بتن - رطوبت نامناسب که منجر به کاهش به نسبت آب/ پودر و جریان اسلامپ پایین تر می شود. - تغییر واکنش پذیری پودرها در زمان استفاده | - ایجاد رطوبت مناسب - افزایش مقدار افزودنی حفظ قابلیت کارایی - استفاده از HRWR افزایش اسلامپ - اندازه گیری واکنش پودر افزودنی ها |
جدول -3 دستورالعمل های عیب یابی SCC
قطعاً در طی هر فرآیندی نتایج پیش بینی نشده ای رخ خواهد داد و این نباید باعث شگفتی شود. یک تولید کننده یا مجری می تواند بری رو به رو شدن با این رویدادها با بکار بردن برنامه کنترل کیفیت، آمادگی لازم را کسب کند. این اطمینان وجود دارد داده هایی که می توانند در فرآیند عیب یابی مورد استفاده قرار گیرند به صورت منظم گردآوری شوند ممکن نیست علت یک نتیجه ی پیش بینی نشده بلاواسطه مشخص گردد و بعضی از دلایل ممکن است در فعالیت های مرتبط پنهان شود. بنابراین زمانی که مشکلی به وجود می آید، یک رویکرد سیستماتیک برای حل مشکل، توجه نمودن به کارآمدترین روش است. گرچه گرایش بیشتر به سمت یک آزمون واحد یا انجام فرآیند چندگانه یا ایجاد تغییر در مخلوط برای حل مشکل می باشد، اما اکثر اوقات این روش ها منجر به اتلاف وقت و فعالیت می شود. نهایتاً عیب یابی می تواند منتهی به شناخت بیشتر فرد از فرآیندها و مصالحی که در دسترس دارد گردد، به علاوه منجر به پیشرفت های جدید جهت کسب اطمینان از عدم وقوع مجدد خطاهای مشابه می گردد.
جهت اطلاعات بیشتر در زمینه تولید و فروش بتن و محصولات مرتبط و همچنین اطلاع از قیمت روز بتن می توانید با شرکت مهندسین مشاور مهرازان پایدار با نام نشان تجاری ثبت شده کلینیک بتن ایران با شماره 02145872 واحد مهندسی تماس حاصل نموده و یا جهت اطلاعات بیشتر در این زمینه به وب سایت رسمی شرکت WWW.CLINICBETON.IRمراجعه فرمایید.