یکی از بهترین راه ها برای اطمینان از صلبیت و متراکم بودن بتن، افزایش پوشش بتنی روی آرماتورها است. بتن صلب و متراکم را می توان با افزایش حداقل حجم سیمان به 350 کیلوگرم در متر مکعب در بتن های معمولی که البته به موقعیت و درجه ی شوری بتن بستگی دارد، کاهش نسبت آب به سیمان، استفاده از مواد کاراساز برای بهبود کارایی با کاهش آب مصرفی، ویبره کردن بتن بطور کامل و اطمینان از عمل آوردن اولیه به اندازه کافی، ساخت.
چون سیمان پرتلند روباره ای، خمیر چسبناک و متراکمی از سیمان را ایجاد می کند، برای کاربردهای مرسوم توصیه می شود (باید شامل حدود 65 تا 70 درصد مواد روباره در وزن سیمان بوده و با یکدیگر مخلوط شده و در فرآیند آسیاب سیمان تولید شده باشد).
این تراکم باعث ساکن شدن حرکت یون کلر می گردد. زیرا باعث ایجاد ملات غیر قابل نفوذی در بتن می شود. همچنین استفاده از پوشش های اپوکسی روی آرماتورها خیلی مفید نخواهد بود. نمک های کلیرد قابل حل بوده و اگر هرگونه رطوبتی در بتن به حرکت در آید، یون های کلر ممکن است توسط این رطوبت از درون بتن جابجا شده و به سمت نقطه ی مشخصی از سازه متمرکز شوند. این تئوری بطور یقین از نتایج بیشمار و متفاوتی که از آنالیزهای شیمیایی روی بتن سخت شده با کلرید کلسیم همراه با یه تسریع کننده انجام شده است بدست آمده است.
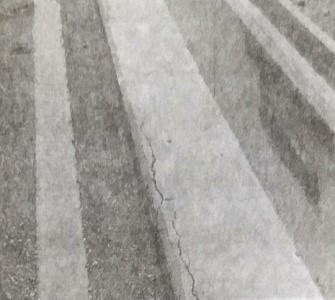
شکل 159- ترکیدگی جدول پیاده رو ناشی از فشار انبساط درونی بتن بدلیل خوردگی آرماتور | 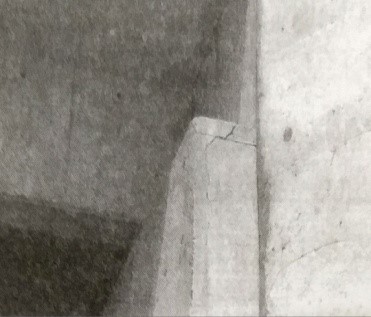 شکل 160- ترکیدگی بتن (در بالای کوله) متعاقب خوردگی آرماتور |
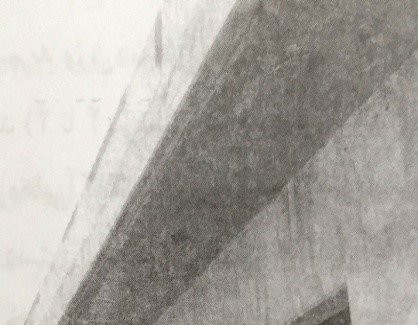
شکل 161- لایه لایه شدن بتن در زیر دال عرشه، ناشی از خوردگی مخفی با فعالیت آشکار | 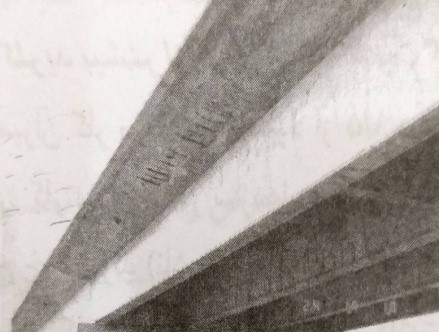
شکل 162- لایه لایه شدن بتن و افتادن آنها همراه با نمایان شدن آرماتورهای خورده شده |
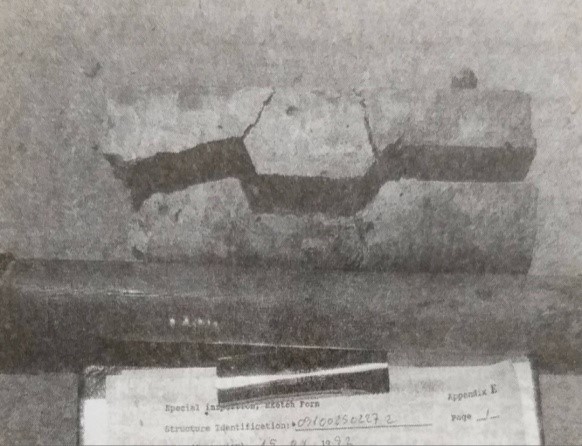
شکل 163- یک نمونه بتنی خارج شده از «کلید برش گیر» که بطور واضح شکستن آن را نشان می دهد.
