انتخاب ترکیبی از الیاف و خمیر به گونه ای که اندرکنش های نامطلوب حذف شده یا کاهش یابند، و یا اندرکنش ها به گونه ای بی خطر و ملایم اتفاق بیفتند، می تواند دوام FRC را افزایش دهد. اما رویکرد عمومی برای بهبود مقاومت الیاف در برابر مواد مهاجم، از طریق تغییر شیمیایی یا بهسازی سطحی آنها، و یا خمیرهای سیمانی غیر پرتلند یا اصلاح شده متمرکز می باشد که دارای خطر کمتری برای الیاف می باشند. این خطر کمتر، از خاصیت قلیایی کمتر محلول حفره ای و تمایل کمتر آن به ته نشینی محصولات هیدراسیون در سطح مشترک الیاف- خمیر، و یا نفوذپذیری کمتر به منظور محدود ساختن ورود عوامل مضر، ناشی می شود.
توسعه الیاف شیشه دارای رشد نسبتا خوبی بوده است. از همان اوایل تولید FRC شیشه، مشخص گردید که الیاف E-Glass (چنانکه در صنعت FRP استفاده گردید) از نظر شیمیایی در خمیر سیمانی با خاصیت قلیایی بالا، ناپایدار می باشند. شیشه مقاوم در برابر قلیا (AR) در دهه 1970 توسط پلیکینگستونز براساس شیشه آب آهک سیلیسی با افزودن حدود 16% زیرکونیوم و با نام تجاری Cem-FIL تولید گردید. با این وجود، FRC شیشه ساخته شده از الیاف AR در برابر آسیب ایمن نبودند و با پیشرفت های بیشتر صورت گرفته، پوشش محلول یا مواد «تثبیت کننده» به الیاف اعمال گردید (ابتدا این مواد برای اهداف تولید اعمال می شد). وجود پلی هیدروکسی فنول ها در تثبیت کننده، رفتار هیدراسیون خمیر سیمان در سطح مشترک را اصلاح نموده و دوام FRC شیشه AR را به میزان قابل ملاحظه ای افزایش می دهد. الیاف شیشه AR با چنین پوشش هایی به الیاف «نسل دوم» معروف بوده و اکنون از استاندارد های صنعت محسوب می شوند. توسعه این مواد تثبیت کننده در حال ادامه می باشد. گاهی اوقات، دیگر سیستم های شیشه نیز توصیه می شوند، مثلا شیشه برپایه استرونتیوم یا بریوم، اما این محصولات به تازگی اهمیت تجاری یافته اند. الیاف فولادی اگرچه در خمیر قلیایی سیمان پایدار می باشند، اما در صورت به هم خوردن این خاصیت قلیایی مثلا توسط یون های کلر یا کربناسیون، چنانکه برای RC وجود دارد، این الیاف در معرض خوردگی قرار خواهند داشت. بنابراین در محیط های شدید مانند کاربردهای دریایی، الیاف فولادی ممکن است گالوانیزه شوند (با فلز روی پوشش داده شوند). فولاد آلیاژی با مقادیر اندک کرومیوم یا نیکل، اما نه به طور کامل «ضد زنگ»، مقاومت زیادی را در برابر زنگ زدگی نشان می دهد، اما فولاد ضدزنگ معمولی (یعنی Cr حدود 15%) نیز ممکن است استفاده شود. هر دو نوع الیاف گالوانیزه و ضد زنگ، مقاومت خیلی بیشتری در برابر زنگ زدن حین سالخوردگی را نسبت به الیاف فولادی با کربن پایین نشان می دهند. الیاف دیگر معمولا دارای ترکیب ثابتی بوده (مانند کربن، پلی پروپیلن و سلولز) و در نتیجه به راحتی نمی توان مقاومت قلیایی طبیعی آنها را افزایش داد.
پربازدیدترین مطالب ما را از دست ندهید!
