کُندگیر کننده ها
بتن تازه ای که به خوبی طراحی و ساخته شده باشد، یک خمیر روان و کارپذیر است که با حفظ قوام (درون چسبی) خود به آسانی جابجا، پخش، متراکم و پرداخت می شود بدون آنکه جداشدگی در آن رخ دهد. با گذشت زمان، بتن تازه به تدریج کارآیی خود را از دست می دهد و به خمیری سفت و پس از آن به جسمی نیمه جامد و در آخر به ماده ای جامد تبدیل می شود. این سفت شدگی و دگرسانی از خمیری روان به ماده ای جامد که با کاهش کارپذیری همراه است به دلیل پیشرفت فرآیند آبگیری سیمان رخ می دهد و به نام پدیده "گیرش بتن" شناخته می شود. پس از گیرش و همراه با پیشرفت آبگیری سیمان، به تدریج بتن سخت و به ماده ای صلب تبدیل می شود که قابلیت تحمل بارهای وارده را دارد. این پدیده به نام سخت شدگی بتن شناخته می شود.
ایجاد تاخیر در گیرش بتن در بسیاری موارد مانند بتن ریزی در هوای گرم و مناطق گرمسیری، حمل و نقل های طولانی، کسب زمان لازم برای ریختن و پرداخت کردن بتن، هماهنگی با سرعت حرکت قالب لغزنده، کنترل دمای آبگیری به خصوص در بتن های حجیم یا بروز وقفه در عملیات بتن ریزی ضروری است که می تواند با استفاده از افزودنی های کندگیر کننده امکان پذیر شود. استفاده از کندگیر کننده ممکن است بر طراحی یا روند بتن ریزی تاثیر گذارد. برای نمونه با کنترل و کند کردن روند آزاد شدن گرمای آبگیری سیمان می توان مقاطع بزرگتری را طراحی و اجرا نمود، یا نماهای تزیینی با استفاده از سنگدانه های نمایان به وجود آورد.
از آنجا که فرآیند آبگیری سیمان یک فرآیند شیمیایی و در بردارنده شماری از واکنش های شیمیایی است، انتظار می رود که با افزودن برخی از مواد شیمیایی به مخلوط سیمان پرتلند و آب بتوان بر آهنگ آبگیری سیمان تاثیر گذاشت و گیرش یا سخت شدن خمیر سیمان را دستخوش تغییر کرد.
فرآیند آبگیری سیمان
آبگیری سیمان پرتلند، که به واکنش شیمیایی بین سیمان و آب گفته می شود، زنجیره ای از واکنش های شیمیایی همپوشان و پیاپی بین بخشینه های (پدیدآرنده های) کلینر، کلسیم سولفات، آب و همچنین بین محصولات آبگیری است که به گیرش و سخت شدن خمیر سیمان می انجامد. افزون بر این، آبگیری سیمان در برگیرنده مجموعه ای از فرآیندهای شیمیایی همبسته (همبند یا وابسته) است که آهنگ (نرخ) رخدادن هر یک از آنها به ماهیت خود فرآیند و به وضعیت و حالت سیستم در زمان رخداد فرآیند بستگی دارد.
از دیدگاه مبانی ترمودینامیکی، اکنون پذیرفته شده و آشکار است که آبگیری سیمان یک فرآیند حل شدن و رسوب کردن است. با در نظر گرفتن ساختار بلورین و نیمه بلورین ساختگرهای (فازهای) هیدراته نشده و هیدراته شده سیمان، آشکار می شود که تبدیل و دگرسانی ساختگرهای هیدراته نشده به هیدراته شده امکان پذیر (شدنی) نیست مگر آنکه امکان عبور و گذر یون ها از درون محلول فراهم باشد.
حل شدن آمیزه های سیمان
واکنش های اولیه آمیزه های (ترکیبات) سیمان پرتلند با آب درون محلول رخ می دهند یا درون محلولی اند یعنی آمیزه ها (ترکیبات) در ابتدا یونیزه می شوند و سپس محصولات آبگیری در محلول شکل می گیرند. حل شدن ساختگرها و سازنده های هیدراته نشده به معنی تجزیه بلورها است و پیامد تجزیه بلورها آن است که یون ها و ذرات با بارهای الکتریکی مثبت و منفی همزمان با هم و به یک اندازه وارد محیط واکنش می شوند. وجود همزمان یون ها و ذرات واکنشگر مختلف در محیط به اندر کنش بین آنها می انجامد. این اندر کنش می تواند به واکنش بین ذرات مختلفی بیانجامد که از بلورهای متفاوت جدا شده اند یا بر سرعت تجزیه و حل شدن ذرات دیگر اثر بگذارد یا آهنگ و روند واکنش بین ذرات را کُند یا تند کند. از سوی دیگر، واکنش برخی از ذرات و رسوب کردن محصولات واکنش بر سطح ذرات سبب کاهش غلظت می شود و بر سرعت تجزیه ذرات دیگر تاثیر می گذارد.
شکل گیری و رسوب کردن محصولات آبگیری
همزمان با حل شدن و تجزیه آمیزه های سیمان در محلول آبی بی درنگ یون های سیلیکات، آلومینات، سولفات و کلسیم در مقادیر زیاد به همراه مقادیر کمتری از یون های عناصر دیگر (مانند سیدیم، پتاسیم، آهن، منیزیم و ...) به محیط واکنش سیمان با آب وارد می شوند. اندرکنش بین این یون ها به واکنش شیمیایی بین آنها و شکل گیری آمیزه های شیمیایی جدید می انجامد. بیشتر آمیزه ها و محصولات آبگیری که در زمان های اولیه پس از اختلاط آب و سیمان پدید می آیند از نوع کلسیم آلومینات هیدراته (اترینگایت، مونوسولفات، هیدروگارنت)، کلسیم سیلیکات هیدراته (C-S-H) و کلسیم هیدروکسید (CH) است.
در ابتدا و پس از اختلاط سیمان و آب، سرعت تجزیه آمیزه ها و سازنده های سیمان (به ویژه C3S و C3A) بسیار زیاد است و پدیده حاکم در مراحل اولیه از نوع حل شدن است. با افزایش غلظت و انباشته شدن محیط از یون ها به تدریج سرعت تجزیه سیمان کاهش می یابد. با افزایش غلظت یون ها در محیط واکنش سیمان و آب آمیزه های شیمیایی جدید یا همان محصولات آبگیری به شکل هسته هایی در فضای بین دانه های سیمان پراکنده می شوند یا به شکل جوانه هایی بر نقاط واکنش پذیر سطح دانه های سیمان نمایان می شوند. به بیان دیگر، شکل گیری محصولات آبگیری با پدیده و سازوکار جوانه زدن آغاز می شود. این جوانه ها به مانند نطفه هایی برای رشد و گسترش محصولات آبگیری عمل می کنند. محصولات آبگیری به این جوانه ها می چسبند و سبب رشد و گسترش آنها می شوند. این پدیده و سازوکار که به نام رویش (رشد کردن) شناخته می شود در ادامه فرآیند آبگیری سیمان نقش دارد.
با پیشرفت روند جوانه زدن، به تدریج نقاط واکنش پذیر سطوح دانه های سیمان کاهش می یابد و روند واکنش آبگیری کند می شود و یک دوره آرامش یا سکون در واکنش رخ می دهد. شکل گیری جوانه ها و رشد آنها سبب تهی شدن محیط واکنش از یون ها می شود و این موضوع سرعت جزیه سیمان را شتاب می دهد. با ادامه واکنش های آبگیری، محصولات آبگیری در دنباله جوانه های موجود شکل می گیرند و جوانه ها رشد می کنند. با رشد جوانه ها سطح واکنش پذیر در محیط افزایش می یابد و یون های جدیدی که تجزیه و وارد محیط شده اند با شتاب واکنش می کنند.
بخشی از محصولات آبگیری نیز که در فضای خالی دانه های سیمان جوانه زده و رشد کرده اند بر سطح دانه ها یا جوانه های رشد کرده رسوب می کنند. این دوره از واکنش دوره شتابنده است که در دنبال دوره سکون نمایان می شود. اگرچه افزایش سطح جانبی جوانه ها ناشی از رشد آنها سبب افزایش آهنگ (سرعت) واکنش می شود ولی از سوی دیگر، سرانجام (در نهایت) در هم تنیدگی (در هم پیچیدن) محصولات فزاینده حاصل از ادامه واکنش آبگیری می تواند به کاهش سرعت واکنش بیانجامد. تا زمانی که یون ها در محیط بتوانند به راحتی و آزادانه حرکت کنند مکانیزم اصلی آبگیری همان مکانیزم جوانه زدن و رویش است. با محدود شدن حرکت آزادانه یون ها در محیط، مکانیزم حاکم بر فرآیند آبگیری به انتشار تغییر می کند. واکنش شیمیایی در این مرحله بیشتر از نوع "شیمی درجا" یا واکنش حالت جامد است که در سطح دانه ها انجام می شود بدون آنکه نیازی به تجزیه و وارد شدن مواد و یون ها به درون محلول باشد.
