دلایل وابسته به زمان بودن خصوصیات، صرف نظر از نوع الیاف موجود، به دو گروه عمده تقسیم می شوند. گروه اول، خوردگی الیاف می باشد. ماهیت اغلب سیمان های هیدرولیکی، قلیایی است. حین فرآیند ساخت، ترکیبات فلز قلیایی موجود به عنوان ناخالصی ها در رس ها استفاده شده به عنوان مواد خام، از طریق دماهای بالای تولید کلینکر، به اکسیدهای قلیایی و یا سولفات ها تبدیل می شوند که در داخل ساختار کلینکر سیمان موجود می باشند. با افزودن آب حین اختلاط بتن الیافی، این مواد قلیایی بسیار محلول، در آب اختلاط رها شده و pH را به شدت افزایش می دهند. با سخت شدن سیمان، آب اختلاط مصرف شده و در نتیجه غلظت مواد قلیایی در آب آزاد باقیمانده که در داخل حفرات موئینه خمیر سیمان وجود داشته و محلول حفره ای نامیده می شود، بالا می رود. محلول حفره ای سیمان می تواند به pH تا 7/13یا mmol/l (OH-) 700 برسد که مقدار OH- اساسا با یون های K+ و نیز با یون های Na+ مرتبط می باشد. محلول حفره ای توسط Ca(OH)2 (پرتلندیت) تولید شده توسط سیمان هیدراته شوند، میانگیری می شود، اما برخلاف آنچه معمولا تصور می شود، مقدار Ca2+ در محلول حفره ای عموما بسیار کم می باشد (یعنی <40mmol/l) که این امر از اثر یون مشترک ناشی می شود (برای جزئیات بیشتر درباره ساختار شیمیایی سیمان، برای نمونه مراجعه کنید به تیلور، 1997). سلامت بسیاری از الیاف، در این سطح بالای شرایط قلیایی مورد تهدید قرار می گیرد و در نتیجه خوردگی الیاف که منجر به افت مقاومت مسلح سازی می گردد، همواره یک مکانیزم تخریب ترکیبی است که باید مورد بررسی قرار گیرد.
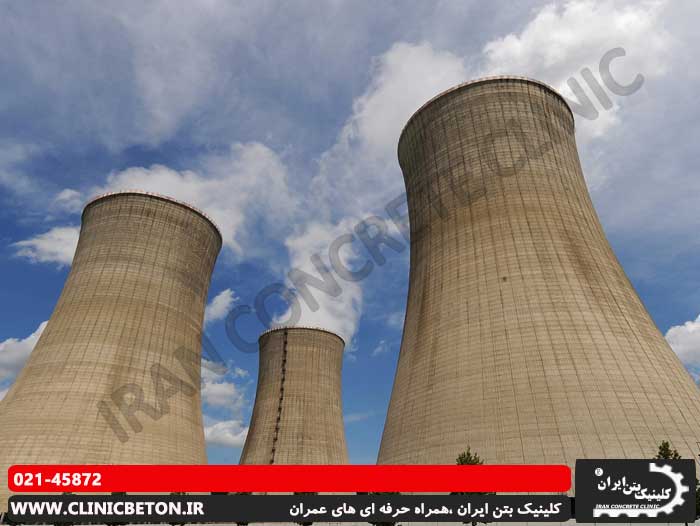
بتن های الیافی جایگذین میلگرد
این موضوع حتی برای الیافی که احتمالا در برابر حمله قلیایی ایمن هستند نیز باید مورد توجه قرار گیرد، زیرا مقیاس های زمانی که باید در نظر گرفته شوند –یعنی طول عمرهای بهره برداری اعضای معمول frc که اغلب چند دهه می باشد- بسیار طولانی تر از دوره های قرارگیری در معرض شرایط محیطی آزمایشگاهی خواهند بود. ضعیف شدن الیاف، علاوه برکاهش مقاومت مسلح سازی اولیه، ممکن است ایجاد تغییری در حالت گسیختگی را نیز منجر شود. با کاهش مقاومت الیاف، lC نیز کاهش می یابد و در نتیجه گسیختگی ممکن است از حالت بیرون کشیده شدن الیاف به پاره شدن الیاف تغییر یابد، یعنی رفتار ناحیه IV (شکل 9-2) ممکن است کاهش یافته و یا حذف گردد. برای الیاف فولادی، محیط قلیایی، لایه محافظی بر روی فولاد تشکیل داده و آن را از خوردگی حفظ می نماید، مانند حالت مربوط به بتن مسلح معمولی که در جای دیگری در این کتاب تشریح گردید. شواهدی نیز وجود دارد که برخی الیاف، خصوصا شیشه، ممکن است بر اثر تماس مستقیم با هیدروکسید کلسیم در خمیر، در معرض حمله فیزیکی- شیمیایی قرار گیرند که شدت آن بیشتر از حمله عامل قلیایی به تنهایی می باشد.