یک روش آزمایشگاهی افزایش دوام، پیش آغشته سازی استرندهای الیافی با موادی است که می توانند از تسریع تولید محصولات هیدراسیون در بین رشته ها جلوگیری کرده و یا ماهیت هیدراسیون را به گونه ای تغییر دهند که محصولات هیدراسیون مضر کمتری تولید گردد. استرندهای الیاف شیشه با میکروسیلیس یا پلیمرهای اکریلیک آغشته سازی شده و الیاف طبیعی نیز با میکروسیلیس بهسازی (فرآوری) شده اند. در هر دو مورد، مقاومت در برابر سالخوردگی تسریع شده و یا هوازدگی به میزان قابل توجهی افزایش یافته است. این روش هنوز به صورت تجاری مورد استفاده قرار نگرفته است، اما قابل توجه به نظر می رسد.
مرسوم ترین روش تاکنون شامل اصلاح خمیر سیمان می شود تا بتوان با استفاده از افزودنی ها در سیمان پرتلند یا استفاده از خمیرهای سیمان غیرپرتلند، سازگاری خمیر سیمان با الیاف را افزایش داد. تعداد مراجع و مطالب بسیاری در ارتباط با این موضوع، خصوصا FRC شیشه موجود می باشد که مطالب پیش از سال 1988 در کتاب هایی توسط ماجومدار و لاز و بنتور و میندس گردآوری و خلاصه شده است.
هدف از افزودنی ها عموما کاهش خاصیت قلیایی محلول حفره ای خمیر و یا واکنش با هیدروکسید کلسیم تولید شده هیدراسیون می باشد. بنابراین مواد پوزولانی، که برای بهبود بتن معمولی استفاده می شوند، افزودنی های مرسومی می باشند. میکروسیلیس تغلیظ شده (CSF)، متاکائولین، سرباره آسیاب شده کوره ذوب آهن (GGBS) و خاکستر بادی پودر شده (PFA) همگی برای استفاده با اغلب انواع الیاف، مورد بررسی قرار گرفته اند. برای FRC فولادی، همین افزودنی ها اغلب استفاده یم شود، اما هدف از آنها چنانکه در بتن مسلح (RC) مطرح است، کاهش نفوذپذیری خمیر و در نتیجه ورود یون های کلر، کربناسیون و آب می باشد. اما مطالعات اندکی مستقیما بهبود دوام FRC فولادی ناشی از اصلاح خمیر را، در قالب کاهش خصوصیات مکانیکی، مورد بررسی قرار داده اند.
CSF یک محصول جانبی صنعت فروسیلیکون بوده و شامل ذرات بسیار ریزی (µm1>) از سیلیس خالص می باشد که به سرعت ب�� Ca(OH)2 واکنش می دهد. این ماده به عنوان بهبود دهنده خمیر برای FRC سلولزی/ طبیعی، FRC سرامیک، FRC کربن (که کاربرد اولیه آن کمک به توزیع و تراکم الیاف می باشد) و FRC شیشه استفاده می شود. این ماده در افزایش دوام ترکیبات الیافی طبیعی قرار گرفته در معرض هوازدگی و سالخوردگی ناشی از چرخه های تر و خشک شدن موثر می باشد، اما دارای اثر محدود یا متغیری بر روی دوام FRC شیشه در معرض سالخوردگی با آب گرم خواهد بود. مقادیر افزودن این ماده بین 10% تا 40% جایگزین سیمان بوده، اما در مقادیر بالاتر جایگزینی، این ماده می تواند اثر نامطلوب قابل ملاحظه ای بر کارآیی داشته باشد و در نتیجه نیازمند نسبت های بالاتر آب به سیمان (W/C) برای تولید بوده و این نامطلوب می باشد. در FRC فولدی، گزارش شده است که جایگزینی 15% سیمان با CSF ورود کلرید و ضریب انتشار کلرید را با یک ضریب 3 کاهش می دهد و جایگزینی 5/8% سیمان با CSF اثر غیرطبیعی بر مقاومت پوسته شدن ناشی از نمک یخ زدایی