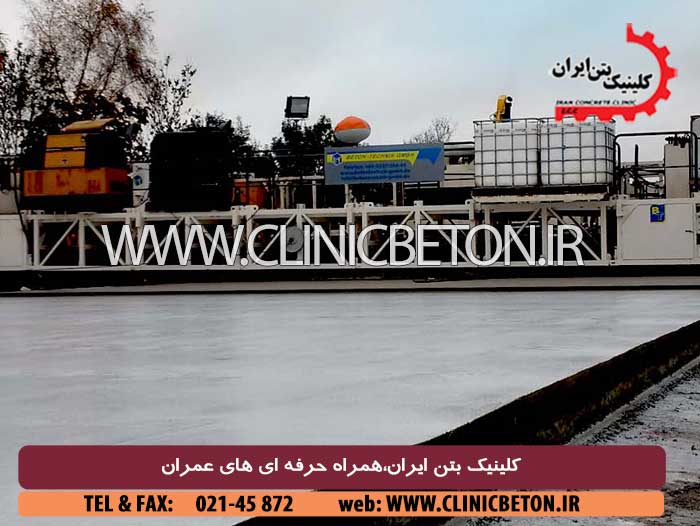
سینتیک آبگیری سیمان
از آنجا که واکنش های شیمایی آبگیری سیمان بسیار پیچیده هستند معمولاً به جای بررسی مستقیم آنها سینتیک شیمیایی آبگیری را بررسی می کنند. سینتیک شیمیایی بررسی و مطالعه سرعت (یا آهنگ) واکنش های شیمایی است. از نظر علمی، سینتیک شیمیایی راجع به عواملی است که بر سرعت واکنش های شیمیایی اثر می گذارند و اینکه چگونه می توان سرعت واکنش ها را کنترل کرد. یکی از روش ها و ابزارهایی که برای مشاهده غیرمستقیم آبگیری سیمان و ترکیب سازهای آن و همچنین بررسی مکانیزم های سینتیک واکنش آبگیری به کار می رود گرماسنجی تک دما است.
در شکل زیر نمایی کلی از روند آزادسازی گرما (گرمازایی) به روش گرماسنجی تک دما نسبت به زمان در مراحل مختلف واکنش آبگیری سیمان پرتلند و روند تقریبی شکل گیری هیدرات ها (محصولات آبگیری) نشان داده شده است.

نمایی کلی از نمودار گرماسنجی تک دما در فرآیند آبگیری سیمان و شکل گیری هیدرات ها
سفت شدگی و گیرش خمیر سیمان
یکی از اولین پیامدهای فیزیکی ناشی از فرآیند شیمیایی بین سیمان و آب (یا همان آبگیری سیمان)، تغییر حالت و دگرسانی بتن خمیری کارپذیر (بتن تازه) به ماده ای شکننده و صلب (بتن سخت شده) است. این فرآیند در برگیرنده دو بخش سفت شدگی و جامد شدگی است.
سفت شدگی آن بخش از دگرسانی خمیر روان به جسم جامد است که به کاهش کارپذیری یا کارآیی بتن می پردازد. کارپذیری یک ویژگی بتن یا ملات تازه و همگن است که بیانگر میزان سادگی (یا دشواری) در هم آمیختن، ریختن، متراکم کردن و پرداخت کردن بتن یا ملات است به گونه ای که همگنی آن حفظ شود.
کار پذیری به رفتار رئولوژیک بتن بستگی دارد که خود به ویژگی های رئولوژیک خمیر سیمان و به اصطکاک داخلی بین سنگدانه ها وابسته است. رفتار دولوژیک بتن تازه با "منحنی جریان" دو نقطه ای و با مدل خطی بینگهام بیان می شود.
T=T0 + µ × y,
برای آنکه درک روشنی از مدل خطی بینگهام به دست آید فرض می کنیم که بتن تازه آمیخته ای از ذرات و دانه های معلق در آب باشد. در این فرض تمامی سنگدانه ها، سیمان، پوزولان و پرکننده ها در شمار ساختگر (فاز) جامد جای می گیرند و از حباب های هوا هم صرفنظر می شود.
حداقل مقدار آب در چنین انباشته ی توده شده ای متناظر با فضای خالی بین دانه ها است. چنین انباشته ای از دانه های جامد که تمامی فضاهای خالی آن با آب پر شده اند بتنی با کارپذیری بسیار کم خواهد بود.
با افزایش مقدار آب فاصله بین دانه ها بیشتر می شود و امکان لغزش دانه ها بر یکدیگر و حرکت بین آنها فراهم می شود در چنین حالتی اگر تنش برشی به سیستم وارد شود امکان پدید آمدن تغییر شکل در آن وجود دارد به شرط آنکه تنش وارده با اندازه کافی بزرگ باشد که بتواند بر اصطکاک بین دانه ها چیره شود.
این تنش آستانه ای که به نام تنش جاری شدن نیز شناخته و با T0 نشان داده می شود به تعداد و ماهیت نقاط تماس بین دانه ها بستگی دارد و به ساختگر (فاز) مایع بستگی ندارد. تنها نقش آب به عنوان ساختگر (فاز) مایع در چنین حالتی ایجاد فاصله بین دانه ها است.
مقدار تنش جاری شدن (T0) ب سادگی یا دشواری جریان یافتن بتن یا به بیان دیگر به روانایی بتن بستگی دارد. روانایی بتن که با آزمایش اسلامپ سنجیده می شود، بیانگر حرکت پذیری نسبی یا توانایی جاری شدن بتن است و نشان دهنده سادگی آغاز حرکت و جاری شدن بتن است. بنابراین، روانایی و اسلامپ بتن تازه به شکل و بافت سطحی سنگدانه ها (تعداد نقاط تماس دانه ها) و به مقدار آب (فاصله بین دانه ها) بستگی دارد و برای بتنی با سنگدانه مشخص (شکل و بافت ثابت) فقط به مقدار آب بستگی دارد.
پس از اختلاط از آنجا که بخشی از آب جذب سنگدانه ها می شود یا در فرآیند آبگیری سیمان مصرف می شود و بخشی دیگر در فضای بین محصولات آبگیری محبوس و جذب سطحی می شود، به تدریج آب آزاد کمتری در محیط اختلاط باقی می ماند و سبب کاهش روانایی بتن (یا افزایش تنش برشی T0) می شود که با افت اسلامپ همراه است. اگر علاوه بر کاهش مقدار آب در محیط بتن اندر کنش فزاینده بین محصولات آبگیری نیز در نظر گرفته شود دلیل کاهش روانایی آشکار خواهد شد. برای نمونه به ازای هر 2 لیتر کاهش یا افزایش مقدار آب اسلامپ حدود یک سانتیمتر کاهش یا افزایش می یابد.
برای آنکه دانه های سنگی در بتن بر روی یکدیگر بلغزند و جابجا شوند باید خمیر سیمان (که سیالی تراکم ناپذیر است) بتواند در فضاهای خالی بین دانه ها جابجا شود. از آنجا که این خمیر به همراه ریزدانه ها سیالی با گرانروی (ویسکوزیته) زیاد است در برابر جریان از خود مقاومت نشان می دهد. این پدیده که کنترل کننده سرعت حرکت و آهنگ جاری شدن بتن (پس از شروع جاری شدن بتن) است به نام گرانروی خمیری شناخته می شود و با µ در معادله نشان داده می شود. گرانروی خمیری بیانگر قوام (درون چسبی) بتن نیز هست و نشانگر پایداری مخلوط بتن و ایستادگی در برابر جداشدگی و آب انداختن بتن است.
بنابراین می توان پذیرفت که کارپذیری یا کارآیی بتن و ملات تازه از دو بخش روانایی و درون چسبی (قوام) تشکیل می شود. روانایی که بیانگر سادگی آغاز جریان یافتن بتن است به تعداد و ماهیت نقاط تماس
دانه های سنگی بستگی دارد . درون چسبی یا قوام بیانگر توانایی بتن تازه برای حفظ و نگه داری همگنی آن است و متناسب با گرانروی خمیری است.
جامدشدگی نتیجه و برآیند شکل گیری محصولات آبگیری و درهم قفل شدن و درهم تنیدگی آنها است و به نام گیرش شناخته می شود. تا پیش از آنکه گیرش رخ دهد، دانه ها و ذرات بتن می توانند نسبت به یکدیگر جابجایی نسبی داشته باشند گو اینکه با پیشرفت فرآیند آبگیری امکان جابجایی محدود و محدودتر می شود. به دلیل همین محدودیت حرکتی ذرات و یون ها است که مقاومت الکتریکی خمیر سیمان در زمان گیرش افزایش ناگهانی می یابد. پدیده گیرش بتن به دو بخش گیرش اولیه و گیرش نهایی تقسیم می شود. گیرش اولیه که تقریباً همزمان با شروع دوره شتابنده در نمودار گرماسنجی رخ می دهد بیانگر به پایان رسیدن زمان کارپذیری بتن است. گیرش نهایی که به طور تقریبی با پایان دوره شتابنده در نمودار گرماسنجی همراه است نشان دهنده آغاز دوره کسب مقاومت های مکانیکی در بتن است.
تعریف و دسته بندی
کندگیر کننده ها یا افزودنی های کندگیر کننده سبب کاهش آهنگ و روند آبگیری سیمان می شوند و آغاز گیرش آن را به تاخیر می اندازند و زمان گیرش را طولانی تر می کنند. افزودنی های کندگیر کننده مواد آلی یا ترکیبی از مواد آلی و معدنی هستند که برای حفظ حالت خمیری و پایش کارپذیری (کارآیی) بتن یا ملات تازه به مخلوط افزوده می شوند.
کندگیر کننده ها با توجه به میزان تاخیری که در گیرش پدید می آورند به دو دسته کندگیر کننده های هنجار (معمولی) و دیرگیر کننده ها تقسیم می شوند. دیرگیر کننده ها به نام افزودنی های کنترل کننده آبگیری نیز شناخته می شوند.
کندگیر کننده های هنجار (یا کُندسازها) شامل کندگیر کننده های مستقل (ASTM C494 Type B) یا همراه با کاهنده های آب (ASTM C494 Type D&G) هستند که قادرند زمان گیرش اولیه را براساس دسته بندی استاندارد ASTM C494، آیین نامه بتن ایران و دیگر استانداردهای معتبر بین المللی از یک تا سه و نیم ساعت به تاخیر اندازند. پس از سپری شدن این تاخیر زمانی یا افزایش دوره سکون و آرامش در روند آبگیری، گیرش سیمان به طور هنجار ادامه می یابد.
