اصول مکانیک شکست اغلب جهت توصیف اثر مسلح سازی الیاف، خصوصا در نسبت های حجمی پایین الیاف در frc فولادی معمولی، به کار گرفته می شوند. جزئیات مدلسازی خارج از هدف این مقاله می باشد، اما این موضوع توسط بنتور و میندس مورد بررسی قرار گرفته است.
به طور کلی، دو مفهوم در ارتباط با دوام frc مهم می باشد. اول آنکه در frc ترک خورده، الیاف بتن در عرض ترک ها قرار گرفته و به نزدیک هم قرار گرفتن آنها کمک می کنند. این حالت، از انتشار بیشتر ترک ها جلوگیری نموده (یعنی انرژی بیشتری برای رشد ترک ها نسبتب ه مصالح غیرمسلح نیاز می باشد) و در نتیجه طاقت ترکیب را افزایش می دهد. دوم آنکه به دلیل ضعیف تر بودن سطح مشترک الیاف- خمیر نسبت به خود خمیر (مشابه ناحیه انتقال در بتن معمولی) انتشار ترک ها در داخل خمیر در امتداد این سطح مشترک منحرف می گردد. بررسی ها و مطالعات هندسی نرخ آزاد شدن انرژی کرنشی برای جداشدگی در برابر ترک خوردگی معمولی بیانگر آن است که انتشر بیشتر، مستلزم انرژی ورودی بیشتری نسبت به خمیر غیر مسلح بوده و در نتیجه مجددا یک افزایش در طاقت پیش بینی می گردد.
زمان
شکل 9-4 کاهش مقاومت خمشی (به صورت کسری از مقاومت 28 روزه یعنی مقاومت اولیه پس از عمل آوری، در آغاز بهره برداری) برای انواع خمیر frc برپایه سیمان پرتلند (PC) را نشان می دهد که با الیاف شیشه نسل اول و دوم مقاوم در برابر قلیا (AR)، دو نوع از الیاف طبیعی، سیزال و الیاف نارگیل و الیاف پلی پروپیلن مسلح شده و در معرض محیط آزاد در انگلستان قرار گرفته اند.
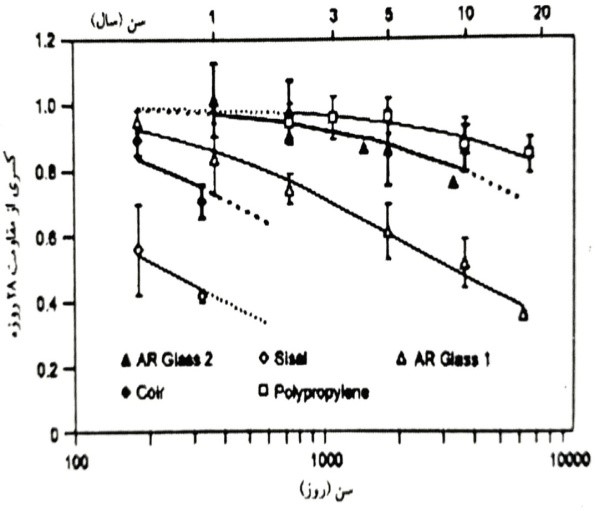
شکل 9-4- مقاومت در برابر زمان برای انواع بتن الیافی (frc) در معرض محیط طبیعی. کلیدواژه: AR Glass 2: شیشه AR نسل دوم/ بتن الیافی سیمان پرتلند معمولی؛ AR Glass I: شیشه AR نسل اول/ بتن الیافی سیمان پرتلند معمولی؛ پلی پروپیلن: بتن الیافی با پلی پروپیلن/ سیمان پرتلند معمولی/ پودر خاکستر بادی؛ بتن الیافی سیمان پرتلند معمولی، الیاف نارگیل و سیزال. منحنی ها: بهترین براش رابطه پورنل و همکاران و پورنل و بیدوز (S = [1+kt]-0.5). مقادیر خطا: ±1 انحراف معیار در صورت وجود.