در برخی کاربردها، ورود عامل خارجی زیان آور برای برخی الیاف، مانند کلریدها یا مواد آلی اسیدی، باید مورد بررسی قرار گیرد. علی رغم آنکه این موضوع برای frc فولادی از درجه اول اهمیت برخوردار می باشد (مثلا کلریدها لایه محافظ بر روی الیاف فولادی را همانند فولاد در بتن مسلح، تخریب می کنند)، اما برای انواع دیگر frc، این موضوع چندان دارای اهمیت نخواهد بود. Frc ساخته شده با الیاف طبیعی که خصوصیات آن با میزان رطوبت تغییر می کند، ممکن است بر اثر نفوذ آب دچار تخریب گردد.
انواع مختلفی از اثرات ناشی از ادامه هیدراسیون خمیر سیمانی نیز می تواند موجب تخریب ترکیب ساخته شده گردد. با فرض حضور مداوم آب، سیمان هیدراته نشده باقیمانده در خمیر (که همواره مقدار آن کم می باشد) به هیدراته شدن ادامه داده و محصولات هیدراسیون بیشتری تولید نموده و مقاومت خمیر را افزایش می دهد. خود ساختار فاز هیدراته نیز به آهستگی تغییر می کند، زیرا این ساختار ماهیتا از فازهای نیمه پایدار تشکیل شده است. اگرچه این ادامه تکامل هیدراسیون ممکن است تنها برای بخش کمی از خمیر سیمان اتفاق بیفتد، اما اثرات برآیند بر روی اندرکنش های الیاف- خمیر می تواند عمیق باشد.
از رابطه (9-2) می توان دریافت که Vfcrit به مقاومت خمیر وابسته می باشد، به طوری که با محکم تر شدن خمیر، لازم است که نسبت بیشتری از الیاف، بار اعمال شده به آنها را هنگام آغاز ترک خوردگی خمیر گرفته و در نتیجه تنش را به الیاف منتقل نمایند. بنابراین برای ترکیباتی که با یک مقدار الیاف بسیار نزدیک به Vfcrit طراحی می شوند، تقویت بیشتر خمیر ممکن است رفتار ترکیب را در ترک اول از حالت نرم به ترد (شکننده) تغییر دهد، به گونه ای که نواحی II و III منحنی تنش- کرنش (شکل 9-2) قابل تشخیص نخواهند بود. اگر l>>lC باشد، آنگاه ناحیه IV نیز ممکن است حذف گردد. طراحی ترکیب باید به گونه ای دقیق انجام شود که از ایجاد این شرایط، جلوگیری نماید.
ادامه هیدراسیون نیز موجب «تراکم» ناحیه مشترک بین الیاف و خمیر می گردد. هنگامی که در ابتدا frc ساخته می شود، این ناحیه مشترک نسبتا متخلخل بوده و تماس نزدیکی را میان الیاف و خمیر برقرار نمی سازد. بنابراین ناحیه انتقال نسبتا ضعیف می باشد که این شرایط اغلب به چند دلیل به نفع ترکیب می باشد. در سنین اولیه، ترک های منتشر شونده در داخل خمیر، در این ناحیه ضعیف منحرف می شوند. با بیشتر شدن سن خمیر، محصولات هیدراسیون (خصوصا پرتلندیت) فضاهای موجود در ناحیه میانی ��ا پر کرده و تخلخل ر کاهش داده و سختی و ماومت را افزایش می دهند؛ به این ترتیب احتمال عبور یک ترک از میان الیاف نسبت به عبور از اطراف آن، از نظر آماری بیشتر می شود. این شرایط، موجب کاهش طاقت مصالح می گردد. همچنین الیافی که در عرض ترک ها قرار می گیرند (بر روی ترک ها پل می زنند)، بر اثر مسیر غیرمستقیم ترک ها، تمایل به خم شدن داشته و الیاف عموما با محور تنش همتراز نمی شوند. با سخت شدن خمیر، شعاع های انحنای الیاف کوچک تر می شود، زیرا خمیر در مجاورت نزدیک نقطه ای که یک رشته الیاف از سطح ترک خارج می شود، دارای سازگاری کمتری می باشد. این حالت موجب ایجاد تنش بیشتری در الیاف شده و احتمال شکستن آنها را افزایش می دهد. پیوستگی میان یک رشته یا دسته رشته نیز با متراکم شدن ناحیه میانی، افزایش می یابد. با افزایش تنش پیوستگی، lC کاهش می یابد. احتمال گسیختگی الیاف نسبت به بیرون کشیده شدن آنها افزایش یافته، رفتار ناحیه IV (شکل 9-2) توسعه نیافته و طاقت کاهش می یابد (هر چند که مقاومت کششی/ خمشی ممکن است به دلیل افزایش l/lC و در نتیجه n، به میزان قابل ملاحظه ای افزایش یابد).
