کاهنده های آب در بازه بالا
فوق روان کننده های بتن در عملکرد افزودنی های سنتی تغییرات قابل ملاحظه ای را به وجود می آورند. مواد شیمیایی که به عنوان فوق روان کننده مورد استفاده قرار می گیرند بر کشش سطحی آب در اختلاط بتن اثر نمی گذارد، در نتیجه می توان مقادیر بیشتری از آنها را بدون حضور اثرات جانبی نامطلوب (هوای محبوس، جدایش و کندی گیرش) مورد استفاده قرار داد. زمان پیدایش فوق روان کننده ها در اوایل دهه 1970 بود و اکنون فوق روان کننده های بتن به نسل سوم خود تکامل پیدا کرده اند، طوری که ساختار مولکولی آنها بر محدودیت های پیشین که با کارکرد فوق روان کننده ها در ارتباط بود، غلبه کرده است. این سه نسل فوق روان کننده ها را می توان به صورت زیر طبقه بندی نمود.
نسل اول فوق روان کننده ها اصالتا مواد آنیونی هستند. آنها بارهای منفی را بر ذرات سیمان ایجاد می کنند و موجب می شوند تا آنها یکدیگر را دفع نمایند. به این ترتیب اصطکاک سطحی کاهش می یابد. این نسل تقریبا بر فرآیند هیدراتاسیون بی اثر هستند. به علت مدت کوتاه کارایی ایجاد شده، نسل اول فوق روان کننده ها عموما در محل کارگاه (پروژه) اضافه می شوند. نسل دوم فوق روان کننده ها روی ذرات سیمان بیشتر جذب می شوند. این کار نه تنها شکل پذیری روی خمیر سیمان می کند، بلکه نسبت آب به سیمان کمی را هم ممکن می سازد و فرآیند هیدراتاسیون را کنترل می کند. این کنترل هیدراتاسیون امکان می دهد که مواد نسل دوم در دماهای کمتر بتن به نسبت مواد نسل اول، استفاده شود. این نسخه های دیرگیرکننده مدت زمان کارایی را طولانی می نمایند و برخی مواد می تواند درکارخانه اضافه شود. مواد شیمیایی فوق روان کننده نسل سوم برای تاثیرات فضایی حلقه های جانبی شان انتخاب می شوند. آنها همچنین روی ذرات سیمان جذب می شوند اما اثرات خود را نه از طریق دفع الکترواستاتیکی، بلکه بیشتر از طریق مکانیسم ممانعت فضایی تامین کنند. چون این نسل یکنواختی های بیشتری را به مدت زمان های طولانی تر حفظ می نمایند، آنها را اغلب در کارخانه به ترکیب اضافه می کنند. بنابراین، اختلاف اساسی میان مواد نسل دوم و نسل سوم در این است که فوق روان کننده نسل سوم می تواند پیوستگی های گیرش اولیه را شبیه به بتن معمولی حفظ کند در حالی که اختلاطی با شکل پذیری بالا را در نسبت آب به سیمان خیلی پایین ایجاد می کند. دو کارکرد اصلی فوق روان کننده ها عبارتند از:
1- تولید بتن هایی با روانی خیلی بالا که در آنها افزودنی بدون هیچگونه تغییر در نسبت آب به سیمان به اختلاط اضافه می شوند تا اسلامپ هایی بیشتر از 180 mm تولید شود.
2- تولید بتن با نسبت های آب به سیمان پایین برای رسیدن به مقاومت های اولیه و نهایی بالا و کاهش بیشتر نفوذپذیری به رطوبت و نمک ها.
با پیدایش بتن با کارایی بالا و توسعه نسل سوم فوق روان کننده ها (اغلب با پایه پلیمری اکریلیک) ذکه به طور محسوسی کاهش آب بیشتری را در یکنواختی های قابل روانی فراهم می کند، اینگونه مرزبندی ها کم رنگ شده است. اگر چه با به کار بردن ترکیبی از افزودنی ها در حال حاضر امکان به دست آوردن بتن های با نسبت آب به سیمان و بادوام بالا که خود تراز شونده و در عین حال کاملا چسبنده هستند، عملی شده است.