دیرگیر کننده ها که به نام فراکندگیر کننده ها هم نامیده می شوند آن دسته از کندگیر کننده های آلی و مستقل هستند که قادرند آبگیری سیمان را متوقف کنند و ساعت های طولانی (حتی تا 72 ساعت) تاخیر در گیرش بتن پدید آورند.
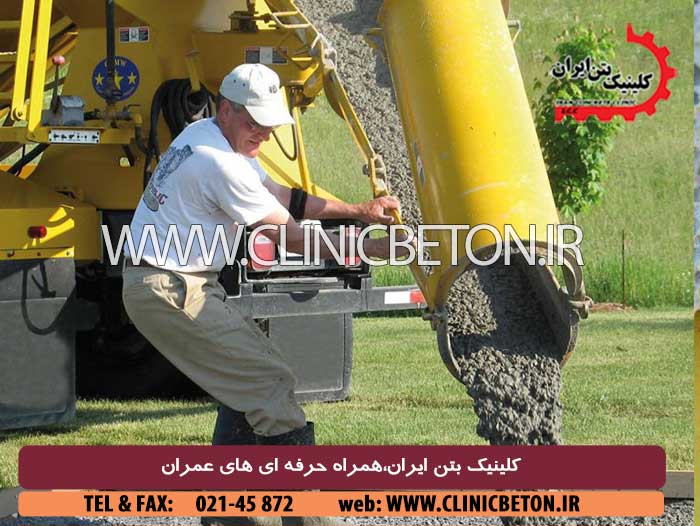
مکانیزم عملکرد کندگیر کننده ها
کندگیر کننده ها از نوع افزودنی های با عملکرد شیمیایی هستند. این افزودنی ها در فرآیند آبگیری سیمان دخالت می کنند یا روند شکل گیری و ساختار محصولات آبگیری را تغییر می دهند (دگرسان می کنند).
همچنان که گفته شد آبگیری سیمان یک فرآیند حل شدن و رسوب کردن است که پیامد آن جوانه زنی و رشد (رویش) محصولات آبگیری بر سطح دانه ها یا در فضای خالی بین دانه های سیمان است. گسترش و در هم تنیده شدن محصولات آبگیری سبب جامد شدن و گیرش خمیر سیمان و بتن می شود. بنابراین برای به تاخیر انداختن روند واکنش آبگیری دو راهکار کلی می تواند وجود داشته باشد. نخستین راهکار، ک��ستن از سرعت و آهنگ تجزیه آمیزه های (ترکیبات) سیمان است. راهکار دوم کندکردن روند شکل گیری محصولات آبگیری و به تاخیر انداختن در هم تنیدگی محصولات آبگیری است. در این راستا می توان چگونگی کارکرد افزودنی های کندگیر کننده را به دو شیوه کنترل سرعت تجزیه و کنترل شکل گیری محصولات آبگیری (کنترل در هم تنیدگی) تقسیم کرد.
با توجه به گوناگونی مواد اولیه مصرفی در تولید افزودنی های کندگیر کننده و اندرکنش شیمیایی جداگانه آنها در روند آبگیری سیمان، نمی توان سازوکار (مکانیزم) یکسانی را برای عملکرد همه آنها تعریف کرد. با این حال می توان سازوکار (مکانیزم) یکسانی را برای عملکرد همه آنها تعریف کرد. با این حال می توان سازوکار و چگونگی کُند کردن یا جلوگیری از آبگیری سیمان را به چهار دسته الف) کمپلکس شدن کلسیم، ب) کُندسازی روند جوانه زدن، پ) جذب سطحی و ت) لایه محافظ (ایجاد لایه بازدارنده) تقسیم کرد.
محیط آبگیری خمیر سیمان پرتلند را می توان متشکل از برخی آنیون های با بار الکتریکی منفی (مانند سیلیکات و آلومینات) و کاتیون های با بار الکتریکی مثبت (مانند کلسیم) انگاشت که انحلال پذیری هر یک از آنها به نوع و غلظت دیگر یون های مثبت یا منفی موجود در محلول بستگی دارد. یون های کلسیم که از تجزیه آمیزه های سیمان و گچ در محیط آزاد می شوند با یون های هیدروکسید و با آلومینات ها و سیلیکات ها واکنش می کنند و هیدرات ها (محصولات آبگیری) را پدید می آورند که به شکل جوانه بر سطح دانه های سیمان یا در فضای خالی بین دانه ها نمایان می شوند. با ادامه واکنش (به شرط حضور و وجود یون های کلسیم، سیلیکات و آلومینات در محیط واکنش) این هیدرات ها رشد می کنند و گسترش می یابند.
از آنجا که تجزیه و واردن شدن یون ها (به ویژه یون های سیلیکات، آلومینات، کلسیم و سولفات) پدیده حاکم بر فرآیند آبگیری سیمان در زمان های اولیه پس از تماس آب با سیمان است برخی از کُندگیر کننده ها با کاستن از سرعت تجزیه کاتیون ها و آنیون ها و کاهش آهنگ ورود یون ها به محلول و محیط واکنش، روند واکنش آبگیری را کُند می کنند. چنانچه یون های کلسیم آزاد شده در محیط به هر شیوه دیگری به جز واکنش با سیلیکات ها و آلومینات ها مصرف شوند یا واکنش آنها با سیلیکات ها و آلومینات ها کُند شود، محیط واکنش از آلومینات ها و سیلیکات های واکنش نکرده اشباع می شود و روند تجزیه دانه های سیمان کاهش می یابد که پیامد کُند شدن روند آبگیری سیمان و تاخیر در گیرش باشد. یکی از شیوه های مصرف یون های کلسیم و بیرون بردن آنها از محلول و محیط واکنش، کمپلکس شدن این یون ها است.
کمپلکس شدن (پُرسازند شدن) به واکنش های بین یون های ساده و شکل گیری کمپلکس های (پرسازندهای) یونی یا بین کمپلکس های (پُرسازندهای) مولکولی جذب شده روی سطح جامد گفته می شود. کمپلکس (پُرسازند) هر آمیزه شیمیایی است که در آن از بر هم کنش الکترون های گروه دهنده با اربیتال های خالی گروه پذیرنده، پیوند ایجاد می شود.
مصرف یون های کلسیم به شیوه کمپلکس شدن کلسیم به دو روش انجام می شود. روش اول در برگیرنده خارج کردن (بیرون بردن) یون های کلسیم از محلول با تشکیل (شکل گیری) نمک های کلسیم نامحلول حاصل از واکنش بین یون های کلسیم با آنیون هایی است که توسط افزودنی کُندگیر کننده وارد محلول شده اند و واکنش پذیری آنها بیشتر و پرشتاب تر از آنیون های سیمان (سیلیکات ها و آلومینات ها) است. روش دوم در برگیرنده کی لیت (به دام انداختن) یون های کلسیم در محلول و جلوگیری از شکل گیری کلسیم هیدروکسید (CH) یا پرتلندیت و کلسیم سیلیکات هیدراته (C-S-H) است. در کی لیت شدن (به دام انداختن)، مولکول های خطی مواد کُندگیر کننده (که دارای فلزات کمپلکس هستند) با به دام انداختن یون های کلسیم موجود در محلول به مولکول های حلقه ای شکل پایدار تغییر می کنند و یون های کلسیم را از محلول و محیط واکنش خارج می کنند (بیرون می برند).
نکته: کُندگیر کننده هایی که با وارد کردن یون (آنیون یا کاتیون) به محلول سبب مصرف یون های کلسیم می شوند بسته به نوع و مقدار مصرف می توانند باعث کُندگیری سیلیکات ها (C3S)، کُندگیری آلومینات ها (C3A) یا هر دو شوند. موادی از این دست ممکن است کارکردی دوگانه داشته باشند یعنی در مقادیر مصرف کم اثر کُندگیری و در مقادیر مصرف زیاد اثر زودگیری از خود نشان می دهند (یا برعکس).
برخی از کُندگیر کننده ها با جلوگیری از انباشته شدن (مقادیر مورد نیاز) یون های کلسیم در پیرامون خوشه های هیدرات ها (محصولات آبگیری) از رشد بلورهای C-S-H و Ca(OH)2 در دنباله و پیرامون ریز خوشه ها جلوگیری می کنند و روند رشد جوانه ها و آهنگ در هم تنیدگی آنها را کُند می کنند. این سازوکار کُند کردن روند آبگیری سیمان به نام کُندسازی جوانه زنی شناخته می شود.
در سازوکار جذب سطحی کنترل آبگیری سیمان، گروهی از کُندگیر کننده ها به طور مستقیم جذب دانه های سیمان و محصولات آبگیری (هیدرات ها) می شوند و با پوشاندن بخش هایی از سطح آبگیری نکرده دانه های سیمان یا سطح هیدرات های شکل گرفته، از پیشرفت واکنش با آب جلوگیری می کنند و روند آبگیری را کُند می سازند و دوره آرامش یا سکون بتن تازه را افزایش می دهند. کُندگیر کننده هایی که جذب سطح هیدرات ها (ذرات آبگیری کرده) یا سطح دانه های آبگیری نکرده سیمان می شوند عموماً از نوع عوامل اثر کننده بر سطح (مانند گلوکونات ها، لیگنوسولفونات ها و قندها) هستند که در زنجیره هیدروکربنی خود دارای گروه های قطبی باشند. این نوع کُندگیر کننده ها علاوه بر پوشاندن بخشی از سطح دانه های سیمان که سبب تاخیر در فرآیند آبگیری می شود (تاثیر مستقیم)، با پراکندن و دور کردن دانه ها از یکدیگر سبب به تاخیر افتادن در هم تنیدگی محصولات آبگیری نیز می شوند (تاثیر غیر مستقیم) و به حفظ کارپذیری (کارآیی) کمک می کنند.