یک پدیده مرتبط، «پرشدن دسته ها» می باشد. در frc با سن پایین مسلح به استرندها یا دسته رشته ها، معمولا فضایی بین رشته های مجزا وجود دارد که خمیر به داخل آن نفوذ نکرده است. بنابراین مصالح مسلح سازی می تواند مانند یک طناب رفتار نماید که در آن رشته ها بر روی یکدیگر حرکت کرده و طاقت پس از نقطه اوج ترکیب را به میزان قابل ملاحظه ای افزایش می دهند. با افزایش سن ترکیب، ادامه هیدراسیون و مهاجرت گونه ها در داخل خمیر سیمان منجر به ته نشینی محصولات هیدراسیون، خصوصا پرتلندیت، بین رشته ها شده و در نهایت کلیه فضاهای موجود پر می شوند. رفتار شبیه طناب از بین رفته و طاقت ترکیب ممکن است رو به کاهش گذارد.
اهمیت نسبی هر یک از این مکانیزم های تخریب، به ترکیب بخصوص الیاف- خمیر بستگی دارد. برخی ترکیب ها به ویژه نسبت به مکانیزم های خاصی، آسیب پذیر هستند، درحالی که در برخی دیگر، مکانیزم غالب همین موضوع مورد بحث و تحقیق می باشد. مکانیزم های مربوط به تغییر ریزساختار frc و مدلسازی تخریب، با جزئیات بیشتری در مقالات وب سایت رسمی کلینیک بتن ایران مورد بررسی قرار گرفته اند.
دوام الیاف ها
پیش از بحث پیرامون راهکارهای بهبود دوام frc، لازم است که روش هایی که توسط آنها داده های مربوطه به دست آمده اند، مشخص گردند. از آنجا که frc ماده نسبتا جدیدی است، مجموعه داده های هوازدگی «جاری» در زمان انجام فعالیت های مربوط به بهبود دوام frc موجود نمی باشد، به گونه ای که هنوز برای هوازدگی طبیعی بلند مدت، داده های کافی وجود ندارد. با پیشرفت ضوابط جدید برای دوام، روش های سالخوردگی تسریع شده برای بررسی پیشرفت های مورد نظر به کار گرفته شدند و امروزه این روش ها هنوز دارای کاربرد گسترده ای می باشند. دو نوع فنی از آزمایشات وجود دارد که عبارتند از سالخوردگی پیوسته و سالخوردگی چرخه ای. هدف از نوع اول تسریع تخریب از طریق غرقاب نمودن نمونه های ترکیب در آب در دمای بالا (عموما C°50≤) و در نتیجه تسریع دمایی واکنش الیاف- خمیر و یا از طریق محلول های مهاجم (یعنی محلول های آب دریا و نمک های یخ زدا) می باشد که در آن انتشار یون ها به داخل ترکیب از طریق افزایش گرادیان غلظت تسریع می گردد. محلول های مهاجم پرحرارت نیز گاهی برای آزمایشات حدی استفاده می شوند.