خواهد داشت. یان و همکاران گزارش نمودند که جایگزینی 5/2% سیمان با CSF، مقاومت FRC فولادی در برابر خستگی را دو برابر نموده است. متاکائولین یک رس چینی آهکی است که به سادگی با Ca(OH)2 در خمیر واکنش داده و خاصیت قلیایی محلول حفره ای را کاهش می دهد. این ماده به عنوان یک افزودنی FRC شیشه جهت بهبود دوام، به طور گسترده ای مورد بررسی قرار گرفته است. تقریبا کلیه محققین بر این موضوع اتفاق نظر دارند که افزودن این ماده به میزان 20 تا 25 درصد جایگزین سیمان، عملکرد دوامی FRC شیشه را هم تحت شرایط هوازدگی تسریع شده (یعنی آب گرم) و هم هوازدگی طبیعی بهبود می بخشد. میزان این بهبود به چگونگی تفسیر نتایج سالخوردگی تسریع شده بستگی دارد، اما این مقادیر برای فرمول های تجاری جهت استفاده به خوبی تعیین گردیده است. همچنین عقیده بر آن است که متاکائولین پرداخت سطحی و مقاومت در برابر تخریب نمای ظاهری ناشی از غبارگرفتگی و یا شوره زدن را بهبود می بخشد. به نظر نمی رسد که این ماده جهت بهبود دوام به همراه دیگر انواع الیاف به جز مورد گزارش دشه توسط گوتیرز و همکاران استفاده شده باشد که آنها نیز تغییرات در خواص مکانیکی را با زمان کنترل ننموده اند و تنها انتشار کلرید را مرود توجه قرار داده اند. گزارش شده است که جایگزینی 15% سیمان با متاکائولین در FRC فولادی، انتشار کلرید را مورد توجه قرار داده اند. گزارش شده است که جایگزینی 15% سیمان با متاکائولین در FRC فولادی، انتشار کلرید را با ضریب مشابهی برای CSF کاهش می دهد.
GGBS با FRC طبیعی و FRC شیشه با موفقیت نسبتا کمی مورد استفاده قرار گرفته اند. گزارش گردید که تاثیر آن بر روی FRC شیشه در سطوح بسیار بالای جایگزینی سیمان (70%) مثبت بود، اما این موضوع از نظر تجاری مورد توجه نمی باشد، هرچند که برخی فرمول های ژاپنی از سیمان سرباره کوره ذوب آهن به همراه دیگر افزودنی ها استفاده می کنند. خمیر دوراپکت که ترکیبی است که FRC شیشه ساخته شده با آن دارای هدف ضمانت طول عمر 50 ساله می باشد، براساس سیمان سرباره کوره ذوب آهن به همراه میکروسیلیس ساخته می شود. به نظر نمی رسد که GGBS حتی با مقدار 70% جایگزین سیمان در کاهش انتشار کلرید در FRC فولادی به اندازه CSF یا متاکائولین موثر باشد. PFA در FRC پلی پروپیلن و FRC شیشه استفاده شده است. FRC پلی پروپیلن با PFA ترکیبی است که در مطالعه بلندمدت توسط هانات مورد بررسی قرار گرفته است (شکل 9-1 را نیز ملاحظه نمایید). به نظر می رسد که چنین ترکیباتی، بیشتر مقاومت خود را پس از 18 سال هوازدگی حفظ می کنند، اما هیچگونه مقایسه ای با خمیر OPC اصلاح نشده صورت نگرفته است. به نظر می رسد که افزودن PFA به FRC شیشه از نظر افزایش دوام، دارای مزایایی می باشد. بهبودهای دوامی گزارش شده توسط سیر و همکاران نتیجه سیستم ترکیبی شامل PFA و میکروسیلیس بوده و در نتیجه نمی تواند تنها ناشی از PFA باشد.
باید خاطرنشان نمود که افزودن PFA و GGBS موجب گیرش و سخت شدن کندتر خمیر و در نتیجه مقاومت های کمتر خمیر در سنین اولیه می گردد.