بتن روان
اختلاط های بتنی استاندارد دارای چسبندگی خوب و اسلامپ بیش از mm180 به عنوان بتن روان طبقه بندی می شوند. شکل 7-16 شبه سیالی را نشان می دهد که با اضافه شدن یک فوق روان کننده به اسلامپ mm75-50 (a) دست می یابد. ویژگی های بی نظیر بتن روان، که در آن کارایی بالا و چسبندگی زیاد هر دو وجود دارند، این امکان را می دهد که درشتدانه ها به صورت متوازن در تمام ارتفاع بتن ریزی شده توزیع گردند. این امر به وضوح در مغزه های نشان داده شده در شکل 7-17 نشان داده شده است. نتایج پس از 3 سال از تاریخ بتن ریزی در شکل 7-18، و نتایج در جدول 7-13 ارائه شده است. مقاومت های فزآینده نشان داده شده برای مغزه های گرفته شده از دال های بتنی روان می تواند با فقدان فضاهای خالی مرتبط باشد (شکل 7-17، مغزه A). جنبه هایی از نسبت اختلاط که باید در طراحی مخلوط های با قبلیت روانی بالا در نظر گرفته شود عبارتند از: (1) میزان سیمان موجود؛ (2) میزان ریزدانه های موجود؛ (3) نوع فوق روان کننده؛ (4) حضور دیگر افزودنی ها در اختلاط؛ (5) نوع سیمان یا مواد سیمانی؛ (6) پیمانه مصرفی افزودنی؛ (7) ترتیب اضافه شدن؛ (8) خصوصیات درشت دانه. کنترل همه این متغیرها این تضمین را می دهد که بارگذاری های متوالی در ویژگی های مربوط به حمل کردن، بتن ریزی و عملیات تکمیلی، مشابه می باشند.
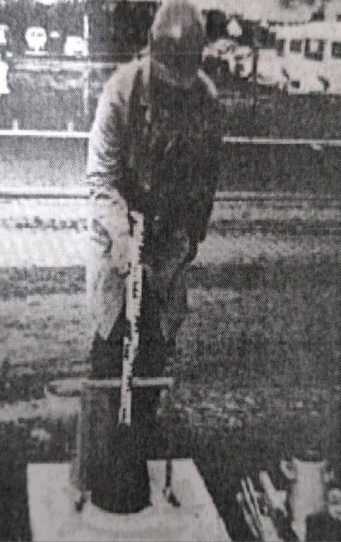 (b) | 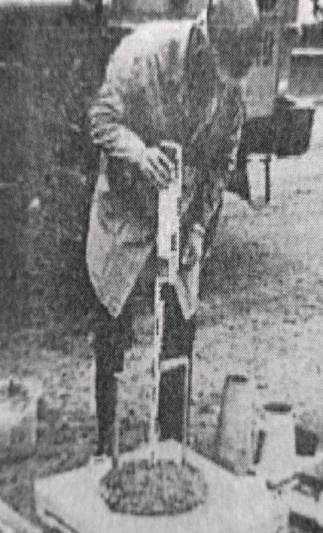 (a) |
شکل 7-16- (a) اسلامپ mm50 قبل از اضافه شدن یک فوق روان کننده، (b) اسلامپ فروریخته
بتن mm100 که عموما در بتن روان استفاده می شود.