اندازه های کمکی در مقابل اثرات خوردگی
قبل از هرگونه تعمیر برای ترک های ناشی از پوسیدگی و زنگ زدگی و جداشدگی بتن از آرماتورها، توجه به این نکته ضروری است که لازم است برای تعیین مقدار کلر موجود در محل آزمایشاتی انجام گیرد. راهنمای نمونه برداری و آزمایشات بر روی کلرایدها در استاندارد ASTM موجود است. تعیین سطح کلر بطور معمول برحسب درصد معادل کلرید کلسیم در وزن سیمان تعیین می شود.
الف) کلرید کمتر از 5/0 درصد (نسبت کلرید کلسیم به وزن سیمان)
نتایج وجود این سطح از کلر مساعد و پایدار بوده و از منابع طبیعی نظیر سنگدانه ها نشات می گیرد و حالت یا وضعیت مشکل سازی را ایجاد نمی کند. ترکها و جداشدگی ها در این حالت از کربناسیون و فقدان پوشش کافی در آرماتورها و وجود بتن نفوذپذیر ناشی می شوند. این عوامل را باید بررسی نمود و اگر محرز باشد روش تعمیر و علاج باید براساس این عوامل انجام شود.
ب) کلرید بیشتر از 5/0 درصد (نسبت کلرید کلسیم به وزن سیمان)
اگر میزان کلر متفاوت و معمولا از 5/1 درصد تجاوز کند (2 تا 4 درصد)، نشانگر بیش از اندازه بودن میزان کلر می باشد. در سازه هایی نظیر عرشه ی پلها یا سازه هایی که تمرکز بالایی از کلر در نزدیک سطح خود دارند (ناشی از نمک های یخ زدا)، باید مطابق دستور العمل رفتار گردد. هنگامی که میزان بالا بودن کلر اثبات شد، باید به خاطر داشت که فرآیند خوردگی را نمی توان به آسانی متوقف نمود (مثلا با درزگیری). اثر کلر بدلیل اینکه رطوبت را نمی توان مهار نمود همچنان ادامه خواهد یافت.
تمامی بتن متاثر شده از زنگ زدگی در اطراف آرماتورهای زنگ زده باید برداشته شود (اطراف کلیه آرماتورها). فولاد و بتن واقع در نما باید تمیز شوند، ترجیحا با سند بلاست نمودن. همچنین آرماتورهای اضافه ای باید بجای آرماتورهای از دست رفته و خورده شده نصب شود. بتن واقع در معرض دید باید توسط آب، اشباع شده و شستشو شود و بالاخره بتن یا ملاتی در لایه هایی با فشار باد (شاتکریت) در محل مورد نظر جایگزین شوند. عمل اشباع نمودن توسط آب را در صورتی که از ملات یا بتن اپوکسی استفاده شود باید متوقف نمود، مگر اینکه اپوکسی در مقابل آب حساس نباشد.
البته این احتمال وجود دارد که برخی از نقاط تقویت شده بتن بعد از این مرحله دچار ترک های زنگ زدگی شوند. بنابراین باید تصمیمی بر اینکه نشان دهد چه مقدار از بتن باید برداشته شود اتخاذ گردد. این تصمیم گیری معمولا به مسائل و مشکلات مالی محدود می شود. در برخی از حالتها بازدیدهای متوالی و متناوب و سپس تعمیر، از خرابی و برداشت های وسیع اقتصادی تر است.