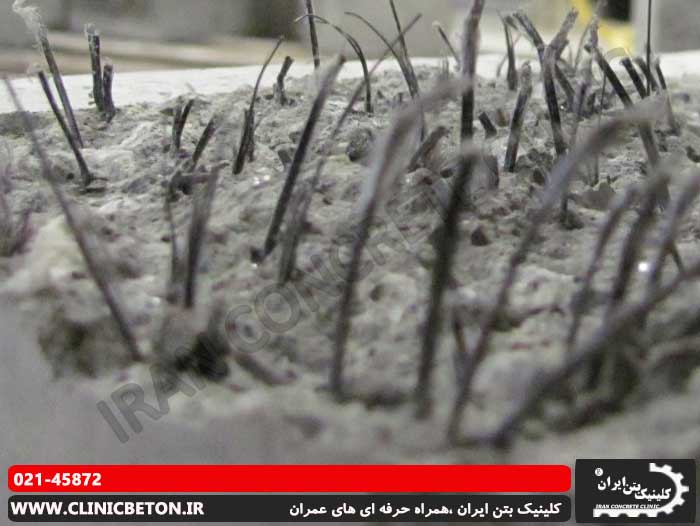
الیاف در بتن
راهکار دیگری که در FRC شیشه به کار گرفته شده عبارت است از اصلاح پلیمری خمیر. ماجومدار و لاز م یک مقاله کامل را به این موضوع اختصاص داده اند. انواع مختلفی از پلیمرها امتحان شده اند، اما خیرا توجه زیادی بر روی پراکنش پلیمر اکریلین (فورتون) متمرکز گردیده است. این ماده که در ابتدا به عنوان یک عمل آورنده کمکی برای مقاطع بتنی نازک طراحی شده بود تا از افت آب ناشی از تبخیر که منجر به ترک جمع شدگی می گردد، جلوگیری نماید، به FRC شیشه افزوده می گردد تا کارآیی را در حالت تازه افزایش داده و قالب گیری را بهبود بخشد. همچنین بسیاری قیده دارند که این ماده می تواند دوام و فرمول «5/5» را که شامل FRC شیشه OPC به علاوه 5% حجمی ذرات جامد پلیمر فورتون و 5% وزنی الیاف شیشه AR بوده و در مراجع FRC شیشه موجود می باشد، بهبود بخشد به گونه ای که این ماده اغلب به صورت ضمنی تحت عنوان «پایه»ای قلمداد می شود که اصلاح کننده هایی مانند متاکائولین بعدا به آن افزوده می شوند. مکانیزمی که توسط آن دوام افزایش می یابد، با پوزولان ها متفاوت می باشد که در آن خاصیت قلیایی ناشی از تشکیل Ca(OH)2 کاهش نمی یابد، بلکه در این فرآیند، الیاف با یک لایه محافظ پوشش داده می شوند و یا هیدراسیون در سطح مشترک اصلاح می گردد که این کار از طریق اشغال فضاهایی که ممکن است توسط Ca(OH)2 پر شوند، صورت می گیرد. بحث هایی در ارتباط با این موضوع وجود دارد که آیا اصلاح پلیمری خمیر واقعا می تواند منجر به افزایش دوام گردد، با وجودی که روش های سالخوردگی تسریع شده اغلب نتایج متضادی را حاصل می نمایند. جدیدترین پژوهش ها به وضوح نشان می دهند که سالخوردگی ناشی از آب گرم، برای FRC اصلاح شده پلیمری مناسب نبوده و همچنین افزودن پلیمر به خمیرهای اصلاح شده و OPC ساده، از نظر دوامی می تواند بسیار مفید باشد به گونه ای که در مدت 19 سال هوازدگی طبیعی، کاهش مدول شکست (MOR) ناچیز بوده و در مقایسه با FRC شیشه شامل خمیر OPC ساده، کرنش گسیختگی تا 75% کاهش یافته است. اصلاح پلیمری خمیر با انواع دیگر الیاف، غیرمعمول می باشد، اما خلاصه ای از آن توسط بنتور و میندس ارائه شده است. بتن اصلاح شده پلیمری به ندرت به عنوان خمیری برای FRC فولادی استفاده یم شود، اما پلیمر عموما برای بهبود کارآیی، و نه بهبود دوام، استفاده می شود، هرچند برخی نویسندگان ادعا می کنند که این ماده می تواند به بهبود دوام کمک نماید. دیگر سیستم های سیمانی مرسوم غیر پرتلند (nP) نیز جهت استفاده در FRC مورد بررسی قرار گرفته اند. باز هم مشخص گردید که این تکنیک برای FRC شیشه نسبت به دیگر سیستم ها، توسعه بهتری یافته است. استفاده