شکل 7-17- مغزه های گرفته شده ز دال های بتنی 3 ساله با (A) بتن روان؛ (B) با اسلامپ mm50
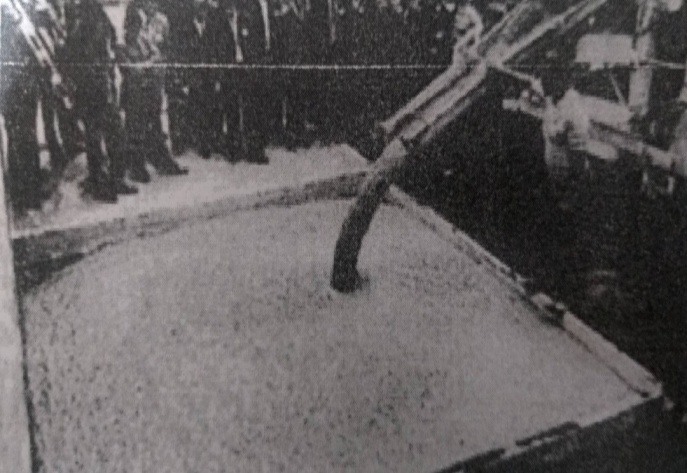
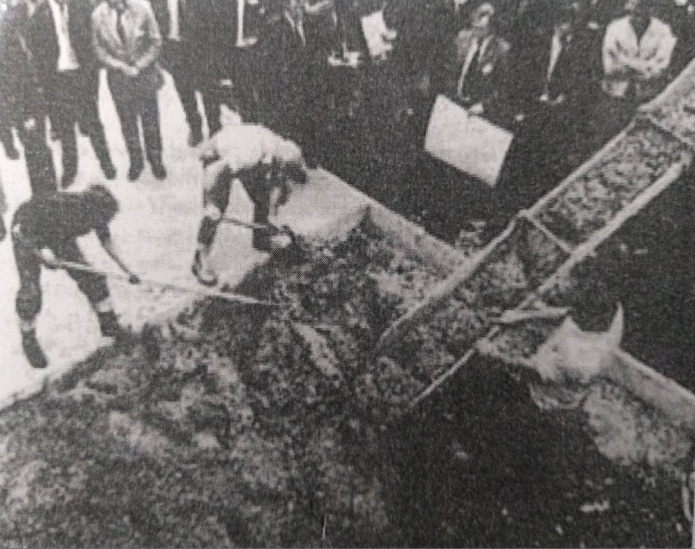
شکل 7-18- بتن ریزی دال ها (a) با استفاده از بتن روان و (b) با روش سنتی
جدول 7-13- ویژگی های مغزه های 3 ساله نشان داده شده در شکل 7-17
بتن با اسلامپ 50 میلیمتری دال ساخته شده از بتن روان |
خوب | خوب | بازدید چشمی |
ضعیف 1 – متوسط خوب | خوب | توزیع مواد |
کم | بدون فضای خالی | تراکم بتن |
قابل ملاحظه | قابل اغماض | فضای خالی (تخلخل) |
3.26 | 8.32 | زیاد |
0.33 | 8.40 | متوسط |
05.23 | 20.23 | کم |
| | نتایج آزمون |
| | مقاومت استوانه ای اصلاح شده |
| | مقاومت مکعبی تخمین زده شده |
| | چگالی (kg/m3) |
مقدار سیمان بهینه موجود که یکنواختی های روان را تامین می کند در بازه kg/m3 415 – 270. مقدار ذرات ریز موجود یک مخلوط برای ممانعت از آب انداختگی و جدایش مخلوط با اسلامپ بالا مهم است. با این وجود، کاربرد افزونی بهبود دهنده ویسکوزیته این امکان می دهد مخلوط های با روانی خیلی بالا چسبنده نگه داشته شود، اهمیت این پارامتر را نسبت به قبل کمتر ساخته است. کاربرد یک ترکیب از افزودنی ها در بتن روان، سازگاری افزودنی ها را یک الزام مهم همراه می سازد. بسیاری از افزودنی های بهبود بخش ویسکوزیته با فوق روان کننده ها برای محل های جذب روی ذرات سیمان رقابت می کنند و موجب می شود که فوق روان کننده اثر کمتری داشته باشد. این مورد بخصوص برای فوق روان کننده های نوع نفتالن فرمالدهید- سولفات صحیح می باشد. انواع جدیدتر فوق روان کننده ها اثرات خود را با یک مکانیسم فضایی ایجاد می کنند که قابلیت روانی بیشتری را حتی در نسبت های آب به سیمان پایین القاء می کند. در نتیجه مهم است که این اثر را هنگام استفاده از مواد سیمانی، سیمان های تیپ IV یا V، سرباره کوره آهن گدازی یا خاکستر بادی، که همگی آنها مستلزم دز افزودنی پایین تر برای ایجاد یک اسلامپ مشخص است، در نظر بگیریم. از این گذشته، به علت میزان ذرات جامد متغیر و بنابراین غلظت موثر در فوق روان کننده های اختصاصی مختلف، توجه خاصی باید به دز توصیه شده تولید کننده برای بتن روان صورت بگیرد. این فاکتور ثانوی در فوق روان کننده های نسل اول (انواع ملامین و نفتالن) به نسبت انواع با پایه پلیمراکریلیک جدیدتر که از طریق مکانیسم فضایی اجرا می شود و در نتیجه توسط