در این سازوکار یک لایه نیمه تراوای فراگیر متشکل از نمک های کلسیم با انحلال پذیری بسیار کم در کل سطح دانه های سیمان و بر روی ذرات هیدراته شده و هیدراته نشده شکل می گیرد و مانند یک لایه بازدارنده و محافظ از رسیدن آب به سطح دانه های سیمان جلوگیری و روند آبگیری را بسیار کُند و تقریباً متوقف می کند. خاصیت اُسمزی سبب درون کشیده شدن آب از میان این غشای نیمه تروا به سوی ذرات هیدراته نشده می شود. جریان یافتن آب به درون غشای نیمه سبب افزایش فشار درون غشا می شود و در نهایت به پارگی غشا می انجامد. پس از پاره شدن غشا، فرآیند آبگیری به طور معمولی ادامه می یابد.. دیرگیر کننده ها عموماً دارای چنین سازوکاری هستند.
دیرگیر کننده ها دارای عملکرد دوگانه هستند، یعنی علاوه بر تشکیل غشایی در اطراف مواد سیمانی هیدراته نشده و جلوگیری از آبگیری آنها، دارای خاصیت پراکندن ذرات هم هستند و از لخته شدن ذرات چه آنها که آبگیری کرده اند و چه آنها که آبگیری نکرده اند جلوگیری می کنند. به همین دلیل است که دیرگیر کننده ها از توان کُندگیری بیشتری برخوردارند و می توانند بتن تولید شده را برای ساعت ها و یا روزهای بعدی به شکل کاملا تازه و کارپذیر (کارآ) نگه دارند.
نکته 4-2- از آنجا که سرعت واکنش آلومینات ها در زمان تماس با آب بسیار بیشتر از سیلیکات ها است، بخش های هیدراته شده کلینکر (بخش آلومینات ها) دارای سطح جانبی زیادی خواهند بود که به طور کامل با غشای نیمه تراوا پوشانده نمی شوند و نمی توان از دسترسی آب و جابه جا شدن یون ها در چنین بخش هایی به طور کامل جلوگیری کرد. به همین دلیل روند واکنش کلسیم آلومینات ها اندکی کُند می شود در حالیکه واکنش کلسیم سیلیکات ها (که تقریباً با غشای تراوا پوشانده شده اند) و شکل گیری C-S-H و Ca(OH)2 بسیار کُند و آهسته خواهد شد. به بیان دیگر کارکرد دیرگیر کننده ها بر کُندکردن روند واکنش سیلیکات ها بسیار بیشتر از آلومینات ها است.
مواد تشکیل دهنده کندگیر کننده ها
موادی که به عنوان کُندگیر کننده (هنجار یا دیرگیر) به کار می روند، معمولاً شامل آمیزه ها (ترکیبات) و مشتقات مواد شیمیایی زیر هستند که ممکن است به تنهایی یا در ترکیب با سایر مواد آلی یا معدنی مورد استفاده قرار گیرند:
- نمک ها، مشتقات و آمیزه های (ترکیبات) اسید لیگنوسولفونیک و لیگنوسولفونات ها
- برخی از نمک های نفتالین سولفونیک اسید با جرم ملکولی سنگین
- کربوهیدرات ها، پلی ساخاریدها، گلوکنات ها، ساکاروز، شکر، ملاس و انواع مواد قندی
- برخی از نمک های فلزات دو خصلتی (فلزاتی که همزمان خاصیت بازی و اسیدی دارند) مانند روی، سرب و قلع
- نمک های اسید (هایدروکسیلیت) کربوکسیلیک و مشتقات آن
- برخی از هیدروکربن ها با فرمول کلی Cn(H2O)n (مانند شیر ذرت)
- نمک های سدیم اسیدهای فسفریک، بوریک و اگزالیک و برخی از نمک های غیرآلی مانند فسفات ها و بورات ها
- نمک های آلی فسفونات ها که بیشتر دیرگیر کننده ها از این نمک ها ساخته می شوند
نکته: بیشتر کُندگیر کننده ها چند سازوکاره هستند یعنی برای کُند کردن روند آبگیری و ایجاد تاخیر در گیرش از دو یا چند (بیش از یک) سازوکار (مکانیزم) بهره می گیرند.
کاربرد همانند سایر افزودنی های شیمیایی بتن، کندگیر کننده ها نیز پاسخگوی نیازهای متعددی در کارگاه هستند. در شرایط آب و هوایی ایران که در منطقه گرم و خشک طبقه بندی می شود همواره گیرش های زود هنگام باعث بروز مشکلات متعدد اجرایی می شوند و به همین دلیل، شاید تاکید و توجه ویژه به این نوع افزودنی ها و گنجاندن آنها در مشخصات فنی مربوط به طرح اختلاط بتن ضروری به نظر می رسد. افزودنی های کندگیر کننده، به شرط کارشناسی و استفاده آگاهانه، می توانند بسیاری از مشکلات اجرایی و نتایج نامطلوب بتن سخت شده را (که به دلیل سرعت روند گیرش بتن پدید می آیند) برطرف نمایند. افزودنی های کندگیر کننده هزینه اجرای سازه های بتن مسلح را به ویژه در شرایط آب و هوایی گرم به طور چشمگیری کاهش می دهند.
نکته: کُندگیر کننده ها می توانند همراه با کاهنده های آب (استفاده از روان کننده ها یا فوق روان کننده هایی که اثر جانبی کندگیری دارند) یا به تنهایی (کندگیر کننده مستقل) به مخلوط های پایه سیمانی افزوده شوند. کُندگیر کننده های هنجار به هر دو صورت می توانند به کار روند ولی دیرگیر کننده ها به تنهایی به کار می روند.
کاربرد اصلی کندگیر کننده ها به تاخیر انداختن زمان گیرش برای حفظ کارپذیری (کارآیی) بتن تازه یا کنترل روند واکنش آبگیری سیمان است ولی از آنجا که دامنه تاخیرزایی کندگیر کننده های هنجار با دیرگیر کننده ها متفاوت است کاربرد آنها نیز اندکی با یکدیگر تفاوت دارد.
کاربرد کندگیر کنن��ه های هنجار (کُندسازها)
این نوع کُندگیر کننده ها زمان گیرش اولیه بتن را بین 1 تا 5/3 ساعت به تاخیر می اندازد و مکانیزم عملکرد آنها معمولاً کمپلکس کردن کلسیم و جذب سطحی و در مواردی نیز کُندسازی روند جوانه زدن محصولات آبگیری است. این نوع کندگیر کننده ها تنها روند آبگیری آمیزه های سیمان (به ویژه C3A یا C3S یا هر دو) را کُند می کنند ولی هرگز روند آبگیری را متوقف نمی کنند مگر آنکه مصرف آنها بیش از اندازه باشد. در این راستا می توان کاربرد کُندگیر کننده های هنجار (کُندسازها) را به ترتیب زیر دسته بندی کرد.
الف) پیشگیری از اثرات ناخوشایند (نامطلوب) هوای گرم
دمای زیاد و هوای گرم سبب شتاب گرفتن واکنش های آبگیری و تسریع در روند آبگیری سیمان می شود. تسریع در روند آبگیری به اثرات نامطلوبی در بتن مانند کاهش زمان گیرش بتن تازه و کاهش مقاومت های دراز مدت بتن سخت شده می انجامد.
آبگیری سیمان یک فرآیند گرمازا است و در هوای گرم که دمای هوای محیط بیشتر از دمای بتن تازه است، پراکنده شدن و تبادل گرمای آبگیری به محیط بسیار به سختی انجام می شود و این گرمای آبگیری انباشته شده در بتن تازه سبب افزایش آهنگ آبگیری سیمان می شود و گیرش را تسریع می کند.
افزایش دما و افزایش آهنگ و سرعت واکنش های آبگیری در بتن تازه سبب نایکنواخت شدن ریزساختار خمیر سخت شده سیمان می شود که پیامد آن کاهش مقاومت در درازمدت است.. همانگونه که در این شکل دیده می شود با افزایش دمای سخت بتن، مقاومت درازمدت آن کاهش می یابد. کُندگیر کننده ها با کاستن از روند و سرعت آبگیری خمیر سیمان در هوای گرم با اثرات نامطلوب هوای گرم بر بتن تازه و سخت شده مقابله می کنند.
ب) حمل و انتقال بتن
در مواردی که زمان بین ساختن بتن تا ریختن آن به هر دلیلی به درازا بکشد، برای کُندکردن روند آبگیری سیمان و جلوگیری از گیرش بتن در مدت زمان انتقال آن به پای کار می توان از افزودنی های کندگیر کننده استفاده کرد. به درازا کشیدن زمان بین ساختن تا ریختن بتن می تواند به دلیل ترافیک درون شهری، ناهمواری راه های دسترسی برون شهری، دشواری عملیات بتن ریزی، یا پراکنده بودن مقاطع کم حجم بتن ریزی (مانند بتن ریزی جان پناه آب گذرها در راهسازی) رخ دهد.
در همه این موارد استفاده از افزودنی کُندگیر کننده برای حفظ حالت خمیری بتن تازه و جلوگیری از افت مقاومت های مکانیکی بتن سخت شده (به دلیل پیشرفت بخشی از آبگیری در زمان طولانی انتقال بتن) ضروری است.
پ) کُندکردن روند گرمازایی در بتن ریزی حجیم
گرمای ایجاد شده در بتن حجیم ناشی از آبگیری باعث پدید آمدن اختلاف دما بین بخش درونی و سطوح بیرونی بتن می شود و چنانچه این اختلاف دما از 20 درجه سانتی گراد فراتر رود می تواند به بروز
ترک های حرارتی بیانجامد.