ترک های ناشی از پوسیدگی آرماتور بدلیل کربناسیون در بتن
کربناسیون فرآیندی است که در آن دی اکسید کربن (موجود در اتمسفر) تحت تاثیر با هیدرواکسید کلسیم (غیر محلول در آب خالص) موجود در بتن سازه واکنش می دهد و در نتیجه شکل گیری کربنات کلسیم در این واکنش، خاصیت اسیدی زیاد شده چون PH در مخلوط بت�� کاهش می یابد. در نتیجه، میلگردهای فولادی خورده می شوند. زیرا قلیایی های بتن با کاهش PH کم می شود و در طی فرآیند کربناسیون انفعال پذیری اطراف میلگرد تنزل پیدا می کند.
افزایش حجم و پیامدهای ناشی از خوردگی (اکسید ترکیبات آهن که حجمی بیشتر از حجم فولاد اولیه دارد) باعث ایجاد یک تنش شعاعی قوی اطراف میلگردهای فولادی می شود که در نتیجه آن ترک های شعاعی موضعی در محل ایجاد می شوند که به راحتی در دسترس اکسیژن، رطوبت و یون های کلر در بتن قرار دارد و شرایطی را ایجاد می کند که خوردگی ادامه یافته و باعث بروز ترک های بیشتری شده و نهایتا یک گسیختگی و شکاف عمده ایجاد می شود. در اینجا نیز عامل تراکم در بتن کمک زیادی به مقابله با اثرات شیمیایی خواهد نمود.
ترک های ناشی از پوسیدگی آرماتور بدلیل قرار گرفتن در معرض رطوبت و اتمسفر
آرماتورها، فلادهای پیش کشیده و بیشتر عناصر فولادی اگر در معرض رطوبت اتمسفر و در معرض دید قرار گیرند دچار خوردگی ناشی از واکنش شیمیایی با اکسیژن خواهند شد. این واکنش حتی اگر فولاد درون بتن قرار گرفته باشد ادامه دارد. چون اکثر پوسیدگی ها باعث ایجاد حجمی بیشتر از حجم فلز اولیه می شوند، این فرآیند تولید تنش های شعاعی بزرگی اطراف بتن کرده و پکیدگی در بتن ایجاد می شود که به شکل یک خط اثر از ترک می باشد. این ترک می تواند بتن را بصورت ورقه هایی از هم جدا کرده (ورقه ورقه شدن) و سرانجام خسارت ایجاد می شود. استفاده از بتن متراکم برای مقابله با مشکل پوسیدگی مفید است اما در وهله اول فولاد پوسیده نباید مورد استفاده قرار گیرد زیرا زودتر در معرض خطر قرار می گیرد.
ترک های ناشی از واکنش قلیا (در سیمان) با دسته مخصوصی از سنگدانه های واکنش پذیر
فرم نادری از باز شدگی و شکاف خوردگی می تواند تحت شرایط رطوبت و متعاقب آن با واکنش ترکیباتی از سیلیکات و کربنات در بعضی سنگدانه ها با مواد قلیایی موجود در سیمان اتفاق بیافتد. واکنش بین سیلیکات و قلیا تولید ژلی می کند که حجم بیشتری را اشغال کرده و باعث باز شدگی و شکاف شده و معمولا از منبع انبساط گسترش می یابد. اما این شکافها ممکن است به سایر شکافها متصل شده و تشکیل یک الگویی شبیه نقشه که شبیه شکاف خوردگی نیستند می دهد. لازم به ذکر است که واکنش سنگدانه ها با مواد قلیایی نظیر کلرید و ولفات تنها تحت شرایط رطوبت صورت می گیرد. تشخیص مثبت بودن این پدیده می تواند تنها بوسیله تست های آزمایشگاهی روی نمونه های سیمان برداشته شده از ساختمان انجام شود.
بعضی از علائمی که اغلب وجود دارند ولی همیشه دیده نمی شوند عبارتند از:
- وجود ژل (شبیه صمغ خشک شده یا عسل) بیرون زده از شکاف ها که معمولا روشن اما گاهی اوقات رنگی است و در سطوح عمودی، رنگ این مواد شبیه لکه و در سطوح افقی از سطح بتن بیرون زده می باشد. ژل ممکن است به آسانی با رسوبات کربنات کلسیم یا شوره اشتباه شود.
- پکیدن: به دلیل پکیدن قطعات سنگدانه های واکنش دهنده درست زیر سطح بتن این پدیده ایجاد می شود. ژل ممکن است در کف این پکیدگی دیده شود، در غیر این صورت پکیدگی به آسیب های ناشی از سرما شباهت دارد.