آب داغ به دو دلیل استفاده می شود: اول آنکه آب داغ یک انرژی حرارتی را تامین نموده و بسیاری از frcها نیز تنها بر اثر حرارت بالای «خشک» دچار آسیب نمی شوند. دوم آنکه grc نگهداری شده در محیط داخلی دچار هیچگونه آسیبی نمی گردد. به نظر می رسد که مکانیزم تخریب به نحوی شامل آب می شود که ممکن است شیمیایی یا فیزیکی باشد. محلول های مهاجم، عموما شامل یون های کلرید، معمولا تنها در مطالعات frc فولادی استفاده می شوند. آب داغ نیز برای frc شیشه و دیگر انواع مورد استفاده قرار می گیرد. آزمایشات چرخه ای (دوره ای) اصولا چرخه هایی از دما و یا رطوبت را تکرار می کنند که اعضای frc ممکن است در مدت بهره برداری در معرض آنها قرار گیرند. این آزمایشات چرخه ای معمولا شامل قرارگیری متناوب و تکرار شونده در معرض محیط های گرم، مرطوب، خنک و خشک و یا چرخه های یخ زدن- ذوب شدن می باشند. برای frc فولادی، قرارگیری در معرض پاشش و ترشح نمک ها جهت شبیه سازی مثلا ناحیه جزر و مدی محیط دریایی نیز استفاده می شود.
باید توجه نمود که این آژمایشات قابل استفاده به جای یکدیگر نیستند؛ یعنی برخی آزمایشات برای برخی فرمول های frc مناسب تر می باشند، مثلا آب گرم برای frc شیشه و تر و خشک شدن چرخه ای برای frc طبیعی همچنین برای سالخوردگی بتن مسلح به الیاف سلولزی، توجه به این نکته مهم است که حداقل یکی از گام ها باید کربناسیون خمیر را تسریع نماید. سالخوردگی frc فولادی تقریبا همیشه شامل نمک ها می باشد.
آزمایشات را نیز می توان به دو گروه تقسیم نمود: آزمایشات «تاییدی فرضی» (DS) و آزمایشات پیشگویانه هدف از آزمایشات DS به عنوان ابزار کنترل کیفیت استفاده می شوند، یعنی مثلا اگر نمونه ای از ترکیب پس از یک دوره ثابت یا چند چرخه سالخوردگی آزمایش شود و مشخص گردد که برخی خصوصیات آن بیشتر از برخی مقادیر یا درصدهای از پیش تعیین شده می باشد، آنگاه ترکیب «قابل قبول» بوده و مصالح برای هدف مورد نظر مناسب خواهد بود. هیچگونه پیش بینی یا استنتاجی از رفتار بلندمدت ترکیب، در حال بهره برداری صورت نمی گیرد، تنها بیان می شود که مصالح «بادوام» است، زیرا آزمکایش مربوطه را با موفقیت گذرانده است. از سوی دیگر، در آزمایش پیشگویانه تلاش می شود که ارتباطی میان دوره ها یا تعداد چرخه های سالخوردگی تسریع شده با دوره های طولانی تر هوازدگی بهره برداری برقرار گردد و در نتیجه این روند به سمت تعیین طول عمر مورد انتظار مصالح به پیش می رود. اگر از نظر تئوری هر دو آزمایش چرخه ای و آب گرم می توانند در یک گروه قرار گیرند، اما در عمل سالخوردگی پیوسته به ویژه سالخوردگی با آب گرم می تواند برای آزمایش پیشگویانه و سالخوردگی چرخه ای برای آزمایش DS با چند استثنا مورد استفاده قرار گیرد.
پژوهشگران همچنین الیاف را (در مقابل کامپوزیت ها) در معرض رژیم های سالخوردگی تسریع شده قرار داده اند و رفتار احتمالی آنها در یک خمیر سیمانی را مورد بررسی قرار داده اند. این آزمایشات عموما شامل غرقاب نمودن نمونه های الیاف در محلول های قلیایی گرم، اغلب با ترکیبی مشابه محلول حفره ای سیمان، برای مدت زمان های متفاوت و اندازه گیری کاهش برآیند در مقاومت، می باشد. اینگونه آزمایشات اگرچه برای کمک به ارزیابی الیاف جدید سودمند می باشند، اما باید از نظر استفاده آنها در پیش بینی دوام، با احتیاط مورد بحث قرار گیرند، زیرا اثر خمیر سیمان بر روی الیاف تنها توسط خاصیت قلیایی آن کنترل نمی شود. نشان داده شده است که الیاف سیزال و نارگیل پس از 300 روز در محلول Ca(OH)2 با pH برابر 12، مقاومت خود را به طور کامل از دست می دهند.