در چنین مواردی برای پیشگیری از بروز ترک های حرارتی لازم است که تمهیدات و راهکارهای اجرایی و کارگاهی به کار بسته شود تا گرمای آبگیری ایجاد شده کنترل شود و اختلاف دمای درون و بیرون مقطع بتنی به حداقل برسد (رسانده شود). یکی از این راهکارهای اجرایی، کاهش سرعت و روند گرمازایی به ویژه در ساعت های اولیه است که با استفاده از افزودنی های کندگیر کننده قابل دستیابی است.
کُندگیر کننده ها با کُند کردن و ایجاد آرامش در روند آبگیری سیمان، روند آزاد شدن گرمای آبگیری را در ساعت های اولیه به تاخیر می اندازد گو اینکه تاثیری بر مقدار گرمای آزاد شده نهایی ندارند.
نکته: دوباره تاکید می شود که کُندگیر کننده ها نقشی در کاهش مقدار گرمای آبگیری بتن ندارند و تنها روند آزاد شدن آن را دگرسان می کنند (تغییر می دهند).
ت) بتن ریزی با قالب های لغزنده
قالب لغزنده روشی برای اجرای سازه های بتنی است که در آن قالب همزمان با بتن ریزی حرکت می کند. عملیات بتن ریزی در روش قالب لغزنده به طور پیوسته و به آرامی در طول شبانه روز و تا پایان اجرای سازه مورد نظر (دودکش، برج خنک کننده، شفت های بتنی و ...) یا تا رسیدن به مقطعی مشخص از سازه ادامه دارد. در این روش وزن قالب، تجهیزات و پرسنل اجرایی و تمامی بارهای وارده در حین ساخت توسط بتن تحمل می شود. بنابراین بتنی که همزمان با حرکت قالب از زیر قالب بیرون می آید از یک سو باید از مقاومت کافی برای تحمل بارهای وارده برخوردار باشد و از سوی دیگر به اندازه ای سخت نشده باشد که به قالب بچسبد و حرکت قالب را با مشکل مواجه کند. به همین دلیل حرکت قالب های لغزان بسیار کُند و در حدود چند سانتی متر در ساعت است و لازم است که بتن به آرامی ریخته شود و برای حفظ یکپارچگی و پیوستگی بتن باید زمان گیرش آن متناسب با سرعت بتن ریزی و حرکت قالب تنظیم شود. پس بتنی که برای قالب لغزنده استفاده می شود باید دو ویژگی اصلی داشته باشد اول آنکه در ابتدای قالب برای مدت زمان طولانی خمیری باقی بماند (گیرش آن به تاخیر بیفتد) و در انتهای قالب و در زمان بیرون آمدن از زیر قالب از یک سو سخت نشده باشد و از سوی دیگر به اندازه ای گیرش آن پیشرفت کرده باشد که بتواند بارهای وارده را تحمل کند. دستیابی به چنین ویژگی هایی تنها با استفاده از افزودنی های کُندگیر کننده امکان پذیر خواهد بود.
ث) جلوگیری از پدید آمدن درز سرد
در بتن ریزی های حجیم و گسترده که عملیات بتن ریزی در چندین لایه انجام می شود یا در بتن ریزی هایی که به دلیل شرایط اجرایی (مانند پیچیده بودن شکل مقطع بتن ریزی، کُند بودن سرعت تامین بتن، کاهش خودخواسته سرعت بتن ریزی در مقاطع عمیق، دشواری های دسترسی و متراکم کردن بتن و ...) عملیات بتن ریزی به کندی انجام می شود برای حفظ یکپارچگی بتن لازم است که لایه های بتن به یکدیگر بچسبد و پیوند بین آنها تامین شود. برای دستیابی به یکپارچگی لازم است که در هنگام ریختن لایه جدید بتن لایه زیرین یا بتن کناری هنوز خمیری باقی مانده باشد تا در زمان ویبره زدن دو لایه در یکدیگر ادغام شوند و بین سطوح واریزی بتن درز سرد پدید نیاید. در چنین مواردی، کندگیر بودن
بتن هایی که زودتر ریخته می شوند اجتناب ناپذیر است.
در مواردی نیز که به دلیل طراحی، روش اجرا، یا عملیات اجرایی توقف های پیش بینی شده ای در حین بتن ریزی در نظر گرفته می شود می توان با استفاده از کُندگیر کننده ها روند گیرش بتن را به گونه ای تنظیم کرد تا پیوستگی بتن ریخته شده پیش و پس از توقف تامین شود.
ج) جلوگیری از بروز ترک های سازه ای زودهنگام
در بتن ریزی عرشه و تیرهای پل های چند دهانه به دلیل گیرش و سخت شدگی نسبی بتن در تکیه گاه های کناری و میانی در حین بتن ریزی و ایجاد لنگر منفی ناشی از وزن بتنی که در بخش میانی دهانه ریخته می شود خطر ایجاد خمیدگی و پدید آمدن ترک های سازه ای در تکیه گاه ها وجود دارد. استفاده از افزودنی های کُندگیر کننده در بتن ریزی سازه های بتن مسلح پیوسته (مانند تیرهای سراسری با تکیه گاه میانی) با ایجاد گیرش تدریجی و هماهنگ بتن باعث کاهش خطر خمیدگی و ترک خوردن در بتن نیمه سخت شده می شود. بتن کُندگیر شده ای که روی تکیه گاه های میانی ریخته می شود تا هنگامی که همه بتن بخش میانی دهانه ها ریخته شود به حالت خمیری باقی می ماند.
در مواردی که سطح قالب گسترده باشد با پیشرفت بتن ریزی و افزایش بار وارده به تدریج قالب تغییر شکل می دهد و خیر بر میدارد. چنانچه بخشی از بتن ریخته شده گیرش کرده باشد این خیز و تغییر شکل تدریجی قالب سبب پدید آمدن ترک در بتن نیمه سخت می شود. با به کاربردن کُندگیر کننده ها در چنین مواردی می توان شرایطی فراهم کرد که تا پایان بتن ریزی و پیش از گیرش اولیه بتن ریخته شده، تمامی تغییر شکل و خیز در قالب اتفاق بیفتد.
چ) پرداخت سطح و نماسازی
در مواردی که سطح نهایی با دست و با کمک ماله پرداخت می شود، مانند سطوح سرریز سدها و سازه های هیدرولیکی، لازم است که لایه نهایی بتن کندگیر باشد تا عملیات ماله کشی و ماله کاری (لیسه ای کردن سطح) به آسانی و با دقت انجام گیرد. در کفسازی صنعتی که رویه کفسازی بر روی بتن تازه اجرا می شود مانند روش خشکه پاشی یا روش روکش گذاری، برای پیوند بهتر بین لایه روکش سطحی با بتن تازه لازم است که گیرش بتن زیر با استفاده از کُندگیر کننده ها به تاخیر بیفتد.
برای ایجاد نماهای تزیینی با سنگدانه های رنگی (نمای شسته) یا نماهای با سنگدانه نمایان، از کُندگیر کننده های سطحی استفاده می شود. کُندگیر کننده های سطحی خمیرها یا کاغذهای آغشته به کندگیر کننده هستند که پیش از بتن ریزی به سطح درونی قالب مالیده یا به آن چسبانده می شوند. پس از تماس بتن تازه با این خمیر یا کاغذ، بتن مجاور سطح درونی قالب کُندگیر می شود و شیره سیمان پس از بازکردن قالب با فشار آب یا با برس سیمی زدوده می شود.
کاربرد دیرگیر کننده ها
دیر گیر کننده ها که با نام های کنترل کننده های آبگیری یا فراکُندگیر کننده نیز شناخته می شوند دو کارکرد اساسی در گستره تولید و مصرف بتن دارند.
- دیر گیر کننده ها برای باز ایستاندن (متوقف کردن) ادامه فرآیند آبگیری سیمان در بتن برگشتی (اضافی) یا پساب شستشوی ماشین آلات تولید و حمل به کار می آیند و با بازیافت آنها اجازه می دهند به جای آنکه دور ریخته شوند به چرخه تولید و مصرف بتن بازگردانده شوند.
- دیرگیر کننده ها برای ناواکنشگر کردن بتن تازه ساخت به کار می آیند تا کُندگیری درازمدت پدید آروند. این کُندگیری دراز مدت که پیامد ناواکنشگر شدن سیمان است اجازه می دهد که بتن در فواصل حمل بسیار سولانی به شکل خمیری باقی بماند یا در شرایطی که بتن در فواصل طولانی پمپ می شود بتواند کارآیی و اسلامپ خود را حفظ کند.
برپایه این کارکردها می توان کاربرد دیرگیر کننده ها را به سه گروه 1) بازیافت پساب شستشوی بتن، 2) بازیافت و مصرف دوباره بتن تولید شده و 3) حمل بتن تازه در مسافت های بسیار طولانی یا ایجاد وقفه در تخلیه تراک گروه بندی کرد.
الف) بازیافت پساب شستشوی بتن
کمبود آب، لزوم صرفه جویی در مصرف آن به ویژه در واحدهای تولید بتن آماده و پرهیز از آلودن محیط زیست از جمله عوامل تاثیرگذار در راستای توسعه پایدار هستند که در سال های اخیر استفاده از نوعی دیرگیر کننده را متداول ساخته است که به جای شستن ماشین آلات تولید و کامیون های حمل بتن و دور ریختن پساب شستشو در پایان هر نوبت کاری، از پساب شستشوی بتن که دور ریز نشده و در ماشین آلات باقیمانده است برای ساخت بتن در نوبت کاری بعدی استفاده کرد.