منطقه های جذب کاهش یافته تحت تاثیر قرار نمی گیرد، بیشتر قابل اعمال می باشد. دمای بتن بالا، سیمان نرم با میزان C3A بالا، میزان سیمان موجود زیاد (kg/m3 415)، حضور یک افزودنی بهبود دهنده ویسکوزیته و اسلامپ های اولیه پایین مستلزم دزهای افزودنی بالاتر از پیمانه مصرفی توصیه شده استاندارد تولید کننده خواهد بود. حضور یک عامل هوازا، دیرگیر کننده یا کاهنده آب و کاربرد فوق روان کننده های از نوع اکریلیک اسلامپ بیشتری از افزایش اسلامپ پیش بینی شده به علت عمل فروپاشنده فزاینده دو افزودنی را ایجاد خواهد کرد. در نتیجه، آب انداختگی و جدایش در اختلاط های با میزان سیمان و ذرات ریز پایین تر رخ دهد.
بتن های آماده در بردارنده تاخیر میان مرحله اختلاط و بتن ریزی و افزوده شدن در محل کارگاه از فوق روان کننده های نسل اول و بعضی نسل دوم می باشد. در نتیجه، خصوصیات وابسته به زمان بتن شکل پذیر (مثل اسلامپ و زمان گیرش) و شیوه ای که افزودنی در مخلوط لحاظ می شود مستلزم کنترل مناسب است. برای بتنی که باید به فرم با کارایی بالا تولید شود، لازم است که حمل به کارگاه بتن ریزی با اسلامپ mm755 باشد و پیمانه مصرفی مناسب فوق روان کننده با استفاده از یک توزیع کننده مناسب اضافه شود. تعیین پیمانه مصرفی به صورت دستی در محل کارگاه، گاهی اوقات برای بتن مخلوط شده در کارخانه با فوق روان کننده های نسل اول و دوم استفاده می شود. پیمانه مصرفی فوق روان کننده ای که باید اضافه شود برای هر بارگذاری در کارخانه محاسبه می شود و در یک مخزن در کامیون میکسر حمل می شود. پیمانه مصرفی لازم از طریق یک لوله توسط نیروی گرانش به درون مخزن اختلاط ریخته می شود. این محاسبه عموما بر مبنای نمودارهای تهیه شده (پیش از بتن ریزی) برای پیمانه های مصرفی فوق روان کننده های مورد نیاز برای تولید بتن روان غیر جداشونده در اسلامپ های گوناگون می باشد. با این کار تنظیمات پیمانه مصرفی لازم به هنگامی که مشکلاتی در فراهم کردن اسلامپ لازم در محل کارگاه مواجه می شویم، به راحتی انجام می گیرد. این روش معمولا مستلزم کنترل کافی از یکنواختی است و وابسته به دوره های حداقل تاخیر می باشد. در نتیجه مستلزم زمان بندی دقیق می باشد. پس از اضافه شدن فوق روان کننده ها، اندازه گیری های اسلامپ ثبت می شود. در عین حال، با فوق روان کننده های نسل سوم از نوع اکریلیک استر، افزوده شدن آب اندازه گیری شده در کارخانه ترکیب بتن انجام می شود.