از سیستم های nP برای FRC شیشه توسط ماجومدار و لاز به صورت خلاصه گردآوری شده است. سیمان با آلومینای بالا (HAC) و سیمان با سولفات بالا هر دو دارای خاصیت قلیایی کمتری نسبت به OPC بوده و در نتیجه گزینه هایی برای FRC شیشه محسوب می شوند. نگرانی های مربوط به یکپارچگی خمیر HAC در دماهای نسبتا بالا (واکنش «تغییر حالت») که منجر به ممنوعیت استفاده سازه ای از آن در انگلستان گردید، موجب گردیده است که تولید کنندگان FRC شیشه، با وجود مشخصات دوامی عالی این ماده، با احتیاط از آن استفاده نمایند. سیمان با سولفات بالا نیز مقاومت خوبی را در برابر سالخوردگی نشان داده است، اما گزینه مرسومی برای FRC شیشه نمی باشد، زیرا در معرض ضعیف شدن ناشی از کربناسیون قرار دارد که در مقاطع عموما نازک FRC احتمال آن زیاد می باشد.
طی 10 سال گذشته، توجه به خمیرهای nP برپایه سولفو- آلومینات کلسیم افزایش یافته است. این سیمان ها با 4CaO.3Al2O3.SO4 (ترکیب کلین یا یلمیت) به عنوان جزء فعال اصلی، در حضور یک منبع آهک هیدراته و اترینگایت را به عنوان محصول اصلی و کمی نیز هیدروکسید کلسیم تولید نموده که در ساختار فاز هیدراته باقی می ماند و محلول حفره ای با خاصیت قلیایی کمتری نسبت به OPC حاصل می شود. این نوع سیمان ها در چین و ژاپن تولید گردید، اما مشابه آنها در انگلستان و ایالات متحده نیز موجود می باشد. داده های اندکی در ارتباط با خصوصیات بلندمدت FRC شیشه ساخته شده با چنین سیمان هایی وجود دارد، اما این سیمان ها مقاومت فوق العاده ای را در برابر سالخوردگی تسریع شده با آب گرم از خود نشان می دهند. با این وجود، در تفسیر اینگونه داده ها باید احتیاط نمود. توسعه این خمیرها در حال ادامه بوده و به نظر می رسد که این خمیرها، بهترین گزینه برای FRC شیشه کاملا با دوام، محسوب می شوند. استفاده از خمیرهای nP با الیاف دیگر، کمتر در مراجع مشاهده شده است. پورتاس و همکاران، PFAها و سرباره های کوره ذوب آهن فعال شده با قلیا به همراه الیاف پلی پروپیلن را در معرض سالخوردگی چرخه ای، مورد بررسی قرار داده اند. نتایج به دست آمده غیر واضح بوده و هیچگونه مزیت عمده ای نسبت به OPC را نشان نداند. فرانتزیس و باگوت یک روش آزمایش «دوام» را برای پیوستگی میان الیاف فولادی و سیمان های سولفات منیزیم آلومینات کلسیم گزارش نمودند، اما هیچگونه مزیت دوامی را برای اینگونه خمیرها در مقایسه با سیمان پرتلند پیشنهاد نکردند. ترکیب روش ها نیز مرسوم می باشد که واضح ترین مورد آن ترکیب پلیمر با یک افزودنی پوزولانی می باشد، زیرا این اجزاء با مکانیزم های متفاوتی عمل نموده و ممکن است دارای یک اثر تقویتی باشند. مقاله جامع اخیر بال در ارتباط با هوازدگی