افزودنی های دیرگیر کننده ای که برای جلوگیری از دور ریز پساب شستشوی بتن به کار می روند به نام افزودنی های بازیافت پساب شناخته می شوند. افزودنی های بازیافت پساب افزون بر جلوگیری از آبگیری سیمان در بتن سخت نشده در پساب شستشوی داخل دیگ مخلوط کننده، از ته نشین شدن ذرات معلق در پساب و تشکیل قشری از سیمان سخت شده در پایین دیگ اختلاط یا بر روی پره ها جلوگیری می کنند. پساب شستشو در نوبت کار بعدی به عنوان بخشی از آب و ریزدانه در ساخت بتن در نظر گرفته می شود.
ب) بازیافت و مصرف دوباره بتن تولید شده
در مواردی که به دلیل خراب شدن دستگاه های انتقال و ریختن بتن، یا به دلیل مشکلات پیش بینی نشده اجرایی (مانند در رفتن قالب)، یا برآورد نامناسب در تخمین حجم بتن مورد نیاز بخشی از بتن ساخته شده مصرف نشود و بازگردانده شود می توان با استفاده از دیرگیر کننده ها گیرش بتن باقی مانده در دیگ کمیون بتن بَر (تراک میکسر) را برای مدت زمان لازم به تاخیر انداخت و بتن باقیمانده را در همان روز یا در روز بعد استفاده کرد.
دیرگیر کننده ها برای کنترل فرآیند آبگیری سیمان و توقف گیرش و نگه داری بتن تولید شده در طول شب یا حتی تعطیلی آخر هفته به کار می آیند به گونه ای که می توان بتن باقیمانده در ماشین آلات و تراک ها را در نوبت کاری بعدی به کار برد.
بسته به نوع و مقدار مصرف دیرگیر کننده به کار رفته برای کنترل واکنش آبگیری در بتن تولید شده ممکن است که برای مصرف دوباره چنین بتنی و آغاز دوباره آبگیری به ماده فعال کننده (یا شتاب دهنده) نیاز باشد که پیش از مصرف دوباره به بتن داخل دیگ افزوده می شود.
پ) حمل بتن در مسافت های بسیار طولانی
از دیرگیر کننده ها می توان برای پیشگیری از واکنش های شیمیایی و متوقف کردن فرآیند آبگیری سیمان بهره گرفت تا امکان حمل بتن در مسافت های بسیار طولانی فراهم آید بدون آنکه اسلامپ آن افت چشمگیری داشته باشد یا دمای آن افزایش محسوسی پیدا کند. برای چنین کاربردی باید دیرگیر کننده همزمان با اختلاط یا بی درنگ پس از اختلاط به بتن افزوده شود. پس از آنکه افزودنی به طور کامل با بتن تازه در آمیخت باید دیگ کامیون با آهسته ترین دور ممکن بچرخد. مقدار مصرف افزودنی دیرگیر کننده باید متناسب با فاصله حمل بتن تنظیم شود. در حالت ایده آل باید اثر دیرگیر کنندگی افزودنی مصرف شده پس از رسیدن بتن به پای کار به پایان برسد تا بتن دیرگیر شده بتواند همانند یک بتن معمولی گیرش کند. این شیوه کاربرد به ویژه در تابستان و در هوای گرم که آبگیری به دلیل افزایش دمای بتن شتاب می گیرد بسیار سودمند است.
برای بتن پاشی به شیوه خیش در داخل تونل ها می توان از دیرگیر کننده ها (کنترل کننده های آبگیری) استفاده کرد و بتن تازه را ساعت ها در داخل دیگ کامیون بتن بَر (تراک میکسر) در حالت خمیری حفظ کرد. سپس در زمان مصرف با افزودن بخشینه (جزء) فعال کننده یا با استفاده از افزودنی زودگیر کننده، گیرش بتن از سرگرفته می شود. بنا به نیاز و با تنظیم مقدار زودگیر کننده می توان زمان گیرش اولیه بتن پاششی را به چند ثانیه رسانید.
تاثیر کندگیر کننده ها بر ویژگی های بتن تازه
کُندگیر کننده های هنجار و دیرگیر کننده ها علاوه بر تاثیری که روی روند آبگیری سیمان و زمان گیرش بتن دارند (که به طور کامل و با جزئیات به آن اشاره شد)، بر برخی دیگر از ویژگی های بتن تازه نیز تاثیر گذار هستند.
1- کارپذیری (کارآیی)
همچنان که گفته شد کارپذیری (کارآیی) بتن و ملات تازه از دو بخش روانایی و درون چسبی (قوام) تشکیل می شود. روانایی که بیانگر سادگی آغاز جریان یافتن بتن است به تعداد و ماهیت نقاط تماس دانه های سنگی بستگی دارد و متناظر با تنش جاری شدن است. درون چسبی یا قوام بیانگر توانایی بتن تازه برای حفظ و نگه داری همگنی آن است و متناسب با گرانروی خمیری است.
روانایی بتن که با آزمایش اسلامپ سنجیده می شود برای یک بتن مشخص به مقدار آب اختلاط بستگی دارد. مصرف شدن آب بتن تازه برای واکنش های آبگیری سیمان یا جذب شدن مولکول های آب به سطح دانه ها و ذرات و نیز تبخیر شدن آب از جمله عواملی هستند که سبب کاهش تدریجی آب در بتن تازه و در نتیجه کاهش تدریجی روانایی (یا افت اسلامپ) در بتن تازه می شوند.
از آنجا که کُندگیر کننده های هنجار نقشی در کاهش روند جذب شدن آب به سطوح دانه ها و ذرات ندارند و از وانکش های آبگیری سیمان هم به طور کامل جلوگیری نمی کنند، بنابراین تاثیر بسیار اندکی بر کاهش روند افت اسلامپ دارند. به بیان دیگر، کُندگیر کننده های هنجار نقشی در حفظ اسلامپ بتن تازه ندارند و در مواردی حتی ممکن است روند افت اسلامپ را نیز افزایش دهند. کُندگیر کننده های هنجار با کُند کردن سرعت شکل گیری محصولات آبگیری سبب کاهش روند در هم تنیدگی آنها می شوند و در نتیجه روند افزایش گرانروی خمیری را تا حدود زیادی کاهش می دهند و به حفظ جاپذیری بتن تازه کمک می کنند. بتن دارای کندگیر کننده هنجار در مقایسه با بتن شاهد (بدون افزودنی) ویژگی متراکم شدن (ویبره شدن) خود را بیشتر حفظ می کند.
دیرگیر کننده ها به دلیل باز ایستادن و توقف واکنش آبگیری (کاهش مصرف آب بتن تازه) به حفظ اسلامپ بتن تازه کمک می کنند و ویژگی جاپذیری بتن را نیز حفظ می کنند.
2- دمای بتن
کُندگیر کننده ها دمای بتن تازه را کاهش نمی دهند و تاثیری بر مقدار گرمای آبگیری ندارند ولی روند آزاد شدن گرمای آبگیری سیمان را کُند می کنند. دیرگیر کننده ها به دلیل باز ایستادن فرآیند آبگیری از افزایش دمای بتن تازه در حین انتقال جلوگیری می کنند.
3- مقدار هوای بتن
کُندگیر کننده های هنجار، به غیر از آنهایی که خاصیت روان کنندگی هم دارند (مانند لیگنوسولفونات ها و گلوکونات ها)، عموماً نقشی در افزایش یا کاهش مقدار هوای بتن تازه ندارند ولی به دلیل آنکه زمان خمیری بودن بتن را افزایش می دهند زمان بیشتری برای خروج حباب های هوا فراهم می آورند و روند افت (از دست دادن) مقدار هوای بتن تازه را اندکی افزایش می دهند.
4- نشست خمیری و آب انداختن
به ته نشین شدن ذرات جامد (تحت اثر وزن خودشان) در یک بتن یا ملات تازه، که پس از ریختن و پیش از آغاز گیرش بتن رخ می دهد، نشست خمیری گفته می شود. کُندگیر کننده ها با افزایش زمان گیرش و حفظ بتن در حالت خمیری، پتانسیل نشست خمیری را در بتن یا ملات تازه افزایش می دهند.
آب انداختن به بالا آمدن خود به خود آب از درون بتن ریخته شده به سطح آن گفته می شود که به دلیل نشست خمیری بتن رخ می دهد. افزودنی های کُندگیر کننده به دلیل افزایش پتانسیل نشست خمیری در بتن یا ملات تازه، پتانسیل آب انداختن بتن را (به شرط آنکه بتن خود مستعد آب انداختن باشد) افزایش می دهند.
تاثیر کندگیر کننده ها بر ویژگی های بتن سخت شده
افزودنی های کُندگیر کننده با کُند کردن روند آبگیری سیمان بر روند شکل گیری محصولات آبگیری تاثیر می گذارند و ریزساختار بتن سخت شده را بهبود می دهند. تاثیر این افزودنی ها بر روی بتن سخت شده پیامد نقش آنها بر روی بتن تازه است.
1- مقاومت
مقاومت های کوتاه مدت بتن دارای افزودنی کُندگیر کننده از بتنی همسان و بدون افزودنی (بتن شاهد) کمتر است، در حالی که مقاومت های دراز مدت آن بیشتر از بتن شاهد خواهد بود.. کمتر بودن مقاومت کوتاه مدت به ویژه مقاومت یک روزه بتن دارای کُندگیر کننده نسبت به بتن همسان و بدون کُندگیر کننده به دلیل تاخیری است که کُندگیر کننده ها در روند و سرعت آبگیری سیمان در ساعات اولیه پدید می آورند.