الیاف آرامید (توارون) برای مدت 24 ساعت در شرایط غرقاب در NaOH در شرایط تحت تنش و بدون تنش قرار داده شده اند و هیچگونه اثر نامطلوبی بر روی آنها مشاهده نشده است، اما داده هایی برای طول مدت بیشتر در اختیار نمی باشد. چنین آزمایشاتی مدت ها با ترکیبات گوناگون احتمالی شیشه استفاده شده اند و نتایج حاصله توسط ماجومدار و لاز مورد بررسی و مرور قرار گرفته است، اما فرمول های جدید سرامیک و شیشه هم اکنون در نمونه های واقعی frc در حال آزمایش می باشند، اگر چه در برخی کارهای بنیادی همچنان فقط از الیاف استفاده می شود.
شناخته شده ترین اصل سالخوردگی تسریع شده برای frc (که اغلب به طور نادرست مورد استفاده قرار گرفته است) احتمالا مورد مربوط به grc نوع AR-glass با خمیر OPC می باشد که توسط پراکتور و همکاران در اواخر دهه 1970 ارائه شده است. ترکیبی از آزمایشات بر روی ترکیبات سالخورده بر اثر غرقاب در آب گرم، و ترکیبات قرار گرفته در معرض محل های مختلف در دنیا، با داده های حاصل از یک آزمایش دوام ویژه برای استرندهای الیافی تحت عنوان آزمایش «استرند در سیمان» (SIC) ترکیب گردید. آزمایش SIC شامل نمونه ای متشکل یک استرند از الیاف می باشد (برای grc، معمولا در حدود 200 رشته، هر یک به قطر µm14) که به طور جزئی در یک استوانه از خمیر سیمان قرار گرفته است. سالخوردگی در نمونه از طریق غرقاب نمودن در آب داغ برای یک مدت زمان مشخص ایجاد شده و پس از آن استرند به صورت کششی با استوانه کوچکی از خمیر که به صورت ثابت در جای خود قرار دارد، آزمایش می شود (شکل 9-5). این محققین نتیجه گرفتند که یک مکانیزم تخریب واحد با یک انرژی فعال سازی در حدود kj/mol90، افت مقاومت در کلیه این موارد را کنترل نموده است و داده ها وارد رابطه ای از نوع آرهنیوس شدند تا ارتباطی میان آزمایشات سالخوردگی تسریع شده با دوره های طولانی تر در هوازدگی حین بهره برداری به دست آید.
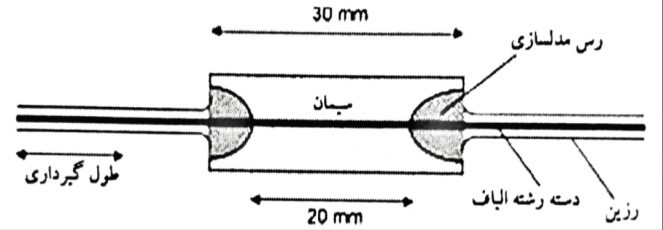
شکل 9-5- طرح نمونه آزمایش SIC
این کار منجر به تعیین «ضریب تسریع» گردید، مثلا یک روز سالخوردگی از طریق غرقاب نمودن در آب گرم در 50، 60 و C°80، همان افت مقاومت به ترتیب 101، 272 و 506 روز از هوازدگی در آب و هوایی شبیه انگلستان را موجب می گردد. این رابطه پیشگویانه سبب شد که سالخوردگی با آب گرم به عنوان روش استاندارد «ضریب دار» برای صحت سنجی فرمول های جدید grc در ارتباط با دوام باقیمانده، پذیرفته شود. با این وجود، این روش تنها برای ترکیبات OPC به طور ذهنی ایجاد شده است. نگرانی مربوط به استفاده از آن توسط محققین دیگر برای grc غیر استاندارد (و حتی frp) با ویژگی ها و مکانیزم های سالخوردگی کاملا متفاوت به همراه کاستی های مدل مربوط به پیش بینی عمر بهره برداری و عدم وجود یک مدل میکرومکانیکی، سبب گردید تا این رابطه توسط پرنل و همکارانش به روز گردد. مبنا و ویژگی های این مدل با جزئیات بیشتری در مقالات قبلی وب سایت رسمی مهندسین مشاور مهرازان پایدار تشریح شده است، اما روشن است که یک مجموعه منحصر به فرد از ضرایب تسریع، به هر دو فرمول خمیر استفاده شده با شیشه AR اعمال می گردد، در حالی که اصولا ضرایب تسریع به دست آمده برای grc نباید به طور خودکار به انواع دیگر frc اعمال شوند.