بلندمدت FRC شیشه اصلاح شده با پلیمر، گزارشی در مورد نمونه های ترکیب پلیمر با متاکائولین و CSF ارائه می نماید که در فواصل تا 13 سال آزمایش شده اند. هیچکدام از نمونه های ترکیبی و تنها اصلاح شده با پلیمر در طول این مدت دچار آسیب عمده ای نشدند، بنابراین به هیچگونه نتیجه قطعی نمی توان دست یافت. بسیاری از ترکیبات ذکر شده در بالا شامل ترکیب مثلا سولفو- آلومینات و متاکائولین (کالکریت)، سیمان سرباره کوره ذوب آهن و سولفو- آلومینات ها (ناشرین) یا سیمان سرباره کوره ذوب آهن و میکروسیلیس (دوراپکت) می باشند. از آنجا که هدف از هر یک از اجزاء بهبود دوام از طریق مکانیزمی با تاثیر مشابه می باشد، در نتیجه اثر تقویتی به حداقل رسیده و یک جزء دارای اثر غالب خواهد بود، اما از آنجا که کاهش دوام در حالت ترکیب اجزاء مختلف نسبت به خمیرهای اصلاح نشده غیرمحتمل می باشد، جزئیات این موضوع تنها در محدوده بحث های علمی و دانشگاهی مورد توجه می باشد.
خمیر سیمانی در FRC در معرض واکنش با دی اکسید کربن هوا قرار دارد، پدیده ای که کربناسیون نامیده می شود. در طول این واکنش، پرتلندیت در خمیر به Ca(CO)3 تبدیل شده و در نتیجه ظرفیت میانگیری محلول حفره ای از دست می رود، مواد قلیایی نیز به کبنات ها تبدیل شده و یا جذب فاز C-S-H می شوند (و نیز کربنات ها، کلسیم زدایی می شوند) و خاصیت قلیایی خمیر به شدت افت می کند. همچنین مقاومت افزایش می یابد. بنابراین از نظر تئوری، یک خمیر کربناته با اغلب الیاف سازگارتر ��ی باشد (به جز الیاف فولادی). کربناسیون طبیعی برای اجزاء FRC می تواند سال ها به طول بانجامد، اما تلاش هایی برای اعمال کربناسیون تسریع شده به منظور بهبود دوام صورت گرفته است. آزمایشات سالخوردگی تسریع شده برای الیاف طبیعی یا FRC سلولزی شامل یک جزء کربناسیون می باشد، زیرا این مواد هنگام قرارگیری در معرض هوازدگی، به سادگی تمایل به کربناته شدن دارند. به نظر می رسد که برخی ابهامات در مراجع درباره تفاوت میان کربناسیون به عنوان یک راهکار علاج بخشی و یا یک فرآیند سالخوردگی وجود دارد، اما اتفاق نظر اخیر بر آن است که عمل آوری اولیه چنین ترکیباتی در یک محیط مملو از CO2، دوام این ترکیبات را افزایش می دهد.
پرنل و همکاران از CO2 فوق بحرانی برای تاثیر برکربناسیون اجزاء FRC شیشه شامل خمیر OPC در مدت چند ساعت، استفاده نمودند. این راهکار علاج بخشی، مقاومت چنین ترکیباتی در برابر سالخوردگی تسریع شده به میزان قابل توجهی افزایش داد، خواص مکانیکی را بهبود بخشید و پایداری ابعادی آنها تحت شرایط تر و خشک شدن را افزایش داد. در FRC فولادی، کربناسیون نامطلوب بوده و بنابراین به عنوان یک راهکار علاج بخشی استفاده نمی شود.