هدف از الیاف در هر حالت، فراهم نمودن مسلح سازی اولیه بوده است. می توان دید که افت های مقاومتی قابل ملاحظه ای با زمان اتفاق می افتد، اما بزرگی این افت ها برای هر frc حتی در رده های مشابه، متفاوت می باشد (یعنی الیاف شیشه و الیاف بیعی). بنابراین انجام تعمیم ها در ارتباط با «دوام» سیستم های frc دشوار بوده و باید به دقت مورد ارزیابی قرار گیرد. به طور کلی، از شواهد موجود مشخص می گردد که دوام frc اولیه مرسوم، به صورت زیر می باشد:
الیاف طبیعی فرآوری نشده << شیشه AR نسل اول << شیشه AR نسل دوم < پلی پروپیلن اگرچه مقاومت خصوصیتی است که برای سالخوردگی بسیار زیاد ذکر می شود، اما دیگر خصوصیات اغلب بیشتر مورد توجه می باشند. با کاهش اثر یا کارآیی الیاف، بر اثر هر مکانیزمی، مقاومت ترکیب کاهش می یابد تا جایی که الیاف دیگر هیچگونه سهم مقاومتی نخواهند داشت، اما مقاومت خمیر حفظ خواهد شد، زیرا مقاومت آن با زمان ثابت بوده و یا افزایش می یابد. بنابراین مقاومت در frc اولیه تنها تا زمانی کاهش می یابد که برابر با مقاومت خمیر شود که در این نقطه کم و بیش ثابت می ماند؛ در frc اولیه، مقاومت خمیر عموما در حدود 20% تا 50% مقاومت ترکیب اولیه بوده، اما در frc ثانویه، که مقدار الیاف نزدیک و یا پایین تر از نسبت حجمی بحرانی است و هدف از الیاف اساسا ایجاد طاقت پس از نقطه حداکثر است (مانند شکل 9-2b)، مقاومت اولیه ترکیب عملا مانند مقاومت خمیر می باشد. در اینگونه موارد، بهتر است یک شاخص طاقت (که معمولا از مساحت زیر منحنی تنش- کرنش تا یک کرنش مشخص به دست می آید) و یا کرنش گسیختگی کنترل شود. از آنجا که هر دو این خصوصیات ماتریس در مقایسه با ترکیب اولیه ناچیز می باشند، این خصوصیات به طور موثری تا صفر کاهش می یابند. با این وجود، اندازه گیری این خصوصیات نسبت به مقاومت دشوارتر بوده و اغلب پراکندگی بسیار زیدی را نشان داده و در نتیجه مقاومت بهترین پارامتر خواهد بود. مثلا لیاف طبیعی فرآوری شده مانند frc سلولزی، معمولا تولید می شود که نسبت حجمی الیاف کمتر یا تقریبا برابر Vfcrit بوده و در نتیجه برای کنترل مقاومت به عنوان یک کمیت نزولی مناسب نخواهد بود. در واقع، مقاومت طی 5 سال قرارگیری در معرض محیط بیرونی، بر اثر ادامه هیدراسیون خمیر و افزایش پیوستگی (و در نتیجه افزایش 1C و ضرایب کارآیی الیاف)، تا نصف افزایش می یابد. اما کرنش گسیختگی از حدود 3% تا مقدار متناظر آن برای خمیر (یعنی 1/0%) در طی این مدت کاهش می یابد که نشانگر آن است که مزیت ناشی از مسلح سازی الیاف تا حد زیادی پس از این زمان، حتی با وجود افزایش مقاومت، کاهش یافته است.