2- ریز ساختار بتن
با کُند شدن روند شکل گیری هیدرات های آبگیری سیمان به دلیل کُند شدن روند واکنش های آبگیری، هیدرات های آبگیری در ساعات اولیه به شکل جوانه های کوچک و فشرده بر روی سطح دانه ها یا در فضای خالی بین دانه ها امکان رشد پیدا می کنند. این به آن معنی است که هیدرات های آبگیری ساختاری فشرده و توپُر پیدا خواهند کرد و ریزساختار بتن را بهبود می بخشند. هر چقدر ریزساختار بتن یکنواخت تر و همگن تر باشد پایایی بتن افزایش خواهد یافت. بنابراین انتظار می رود که استفاده از کُندگیر کننده ها در بتنی که به خوبی ساخته و عمل آوری شود به بهبود ریزساختار بتن بیانجامد و در درازمدت به پایایی بتن کمک کند.
کُندگیر کننده ها با به تاخیر انداختن گیرش اولیه بتن و حفظ حالت خمیری بتن امکان دوباره متراکم کردن بتن به روش بازلرزاندن را فراهم می کنند. بازلرزاندن بتنی که نشست خمیری خود را انجام داده است بیرون راندن حباب های هوا و از بین رفتن حفره ها و فضاهای خالی می شود که در اثر نشست خمیری بتن به ویژه در زیر دانه های درشت و زیر میلگردها پدید آمده اند. امکان بازلرزاندن بتن که دستاورد کُند شدن روند گیرش آن به دلیل استفاده از کُندگیر کننده ها است، می تواند به بهبود پیوستگی بتن و میلگرد نیز کمک کند.
تاثیر اجزای بتن بر عملکرد کندگیر کننده ها
اجزای تشکیل دهنده بتن و به خصوص ترکیبات سیمان تاثیر قابل توجهی بر عملکرد افزودنی کندگیر کننده دارند. برخی از سیمان ها دارای خاصیت کندگیری هستند و گیرش بتن را به تاخیر می اندازند، تاخیر ایجاد شده بایستی در محاسبه به زمان گیرش در نظر گرفته شود. مشاهده گردیده است که انواع مختلف سیمان، یا یک نوع مشخص سیمان تولیدی کارخانه های مختلف، یا محموله های مختلف سیمان از یک نوع و یک کارخانه معین به دلیل تغییر ریزدانگی، تغییر سازنده های شیمیایی یا تغییر هر دو، برای دستیابی به مقدار مشخصی از کُندگیری به مقادیر متفاوتی از یک نوع کُندگیر کننده نیاز دارند. این مسئله لزوم انجام آزمایش های اولیه کارگاهی برای تعیین مقدار مصرف و همچنین تداوم این آزمایش ها بر روی محموله های سیمان ورودی به کارگاه را ضروری می سازد.
وجود کاتیون های تک ظرفیتی (مانند K+ یا Na+) در محیط واکنش سیمان و آب سبب کاهش انحلال پذیری یون کلسیم Ca2+ می شود در حالی که انحلال پذیری یون های سیلیکات و آلومینات را افزایش
می دهد. چنانچه غلظت این کاتیون ها در محیط واکنش پایین باشد، تاثیر حاکم بر روند واکنش کاسته شدن انحلال پذیری یون های کلسیم است که پیامد آن کُندگیر شدن است. در حالیکه در غلظت های بالا تاثیر حاکم بر روند واکنش، افزایش یون های سیلیکات و آلومینات است که پیامد آن زودگیر شدن است. بنابراین برای یک کُندگیر کننده مشخص، افزایش (یا کاهش) مقدار قلیایی های سیمان (K2O , Na2O) باعث کاهش (یا افزایش) میزان اثر گذاری کُندگیر کننده می شود. به بیان ساده تر برای دستیابی به سطح مشخصی از کُندگیری، سیمان های با قلیایی کمتر به افزودنی کندگیر کننده کمتری نیاز دارند.
کارآمد بودن و میزان اثرگذاری یک کُندگیر کننده به مقدار آلومینات های سیمان به ویژه C3A نیز بستگی دارد. از آنجا که واکنش پذیری آلومینات بیشتر از سیلیکات است مقدار بیشتری از کُندگیر کننده در طی شکل گیری هیدرات های آبگیری C3A در محیط مصرف می شوند و کُندگیر کننده کمتری برای به تاخیر انداختن واکنش سیلیکات در دسترس باقی می ماند.
به بیان دیگر، سیمان های با آلومینات کمتر (یا با سیلیکات بیشتر) برای دستیابی به سطح مشخصی از کُندگیری به مقدار کمتری از افزودنی کُندگیر کننده نیاز دارند. وجود پوزولان ها در سیمان یا افزودن مواد پوزولانی به بتن برگیرش بتن اثر می گذارد و به همین دلیل باید مقدار مصرف کندگیر کننده در هر بار تغییر در مقدار پوزولان مجدداً بررسی شود. برای نمونه، تغییر سیمان کارگاه از نوع 2 به سیمان پوزولانی باعث تاخیر در زمان گیرش می شود و لازم است قبل از استفاده از سیمان پوزولانی مقادیر جدید مصرف کندگیر کننده توسط آزمایش های کارگاهی تعیین شود.
برخی از کُندگیر کننده ها به دلیل تغییری که در روند شکل گیری اترینگایت پدید می آورند ممکن است بر رفتار سیمان های منبسط شونده یا بر عملکرد افزودنی های منبسط کننده تاثیر بگذارند. وجود کاهنده های آب (به دلیل پراکنشی که بین دانه های سیمان پدید می آورند) می تواند به کُند شدن روند در هم تنیدگی محصولات آبگیری بیانجامد و به کُند شدن روند آبگیری بتن اندگی کمک کند. بنابراین برای تعیین مقدار مصرف کُندگیر کننده های مستقل در بتن های دارای کاهنده آب باید این تاثیر کاهنده های آب نیز در نظر گرفته شود.
برخی از سیمان ها در مقادیر مصرف کُندگیر کننده رفتار سفت شدگی سریعی از خود نشان می دهند که می تواند به افت شدید اسلامپ بیانجامد که پیامد آن دشواری در ریختن، متراکم کردن و پرداخت کردن بتن است.
تاثیر عوامل محیطی و اجرایی
دما مهمترین عامل محیطی است که بر عملکرد کندگیر کننده تاثیر مستقیم دارد. یکی از دلایل اصلی توصیه مصرف کندگیر کننده، مقابله با مشکلات به وجود آمده در هوای گرم است. دمای بتن تازه، دمای محیط، رطوبت نسبی، سرعت وزش باد، کارآمد بودن ماشین آلات و تجهیزات تولید و انتقال بتن، زمان حمل و مهارت نیروهای اجرایی از دیگر عوامل تاثیر گذار در عملکرد افزودنی های کندگیر کننده هستند. برای نمونه، چنانچه دما در طول شبانه روز نوسان داشته باشد مقدار مصرف کندگیر کننده در ساعات مختلف روز و شب متفاوت خواهد بود. از دیگر عوامل اجرایی تاثیر گذار بر عملکرد کُندگیر کننده ها می توان به زمان افزودن کُندگیر کننده به مخلوط اشاره کرد. چنانچه کسندگیر کننده اندکی پس از اختلاط همه اجزای بتن به مخلوط افزوده شود، توان و قدرت کُندگیر کنندگی آن افزایش می یابد. زیرا در چنین حالتی بخشی از هیدرات ها (به ویژه آلومینات ها) پیش از افزودن کُندگیر کننده شکل گرفته اند و در ادامه، مقدار کُندگیر کننده کمتری را مصرف و از محیط واکنش خارج می کنند..تاخیر در زمان افزودن کُندگیر کننده به مخلوط بر روند آزاد شدن گرمای آبگیری بتن نیز تاثیر می گذارد.
رهنمودهای اجرایی در کارگاه
معمولاً افزودنی های کندگیر کننده در حالت مایع اندازه گیری و مصرف می شوند و چنانچه این افزودنی ها به شکل جامد (پودر) تحویل گردند، لازم است ابتدا بر طبق پیشنهاد تولید کننده محلولی با درصد جامد مناسب از آن تهیه و سپس مصرف شود.
تمامی افزودنی های کندگیر کننده در محدوده ی زمانی معینی بر مخلوط بتن تاثیر می گذارند و با پایان یافتن این محدوده ی زمانی، آبگیری سیمان از سر گرفته می شود. بنابراین، مقدار مصرف کُندگیر کننده باید به گونه ای تنظیم شود تا فرصت کافی برای ریختن، متراکم کردن، پرداخت سطح و کارهای تکمیلی فراهم شود.
ار آنجا که مصرف بیش از اندازه اغلب کندگیر کننده ها می تواند منجر به گیرش ناهنجار یا ناگیر شدن بتن شود، بنابراین دقت در اندازه گیری و پیمانه کردن از اهمیت ویژه ای برخوردار است. مصرف بیش از اندازه افزودنی کُندگیر کننده ممکن است گیرش و روند کسب مقاومت را به نحو چشمگیری به تاخیر بیاندازد. چنانچه به هر دلیلی (خطای انسانی، خطای دستگاه های اندازه گیری و ...) چنین اتفاقی رخ دهد باید بی درنگ اقدامات زیر به کار بسته شود.
- با به کارگیری روش های مناسب عمل آوری از تبخیر آب بتن جلوگیری شود.
- برای جلوگیری از رخدادن ترک های نشست خمیری در بتن باید عملیات باز لرزاندن بتن تا پیش از گیرش اولیه بتن ادامه یابد.
- با پیگیری از شرکت تولید کننده افزودنی، زمان کُندگیری محتمل و قابل انتظار در موارد مشابه و برای چنین مقدار مصرفی تعیین و تخمین زده شود.