یک روش آزمایش پذیرفته شده دیگر برای سالخوردگی تسریع شده برای grc در استاندارد اروپا، DDEN 1170-8:1997 محصولات بتنی پیش ساخته، تحت عنوان روش آزمایش سیمان مسلح به الیاف شیشه، آزمایش نوع هوازدگی چرخه ای، ارائه گردیده است. این روش شامل سالخوردگی چرخه ای است که در آن هر چرخه شامل غرقاب شدن 24 ساعته در آب C°20، 30 دقیقه خشک شدن در هوا در C°70 و جریان هوای با سرعت ms-11، 23 ساعت در هوا در C°70 و 30 دقیقه سرد شدن در هوا در C°20 و جریان هوای با سرعت ms-11 و آزمایش خمشی نمونه ها پس از 10، 25 و 50 چرخه می باشد. انجام این آزمایش دشوار می باشد، زیرا مستلزم تجهیزات ویژه بوده و هیچگونه پیش بینی را شامل نمی شود و تنها می تواند جهت مقایسه استفاده شود. بنابراین، مورد توجه محققین نمی باشد. اما در صنعت دارای طرفدارانی می باشد.
سالخوردگی تسریع شده frc برپایه الیاف سلولزی و یا طبیعی نیز تا حدی مورد توجه قرار گرفته است. در ابتدا، اصول ارائه شده برای سالخوردگی با آب گرم توسط پراکتور و همکارانش برای frc شیشه، برای frc سیزال مورد استفاده قرار گرفت، اما نامناسب بودن آن مشخص گردید. پس از آن بنتور و آکرز روش هایی را برای سالخوردگی تسریع شده frc سلولزی در یک سری از مقالات منتشر نمودند. دو رژیم چرخه ای با طول چرخه 24 ساعته پیشنهاد گردید؛ دمای محیطی/ دمای بالا (AE) و دمای بالا/ اشباع با (CE) CO2، که پس از آنها آزمایش خمش سه نقطه ای براساس ISO 39611-1980E انجام می شود. چرخه AE عبارت بود از 9 ساعت در آب با دمای C°20، 3 ساعت در هوا با دمای C°20، 9 ساعت در معرض تابش اشعه مادون قرمز با دمای C°80 در هوا، و 3 ساعت سرد شدن در هوا با دمای C°20. این چرخه ها به مدت 3 ماه ادامه یافت. چرخه CE دارای بهترین و نزدیک ترین تقریب برای یک دوره 5 ساله هوازدگی طبیعی بوده و درنتیجه مناسب ترین روش شناخته شد. استفاده از این روند برای سالخوردگی FRC سلولزی نیز ادامه دارد، هرچند دیگر محققین از آزمایشات کربناسیون کمی اصلاح شده، علاوه بر روش های یخ زدن- ذوب شدن استفاده می کنند. کلیه محققین به نتایج نسبتا یکسانی دست یافته اند و آن اینکه مقاومت و مدول مصالح در حدود 20 تا 50 درصد افزایش می یابد (در نتیجه کربناسیون خمیر، مقاومت و احتمالا پیوستگی خمیر افزایش می یابد)، اما کرنش گسیختگی تا مقادیری مشابه خمیر غیر مسلح یعنی %1/0> کاهش می یابد. روند مشابهی برای FRC نوع PVA نیز استفاده شده است، اما این کار باز هم با یک Vf بسیار پایین صورت گرفته است. برخی از آزمایشات برای کاربردهای ویژه نیز استفاده شده است. FRC سلولزی برای لوله های فاضلاب استفاده می شود (کاربردی که در آن قبلا از FRC آزبستی استفاده می شد) و بنابراین در معرض عوامل مضر خارجی قرار دارد که می توانند موجب حمله اسیدی و یا بیولوژیکی به الیاف و یا خمیر گردند. فیشر و همکاران نمونه هایی ااز FRC سلولزی را در معرض تصفیه خانه های فاضلاب هوازی و بی هوازی قرار داده و نیز نمونه هایی را در اسید سولفوریک (5~ pH) غرقاب نمودند. اینگونه نتیجه گردید که ممکن است مزایایی در استفاده از FRC سلولزی نسبت به FRC فولادی در این کاربردها وجود داشته باشد. برای FRC با الیاف طبیعی، چرخه های تر و خشک شدن معمولی (مثلا 1 روز غرقاب نمودن در دمای اتاق و پس از آن 6 روز خشک کردن در شرایط محیطی آزمایشگاه) مناسب به نظر می رسد، هر چند از آنجا که چنین ترکیباتی تحت هوازدگی عادی در زمان نسبتا کوتاه دچار آسیب و کاهش کیفیت خصوصیات می شوند، جای بحث وجود دارد که آیا سالخوردگی تسریع شده ضروری می باشد.