بسیاری از تولید کننده های بتن از ترکیبی از فوق روان کننده و یک کاهنده سنتی، اصلاح کننده گیرش یا افزودنی هوازا استفاده می کنند تا به عملکرد مطلوب دست یابند. فوق روان کننده سهم عمده از کاهش آب لازم را تامین می کند و با افزودنی سنتی به یک یا چند تا از اهداف زیر دست پیدا می کنیم: (1) کاهش آب بیشتر، (2) اقتصاد افزودنی، (3) میزان هوای موجود مطلوب، (4) کارایی افزایش یافته، (5) امتداد گیرش و کارایی.فرمولاسیون های افزودنی سنتی تجاری مورد استفاده برای این هدف معمولا بر مبنای سدیم لیگنوسولفونات ها، اسیدهای هیدروکسی کربوکسیلات یا کربو هیدرات های فرآوری شده می باشد. چنین ترکیباتی، در کنار کاهش پیمانه مصرفی روان کننده مورد نیاز، ظاهرا کارایی اختلاط را با کاستن چسبندگی از اختلاط در برخی مخلوط ها را بهبود می بخشد. اخیرا، پروژه های زمینی با استفاده از فوق روان کننده ها بر مبنای استرهای اکریلیک نشان داده است که روانی مطلوب، امتداد کارایی (تا 1 ساعت)، اقتصاد افزودنی و کنترل کیفیت بیشتر می تواند با استفاده صرف از این افزودنی حاصل شود.
علیرغم انتشار وسیع اثرات نامطلوبی که باز خمیر سازی موجب می شود، بخصوص در شرایط با آب و هوای بسیار گرم افزودن آب اضافی در محل کارگاه برای جبران افت اسلامپ هنوز هم یک رویه اجرایی متداول است. تحت این شرایط، کاربرد هر دو افزودنی های سنتی و فوق روان ساز به حداقل کردن مقدار آب مورد نیاز برای باز خمیر سازی کمک می کند، لذا افت مقاومت حداقل می شود. این مورد هم در جدول 7-4 نشان داده می شود.
یکی از محدودیت های برجسته در به کارگیری فوق روان کننده های نسل اول و دوم در بتن روان آماده عبارت است از کاهش سریع در کارایی اولیه و همین امر یکی از موانع اصلی بر سر راه پذیرفته شدن وسیع تر این مواد را تشکیل می دهد. در نتیجه، شماری از تولید کنندگان عمده افزودنی ها از تحقیقات فعالانه به منظور ارتقاء خصوصیات مربوط به حفظ کارایی فوق روان کننده ها حمایت به عمل آورده اند. البته برخی از پیشرفت های اخیر امیدوار کننده نشان داده است، در میان اینها موادی هستند با پایه پلیمرهای اکریلاتی (AP). مواد با پایه AP ظاهرا موثرتر از فوق روان کننده های با پایه SMF یا SNF به لحاظ کاهش آب، افزایش اسلامپ و حفظ اسلامپ می باشند. شکل 7 – 19 بهبود جالب توجه در حفظ کارایی ایجاد شده توسط فوق روان کننده نوع AP در قیاس با نوع SNF را نشان می دهد.
از ویژگی های مهم این نوع افزودنی این است که چنین فایده هایی با اضافه شدن افزودنی به آب اندازه گیری شده (مثل افزودنی های سنتی و تا حد کمی مواد SNF،SMF) درک می شود، بنابراین این نوع افزودنی برخی مسائل که با فوق روان کننده های نسل اول و دوم گره خورده است را از میان بر می دارد. جدول 7-15 اثر زمان اضافه شدن را روی افزایش اسلامپ حاصل با سه نسل فوق روان کننده ها را ارائه می دهد. جالب توجه اینکه اضافه شدن فوری هیچ اثری بر اسلامپ حاصل شده نداشته است. مکانیسم فرو پاشاندن منتسب به نوع AP به اثر ممانعت فضایی بیشتر مربوط می شود تا دافعه الکترواستاتیک مرتبط با انواع SMF،SNF.
جدول 7 – 14 اثر افزودنی های کاهنده آب بر باز خمیر سازی
زمان (دقیقه) سیمان B |
126 120 10 |
(8/7 3) 98 62.0 (2/1 4) 114 58.0 (4/1 3) 95 56.0 (8/5 3) 92 | (2/1 1) 92 56.0 (8/5 1) 92 52.0 (2/1 1) 95 49.0 (8/3 1) 92 | (8/5 3) 92 56.0 (8/5 3) 92 52.0 (4/1 3) 95 49.0 (8/5 3) 92 | اسلامپ mm (in) w/c اسلامپ mm (in) w/c اسلامپ mm (in) w/c اسلامپ mm (in) w/c | مبنا لیگنو سولفونات اصلاح شده ٪18 اسید کربوکسیلیک هیدروکسیلاتی 75٪ فرمالدهید ملامین سولفوناتی 1٪ |
افزودنی های کاهنده آب، کاهش چشمگیر در کل آب را پس از باز خمیر سازی ممکن می سازد.