(به تفاوت بین این دو مورد توجه داشته باشید)
- سایر علائم شامل خیسی دائمی یا رطوبت دائمی، تغییر رنگ و علائم قابل تشخیص انبساط بتن یم باشد.
- واکنش سنگدانه ها با قلیا یک پدیده طولانی مدت است که معمولا چند سال طول می کشد تا خود را نشان دهد.
جلوگیری و علاج ترک های ناشی از واکنش سنگدانه ها با قلیا
اگر سنگدانه ها شامل سیلیکات و کربنات های نامطلوب و واکنش پذیر باشند، در پی آمد این مساله واکنش شیمیایی وسیع و فراوان با قلیایی های سیمان می تواند به سمت افزایش حجم، حرکت های مهم (بسته شدن درزهای انبساط و غیر هم محور شدن تکیه گاه ها و سایر چفت ها و تجهیزات دیگر) و به سمت ایجاد ترک در بتن سوق پیدا کند.
برای جلوگیری:
جایگزینی بخش فعال با مصالح سنگی غیر فعال (واکنش ناپذیر) حتی اگر غیر اقتصادی باشد توصیه می شود. استفاده از سیمان با قلیایی پایین، جلوگیری از رطوبت آشکار اطراف بتن برای هر دوره و زمان مهم، استفاده از سیمان پرتلند روباره شامل 65 درصد روباره در وزن سیمان ( و بیشتر در حالت حمله کلر و سولفات روی آرماتور و سیمان، همچنین برای سازه های ساخته شده در مناطق دریایی یا نزدیک به آن) توصیه می شود. چون این سیمان تولید خمیری متراکم و نتیجتا بتن متراکم و غیر قابل نفوذی می نماید، رفتار فیزیکی واکنش قلیایی ها با سنگدانه ها را تغییر می دهد، زیرا این سیمان دارای مقدار کمی قلیا بوده و واکنش مذکور را کاهش می دهد (حجم کمتر قلیا بدلیل وجود 56 درصد روباره است).
برای علاج:
ترک ها را ممکن است با تزریق اپوکسی ولی نه بعد از 3 تا 5 سال درزگیری نمود. در این سن حداکثر شکل گیری ترک رخ خواهد داد. حتی این ترک ها ممکن است با یکی از روش های قابل کاربرد در سطح درزگیری شوند (برای جلوگیری از ورود آلودگی های بعدی) که در قسمت ترک های زنده بحث خواهد شد. البته تمام این روش های علاج فقط در صورتی امکان پذیر است که خسارت ایجاد شده ناشی از این ترک ها قابل توجه نباشد.
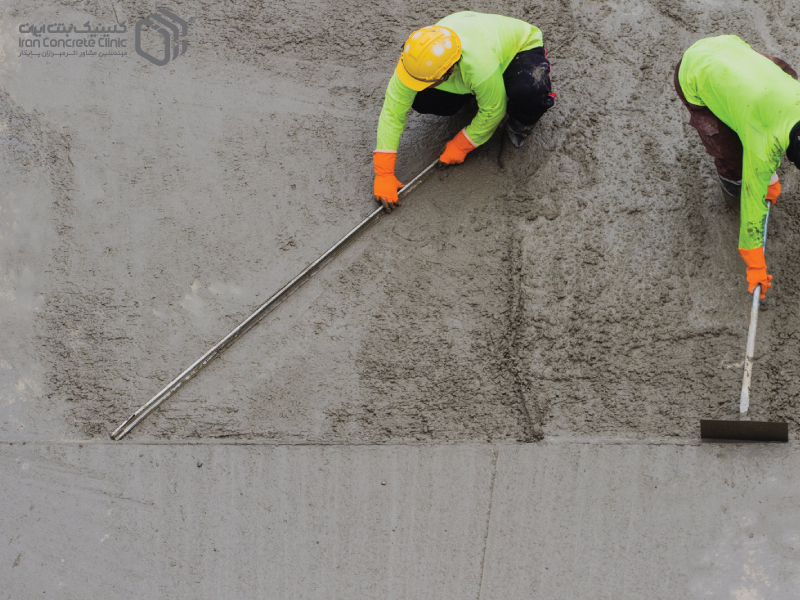
عکسی از ترمیم کردن ترک بتن