اصلاح بتن و ملات در حضور یک لاتکس هم زمان با هیدراتاسیون سیمان و تشکیل یک لایه پلیمر (به هم پیوستگی ذرات پلیمر و پلیمرسازی مونومرها) اتفاق می افتد. هیدراتاسیون سیمان عموما بر فرآیند پلیمرسازی پیشی گرفته و همان طور که عمل آوری در حال انجام است، یک فاز ماتریسی متشکل از هیدرات های سیمان و لایه های پلیمر تشکیل می گردد (شکل 15-6). منافع اصلاح با لاتکس، متشکل از هیدراتهای سیمانو لایه های پلیمر تشکیل می گردد (شکل 15-6). منافع اصلاح با لاتکس را زمانی می توان بهتر متوجه شد که هیدراتاسیون سیمانو تشکیل لایه پلیمر انجمام می شود تا به یک شبکه ماتریسی یکپارچه دست بیابیم که فاز سیمان هیدرات شده و فاز پلیمر به هم نفوذ کنند. خصوصیات برتر و ملات و بتن اصلاح شده با پلیمر در قیاس با بتن و ملات سنتی با چنین ساختار مجزایی تعریف می شود. مثلا، پیوند بهتر میان سنگدانه ها و هیدرات های سیمان که با چند پلیمر واکنش دهنده همچون استرهای پلی اکریلیک (PAE) به دلیل واکنش آنها با کلسیم هیدروکسید رخ می دهد با سطوح سیلیکاتی مقاومت های خمشی را افزایش می دهند؛ و لایه های پلیمر که ایجاد یک اثر محکم کننده حول سنگدانه ها و هیدرات های سیمان دارند که می توانند ترک ها را به هم وصل کنند و از پیش روی ترک جلوگیری کنند، خصوصیات ضد آبی و ناتراوایی، و مقاومت شیمیایی ذوب انجماد را افزایش دهند.
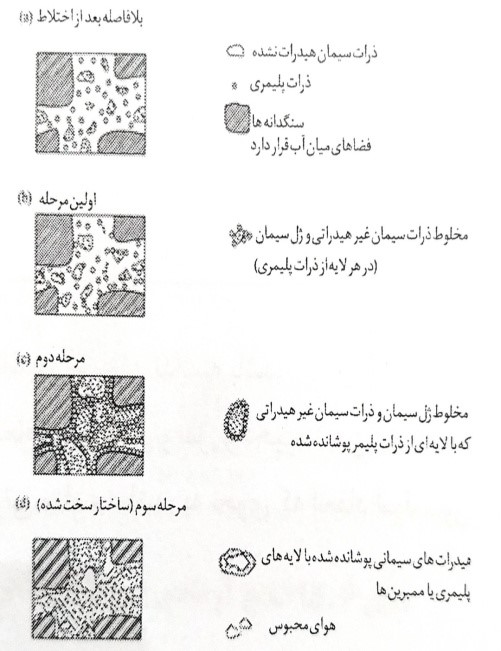
شکل 6-14 مدل ساده سازی شده از تشکیل ماتریس سیمان- پلیمر
الف- (بتن سخت شده)
چنین تاثیراتی با افزایش در میزان پلیمر موجود یا نسبت پلیمر به سیمان (نسبت ذرات جامد کل در یک لاتکس پلیمر به مقدار سیمان در یک مخلوط بتن یا ملات اصلاح شده با لاتکس) بالا می رود. با این وجود، در سطوح فراتر از %20 وزن سیمان در مخلوط، هوای محبوس اضافی و ناپیوستگی در ساختار شبکه یکپارچه تشکیل شده که منجر به کاهش در مقاومت فشاری و مدول می شوند.
نسبت اختلاط
اگر چه طرح اختلاط بتن و ملات اصلاح شده با لاتکس بیشتر به همان روش ملات و بتن معمولی انجام می گیرد. خصوصیاتی همچون کارایی، مقاومت، قابلیت امتداد، به هم چسبیدگی، ناتراوایی و مقاومت شیمیایی به جای آنکه با نسبت آب به سیمان کنترل گردد، با نسبت پلیمر به سیمان کنترل می شوند. از این رو، نسبت پلیمر به سیمان بید بر مبنای الزامات مطلوب باشد.
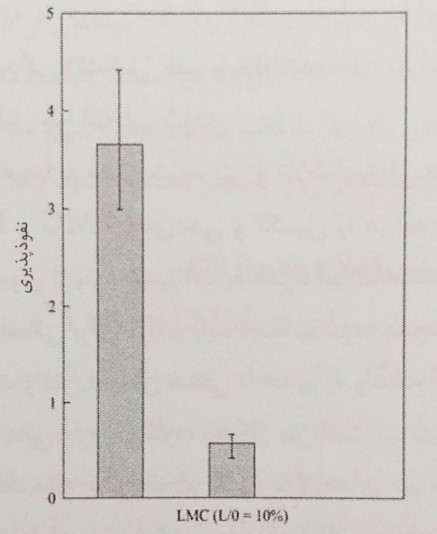
شکل 6-15 نتایج آزمایش نفوذپذیری کلریدی
نسبت های اختلاط اغلب ملات های اصلاح شده با لاتکس در بازه نسبت سیمان به ریزدانه 1:2 تا 1:3 (وزنی)، نسبت پلیمر به سیمان %20-5 و نسبت آب به سیمان 0.6- 0.3 بسته به کارایی مورد نیاز آنها قرار می گیرد. به دلیل خصوصیات محبوس کنندگی هوای ذاتی لاتکس ها، عوامل هوازا نمی توانند در ملات و بتن اصلاح شده با لاتکس استفاده شوند. در زمستان و در اقلیم های سرد، کاربرد سیمان با مقاومت اولیه بالا، سیمان سخت شونده فوق سریع و سیمان با آلومین بالا باید مورد ملاحظه واقع شود. آیین نامه ACI (انستیتو بتن آمریکا) دستورالعمل هایی برای نسبت های اختلاط بتن های اصلاح شده با لاتکس پیشنهاد کرده و این دستورالعمل ها منبع سودمندی برای کاربری در عرشه پل و وصله زدگی می باشد.