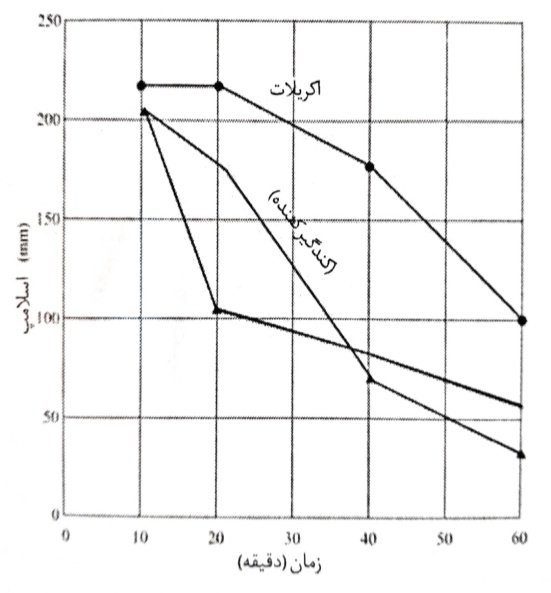
شکل 7 – 19 اثر فوق روان کننده روی اسلامپ بتن
جدول 7-15 اثر مود اضافه شدن فوق روان کننده های CAE، SMF، SNF روی اسلامپ مخلوط های
بتنی با سیمان پرتلند
اختلاط بتنی افزودنی |
اسلامپ (mm) | w/c | مود افزودنی | پیمانه مصرفی (٪) | نوع |
230 | 39.0 | بلافاصله | 30.0 | CAE |
235 | 39.0 | با تاخیر | 30.0 | CAE |
100 | 41.0 | بلافاصله | 50.0 | SMF |
215 | 41.0 | با تاخیر | 50.0 | SMF |
100 | 40.0 | بلافاصله | 48.0 | SNF |
230 | 40.0 | با تاخیر | 48.0 | SNF |
* فوری: افزودن با آب اختلاط. با تاخیر: افزودن پس از 1 دقیقه اختلاط
مواد متشکل از اجزاء لیگوسولفوناتی منتخب با وزن مولکولی بالا، کربوهیدرات موجود کم، موفق آمیز نشان داده و فروپاشنده های موثری با خصوصیات درگیر کنندگی قابل قبول می باشند. در دزهای مصرفی کم در قیاس با فرآورده هایی که بیشتر شناخته شده اند همچون ملامین و سولفونات های نفتالن، مواد تشکیل دهنده با توجه به حفظ کارایی عملکرد قابل مقایسه ای را ارائه می کنند. هوای محبوس تا حدی از کاربرد این مواد نتیجه می شود و مقادیر مقاومت پایین تر از مقادیر به دست آمده با دیگر فوق روان کننده ها می باشند.
افت اسلامپ بیشتر وقتی رخ می دهد که (1) تاخیر طولانی میان اضافه شدن فوق روان کننده و نمونه گیری وجود داشته باشد، (2) تاخیری طولانی میان اختلاط و اضافه شدن فوق روان کننده وجود دارد، و (3) هنگامی که دماهای بتن خیلی بیشتر از دماه��ی محیطی باشد. روش های مورد استفاده برای حداقل کردن مشکلات افت اسلامپ در بتن آماده شامل 1: کاربرد افزودنی دیر گیر کننده با پایه اسید هیدروکسی کربوکسیلات در ارتباط با فوق روان کننده، 2: کاربرد یک فوق روان کننده دیرگیر کننده، 3: اضافه شدن فزاینده افزودنی بیشتر برای تجدید کردن اسلامپ اصلی، و 4: کاربرد خاکستر بادی. روش (3) به طور موفقیت آمیزی در محل پروژه استفاده شده است. اخیرا، فرآورده هایی در دسترس قرار گرفته اند که از طریق طبیعت شیمیایی آنها، امکان امتداد قابل توجه دوره کارایی ایجاد می شود.