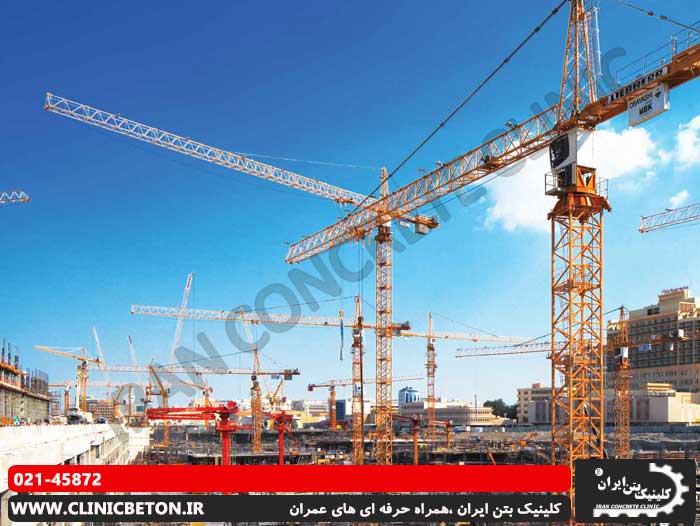
بتن های الیافی
پلیمرهایی به غیر از پلی پروپیلن نیز برای مسلح سازی بتن استفاده شده اند. اکثر آنها نه دارای پیوستگی مناسب با سیمان بوده و نه به اندازه کافی سخت/محکم هستند تا بتوانند نقش قابل توجهی داشته باشند و در نتیجه هیچگونه داده فرسایشی و هوازدگی برای آنها وجود ندارد. آکرز و همکاران سالخوردگی frc شامل PVA را تا 7 سال مورد بررسی قرار دادند. هیچگونه افت مقاومتی گزارش نشد اما معلوم نیست آیا نسبت حجمی بحرانی الیاف به میزان قابل ملاحظه ای بیشتر از Vfcrit بوده است، و در نتیجه این یک نتیجه قطعی و نهایی نمی باشد. ماجومدار گزارش نمود که مقاومت در frc ش��مل PVA پس از 5 سال هوازدگی حفظ شده است، اما دوباره نسبت حجمی الیاف بسیار پایین بوده است، چنانکه از تفاوت بسیار کم میان مقاومت اولین ترک و مقاومت نهایی این موضوع قابل تشخیص می باشد. frc آرامید هیچگونه افتی را در خصوصیات پس از دو سال هوازدگی نشان نداده است، اما اخیرا مفسرین نگرانی هایی را در ارتباط با سازگاری بلندمدت تر الیاف آرامید با سیمان، بیان داشته اند. الیاف پلی استر برای مسلح سازی بتن مناسب نمی باشند، زیرا این الیاف در سیمان به سرعت تخریب می شوند.
الیاف کربن عموما نسبت به محیط قلیایی خورنده در ترکیبات سیمانی، تاثیرناپذیر فرض شده و در نتیجه نسبت به مکانیزم های تخریبی مربوطه نیز ایمن فرض می شوند. محققین اخیر نیز با این فرض موافق می بااشند، هرچند که داده های هوازدگی بلند مدت کمی در مراجع موجود می باشد. کاتز و بنتور و کاتز دریافته اند که مقاومت و طاقت frc کربن در حدود 30 روز به یک مقدار بهینه می رسد که پس از آن افت جزئی در خصوصیات ممکن است بر اثر تراکم خمیر مشاهده گردد، که این خصوصیات احتمالا پس از این مرحله ثابت می مانند. بزرگی این تاثیر به فرمول خمیر، یعنی نسبت میکروسیلیس افزوده شده بستگی دارد .(مقالات دیگر وب سایت کلینیک بتن ایران را مشاهده فرمایید.)
پربازدیدترین مطالب ما را از دست ندهید!
دوام frc فولادی کمتر مورد توجه قرار گرفته است و لازم است که با نگاهی متفاوت مورد بررسی قرار گیرد که در آن، frc فولادی با بتن مسلح (RC) معمولی مقایسه می گردد، یعنی مطالعات در زمینه مشاهده یا عدم مشاهده پوسته شدن سطحی و هرگونه تغییر در یکپارچگی سازه ای بجای کاهش خصوصیات مصالح، گزارش می شوند. بنتور و میندس و جانستون، مطالعات دوام frc فولادی را تا حدود اواخر قرن خلاصه نموده اند. حتی تحت شرایط خوردگی تسریع شده در مدت چند ماه مانند چرخه های تر و خشک شدن در محلول های نمک داغ، frc فولادی با %2= Vf می تواند حداقل 70% مقاومت و 40% طاقت خود را حفظ نماید. گرانجو و بلوچ نشان داده اند که خوردگی الیاف با افت طاقت یا مقاومت خمشی پس از یک سال در یک محیط دریایی شبیه سازی شده حتی برای نمونه های از پیش ترک خورده، مرتبط نمی باشد. تحت شرایط عادی، به نظر می رسد که هیچگونه تخریبی به جز خوردگی ظاهری در سطح الیاف گزارش نشده است. در یک بازنگری، هاف به این نتیجه می رسد که frc فولادی حتی در محیط های دریایی، تنها در صورت ترک خوردن، تخریب خواهد شد.