بیشتر بتن هایی که به دلیل مصرف بیش از اندازه کُندگیر کننده دچار کُندگیری ناهنجار شده اند معمولاً پس از 3 تا 5 روز به روند عادی گیرش و کسب مقاومت باز می گردند. چنانچه کُندگیری بیش از 5 روز به درازا بکشد احتمال آنکه مقاومت بتن رشد اندکی داشته باشد بسیار زیاد خواهد بود. چنانچه مقدار کُندگیر کننده افزوده شده به مخلوط بسیار زیاد باشد ممکن است از آبگیری سیمان به طور کامل جلوگیری کند که به نام ناگیر شوندگی شناخته می شود.
رهنمودهای کاربردی
به دلیل تاثیر چشمگیر ویژگی های سیمان مصرفی بر عملکرد افزودنی های کُندگیر کننده، بهترین روش برای بررسی تاثیر کُندگیر کننده ها بر خواص بتن، انجام آزمایش های کارگاهی است. لازم است این آزمایش ها با توجه به اوضاع جوی پیش بینی شده، روش و امکانات عملی ساخت بتن و با استفاده از مصالح مصرفی کارگاه انجام پذیرد. پارامترهایی که انتظار می رود در اثر به کار بردن کندگیر کننده در طرح عملیات بتن ریزی تغییر کنند عبارتن از: زمان و روند گیرش، کُند شدن روند گرمازایی سیمان و بتن، تاخیر در باز کردن قالب ها، افزایش دوره عمل آوری و در مواردی نیاز به بازلرزاندن بتن.
قبل از شروع کار اصلی بهتر است تعداد کافی طرح اختلاط در آزمایشگاه کارگاه تهیه و آزمایش شود و با ثبت نتایج و مقایسه ی آنها طرح های بهینه برای اجرا برگزیده شوند. اگر چه راهنمایی های بسیار مفیدی در آیین نامه های معتبر بین المللی و استانداردهای ساختمانی ایران برای کاربرد افزودنی های شیمیایی وجود دارد، ولی اغلب آنها در شرایط استاندارد و آزمایشگاهی کنترل شده نتیجه گیری شده اند. بنابراین، بهتر است ضمن پیروی از آنها نسبت به انجام آزمایش های کارگاهی نزدیک به شرایط واقعی کاربردی در کارگاه اقدام نمود. چنانچه یک طرح اختلاط بتن دارای کارآیی و قابلیت پرداخت مناسب باشد و لازم شود که به آن ماده کندگیر کننده افزوده شود، تغییری در مقادیر آب اختلاط مورد نیاز اولیه، سیمان یا مقدار حباب های ریز به وجود نمی آید و در نتیجه نیازی به تغییر در نسبت های اجزای بتن نیست. ولی از آنجا که اغلب افزودنی های کندگیر کننده مواد محلول در آب هستند، لازم است در هنگام محاسبه ی آب اختلاط و نسبت آب به سیمان، مقدار آب موجود در این افزودنی ها محاسبه و معادل آن از آب اختلاط کاسته شود. ولی بخش جامد آنها که نسبت به حجم کل بتن بسیار ناچیز هستند معمولاً نادیده گرفته می شوند.
مخازن نگه داری افزودنی ها باید به آسانی قابل شناسایی بوده و محلول ها در برابر آلودگی، تبخیر، رقیق شدن، دمای بسیار بالا یا یخ زدگی محافظت شوند. توجه به زمان انبارداری هر کُندگیر کننده براساس توصیه ی تولید کننده ی آن ضروری است. در آمیختن کُندگیر کننده ها با دیگر افزودنی ها مجاز نیست و باید آنها را به طور جداگانه پیمانه و به مخلوط اضافه کرد مگر آنکه سازگاری آنها با یکدیگر قبلاً توسط تولید کننده تایید شده باشد. برای مثال، ممکن است کندگیر کننده و روان کننده ی خاصی با هم سازگاری نداشته باشند و در چنین شرایطی بهتر است که هر کدام در مخازن جداگانه نگه داری و با فاصله زمانی مناسب به مخلوط کن بتن افزوده شوند. باتوجه به اینکه افزودنی ها معمولاً در مقادیر بسیار کم و براساس نسبت های کوچک به سیمان مصرف می شوند، باید از ابزار و تجهیزات اندازه گیری دقیق برای پیمانه کردن آنها در کارگاه استفاده شود و در کنار آن آموزش های لازم در مورد حساسیت و تاثیرات نامطلوب احتمالی ناشی از مصارف نادرست به کاربران داده شود.
رعایت دقیق دستورالعمل های شرکت های تولید کننده افزودنی کندگیر کننده و دقت در اندازه گیری مقادیر مصرفی از اهمیت زیادی برخوردار است زیرا همواره خطر عدم گیرش (ناگیرشدن) ناشی از مصرف بیش از اندازه افزودنی های کندگیر کننده وجود دارد. در این راستا، آموزش کاربران و آگاه کردن آنان در مورد حساسیت و اثرات منفی احتمالی ناشی از مصارف نادرست و خطاهای پیمانه کردن افزودنی کُندگیر کننده الزامی و بسیار سودمند خواهد بود. اگرچه به کاربردن بتن دیرگیر شده و باقیمانده از نوبت کاری قبلی به تنهایی مشکل فنی ندارد، ولی از آنجا که به دلیل مشغله های ابتدای نوبت کاری جدید معمولاً کنترل عوامل تاثیرگذار اندکی دشوار است، بهتر است بتن باقیمانده از قبل را با بتن تولید شده در نوبت کاری جدید در آمیخت و به کار برد.
نکته: برخی از کُندگیر کننده ها (به ویژه گروه قندها، شکر و ملاس چغندر یا نیشکر) رفتاری غیر خطی دارند یعنی تناسبی بین مقدار مصرف آنها و میزان کُندگیری که ایجاد می کنند وجود ندارد. به بیان دیگر محدوده مصرفی آنها که می تواند منجر به ناگیرکنندگی شود بسیار حساس است و گاهی در محدوده ی خطای دستگاه های اندازه گیری افزودنی ها در مراکز تولید بتن قرار دارد. بنابراین بهتر است برای بتن ریزی با قالب لغزنده لغزنده از این نوع کُندگیر کننده ها استفاده نشود.
در نوسان زیاد دما (مانند اختلاف دمای بین روز و شب در مناطق کویری) برای بتن ریزی به روش قالب لغزنده مقدار تاخیر مورد نیاز در گیرش بتن در ساعات مختلف شبانه روز یا در روزهای مختلف یکسان نخواهد بود و بهتر است که برای تنظیم زمان گیرش بتن در ساعت های مختلف از کُندگیر کننده های مستقل استفاده شود تا با تنظیم مقدار مصرف آنها به زمان گیرش مورد نظر دست یافت.
ارزیابی و انتخاب کُندگیر کننده
برای ارزیابی و انتخاب افزودنی کُندگیر کننده، لازم است موارد زیر نیز در نظر گرفته شوند. با اینکه کاربرد موفقیت آمیز یک افزودنی کُندگیر کننده در کارها و پروژه های قبلی می تواند راهشگای استفاده از آن در پروژه های با شرایط کاری و مصالح مصرفی همسان (مشابه) باشد، ولی از آنجا که کُندگیر کننده ها نسبت به سازندها و ترکیبات شیمیایی سیمان بسیار حساس هستند لازم است که یک افزودنی کُدگیر کننده با همان سیمانی که در کارگاه مصرف می شود مورد ارزیابی قرار گیرد.
تاخیری که در اثر مصرف کندگیر کننده در گیرش بتن بوجود می آید، موجب آرامش در روند کسب مقاومت اولیه می شود. بتن هایی که به آرامی کسب مقاومت اولیه می کنند عموماً دارای مقاومت های دراز مدت بیشتری هستند.
نکته: برای تعیین میزان اثرگذاری یا مقایسه عملکردی بین کُندگیرهای گوناگون از آزمون تعیین گیرش بتن، مانند ASTM C403 یا آزمون های مشابه استفاده شود و از به کارگیری آزمون هایی که برای تعیین زمان گیرش خمیر سیمان به کار می آیند (مانند آزمون ویکات) پرهیز شود. زیرا به دلیل تفاوت غلظت یون ها در خمیر سیمان و بتن، به کاربردن آزمون هایی که برای تعیین زمان گیرش خمیر سیمان به کار می روند (مانند ویک��ت) برای ارزیابی و مقایسه کُندگیر کننده های مختلف به نتایج گمراه کننده می انجامد.
کنترل کیفیت یکنواختی و ثابت بودن یک افزودنی در مراحل مختلف پروژه و ارسال های متعدد به کارگاه بایستی کنترل شود و برابری آن با آزمایش های اولیه به اثبات برسد. آزمون های لازم برای شناسایی و تایید افزودنی ها شامل: تعیین درصد مواد جامد، غلظت ظاهری، طیف سنجی برای مواد آلی، مقدار کلرید، درجه قلیایی (pH) و برخی موارد دیگر می باشند.
چگالی افزودنی های ارسالی مایع یا آن هایی که در کارگاه به مایع تبدیل شده اند باید براساس معیار و استانداردی که تولید کننده معرفی می کند سنجیده و با آن مقایسه شود. برای این منظور می توان به سهولت و با استفاده از وسایلی چون مایع سنج یا چگالی سنج، درصد جامد و غلظت مناسب آن را بررسی نمود. این عمل باید در دمای استاندارد انجام و نتایج آن به عنوان بخشی از کنترل کیفیت ثبت و نگه داری شود. معمولاً با کنترل رنگ، بود، شکل ظاهری و اندازه گیری غلظت و مقدار pH می توان یکنواختی محموله های مختلف افزودنی های وارده به کارگاه را تایید یا رد کرد.