از آنجا که ورود نمک های مهاجم به جای اندرکنش های الیاف خمیر، عامل کنترل کننده می باشد، آزمایشات مورد استفاده برای FRC فولادی نیازمند تمرکز متفاوتی نسبت به انواع دیگر FRC می باشند و عملکرد آن اغلب با RC مقایسه می شود. به نظر می رسد که دوام در ناحیه جزر و مدی (تلاطم و پاشش) آب از سازه های دریایی، توجه بسیاری را به خود جلب نموده است، چرا که این حالت شدیدترین محیط ممکن فرض شده و در آزمایشات تلاش می شود که این محیط شبیه سازی گردد. چرخه های تر و خشک شدن با استفاده از محلول NaCl 5/3% در 20، 50 و 80 درجه سانتیگراد تا مدت زمان 10 ماه به همراه افزایش کربناسیون و یا بدون آن، آسیب قابل ملاحظه ای را به FRC فولادی وارد می نماید. مقاومت و طاقت برای نمونه های کربناته شده پیش از قرارگیری در معرض این محیط، به ترتیب 20% و 60% کاهش می یابند. تنها طاقت به میزان قابل ملاحظه ای در نمونه های کربناته نشده تا حدود 35% کاهش می یابد. مگنات و گوروسامی یک اتاقک پاشش دریای آزمایشگاهی را با محیط جزر و مدی طبیعی مقایسه کرده و نشان دادند که از نظر ورود کلرید به داخل بتن، اتاقک به دلیل مقدار زیاد نمک، حدود 10 برابر خورنده تر از محیط طبیعی بوده است. محققین اخیرا از طول مدت یکساله با چرخه های دو هفته ای، یک هفته با «مه نمک» NaCl با غلظت g/l5/3 و یک هفته «خشک شدن» و یا تا 1500 چرخه یخ زدن- ذوب شدن در آب شیرین یا محلول نمک NaCl با غلظت g/l5/3 مطابق با ASTM C666A استفاده نموده اند.
پربازدیدترین مطالب ما را از دست ندهید!
برای بررسی سالخوردگی تسریع شده انواع دیگر FRC با انواع مختلف روش های ابتکاری و غیر استاندارد (ad hoc) موجود در مراجع، به نظر نمی رسد که تا این اندازه سرمایه گذاری شده باشد. FRC پلی پروپیلن با استفاده از 50 چرخه تر و خشک شدن و به دنبال آن آزمایش ضربه ای، و 50 چرخه یخ زدن- ذوب شدن و به دنبال آن آزمایش خمشی/ فاشری، مورد بررسی قرار گرفت، که کاهش مقاومت خمشی و عدم تغییر مقاومت فشاری مشاهده گردید. اخیرا بتن مسلح به الیاف سرامیکی برپایه Al2O3، از طریق غرقاب نمودن در دمای C°70 مورد بررسی قرار گرفته است. FRC کربن نیز در معرض سالخوردگی ناشی از یخ زدن- ذوب شدن (براساس ASTM C666) برای حاست بین 30 چرخه و 300 چرخه و غرقاب نمودن در دمای C°75 برای مدت 5 ماه قرار گرفته و تاثیر اندکی (در صورت وجود) بر روی مقاومت مشاهده گردیده است. بنتور و میندس علت آنکه FRC کربن هیچگونه پاسخ بلندمدتی را نسبت به سالخوردگی تسریع شده چرخه ای و آب گرم نشان نمی دهد، بررسی نموده و نتیجه گرفتند که این نوع FRC احتمالا دچار مشکلات دوامی نخواهد شد.