اختلاط، جای دهی و عمل آوری
تجهیزات اختلاط سنتی، وسایل تکمیلی و مخازن بتن آماده می تواند برای اختلاط و جای دهی ملات اصلاح شده با لاتکس (LMM) و بتن اصلاح شده با لاتکس (LMC) استفاده شود. پیش از تخلیه سیمانو سنگدانه به درون میکسر، لاتکس به آب مخلوط اضافه می گردد. علیرغم کاربرد عامل های ضد کف شدگی (تشکیل کف یا Foaming)، سرعت و دوره اختلاط باید برای اجتناب از وارد شدن بی دلیل هوا انتخاب شود.
پربازدیدترین مطالب ما را دنبال کنید!
اگر چه LMM و LMC تقریبا به همان شیوه بتن و ملات معمولی جای دهی و تمکیل می شوند. زمان کار کوتاه تر LMM و LMC جای دهی و تکمیل را در مدت 1 ساعت پس از اختلاط الزامی می کند. برای جلوگیری از وارد شدن آب به همراه آب انداختگی پلیمرها در سطوح تمکیل شده می بایستی از لرزش اضافی برای تراکم باید اجتناب شود. همچنین در سطوح LMC اتمام ماله کشی در قیاس با ملات و بتن سیمان سنتی تا حدی به واسطه کشش مرطوب و شکل گیری یک پوسته سطح که به آسانی پاره می شود، مشکل می باشد. در نتیجه ماله کشی اضافی توصیه نمی شود. چندین مرتبه باید ماله کشی انجام بگیرد تا لایه های کم ضخامت شکل گرفته در طی ماله کشی برطرف شود. به دلیل پاره شدگی سطح که اتفاق خواهد افتاد، ماله کشی مجدد پس از گیرش اولیه توصیه نمی شود. از آنجا که لاتکس ها برای انعقاد در دماهای پایین و بالا مستعد هستند، LMC و LMM نباید هیچگاه در دماهای پایین تر از 5°C و بالاتر از 30°C جای دهی شود. به منظور ممانعت از آب انداختگی ذرات جامد به روی سطوح تمام شده به دلیل لرزش اضافی یا خیس شدگی توسط آب پاشیده شده بلافاصله پس از جای دهی، باید توجه کافی نمود. سطح ها باید پس از اتمام عملیات با یک کرباس یا صفحات پلی اتیلن پوشش داده شود. پیش از جای دهی LMM و LMC همه آلاینده های سطح و مواد شل باید برطرف گردد، سطوح باید به دقت خیس شود و همه آب های ایستا از روی آن برداشته شود.
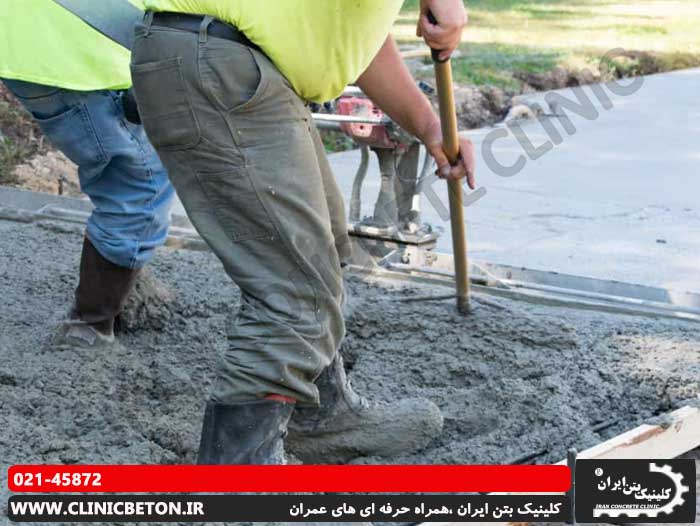
روان کننده بتن تولیدی
شرایط مل آوری خیس همچون نفوذ آب یا عمل آوری مرطوب قابل اعمال به بتن و ملات با سیمان معمولی به ملات و بتن اصلاح شده با لاتکس آسیب زننده است. مقاومت های بهینه با فراهم آوردن یک حد معقول از شرایط خیس (برای 1 تا 3 روز) برای هیدراتاسیون سیمان اولیه و شرایط خشک بعدی (در دمای محیطی) به منظور ارتقاء به هم پیوستگی ذرات پلیمری برای تشکیل لایه، حاصل می گردد. تاثیرات این شرایط عمل آوری روی مقاومت LMM و LMC در جدول 13-6 نشان داده می شود.
عموما، لاتکس های پلیمر مورد استفاده به عنوان اصلاح کننده های سیمانی سمی نیستند. آنها موادی هستند که به لحاظ کارایی امنیت داشته و هیچ پیشگیری خاصی لازم نیست انجام گیرد. با این وجود، چون آنها چسبندگی فوق العاده اای به مواد گوناگون از جمله به فلزات دارند، همه تجهیزات و وسایل همچون میکسرها، ماله کش ها، لرزاننده ها باید بلافاصله پس از کاربرد با آب تمیز شسته شود. برای بتن هایی که نیاز به قالب دارند، توصیه می شود که از موثرترین عامل های جداسازی از قالب همچون موم سیلیکونی یا گیریس استفاده شود.