مدل های بسیاری از رفتار مکانیکی FRC وجود دارد که در میان آنها، توضیحاتی برای رفتار وابسته به زمان نیز یافت می شود. تشریح کامل کلیه این مدل ها نیازمند یک مقاله کامل است و در نتیجه این بحث به مدل هایی محدود می گردد که صراحتا فرآیند تخریب را مورد بررسی قرار می دهند. مدل ها، محدوده ای از توصیفات تجربی فرآیند افت مقاومت تحت سالخوردگی طبیعی و تسریع شده، تا روش های تحلیل پیچیده براساس بررسی تغییرات ریزساختاری در ناحیه میانی الیاف- خمیر را شامل می شوند. هدف از این مدل ها، انعکاس مباحث مربوط به مکانیزم های تخریب توصیف شده در بالا است که در آنها هر یک از مدل های جاری براساس فرضی که مربوط به مکانیزم اصلی فعال می باشد، استوار خواهد بود، یعنی اینکه عامل تخریب، تراکم خمیر/ ناحیه میانی و یا افت مقاومت الیاف خواهد بود.
قدیمی ترین مدلی که در آن یک موضوع دوامی قابل تشخیص می باشد، مدل «ACK» است که رفتار خمیر شکننده ترکیب را توصیف می نماید. بررسی رابطه 9-2 نشان می دهد که افزایش مقاومت خمیر و یا کاهش مقاومت الیاف، که هر دو در برخی FRCها با گذشت زمان قابل مشاهده می باشد، ممکن است مقدار موثر Vf را تا زیر مقدار بحرانی کاهش داده و در نتیجه حالت گسیختگی را از ترک چندگانه به شکست منفرد تغییر دهد. به سادگی می توان با طراحی دقیق ترکیب، از وقوع چنین حالتی پیشگیری نمود. با فرض آنکه الیاف کافی برای جلوگیری از شکست منفرد وجود داشته باشد، آنگاه پس از اولین ترک خمیر (یعنی نواحی II-IV در شکل 9-2) ترکیب مقاومت الیاف و «مقاومت پیوستگی» (یعنی تراکم خمیر) است که رفتار ترکیب را کنترل می کند. مدل ها نیز با فرض غالب بودن یکی از این دو پارامتر قابل دسته بندی می باشند.
مدل های تراکم خمیر
مدل کاتز و بنتور که برای FRC کربن ارائه شده است، دارای کاربرد عمومی می باشد. این مدل بر این اصل استوار است که «تراکم فیزیکی خمیر» علت افت مقاومت و طاقت با گذشت زمان می باشد. دو فرآیند همزمان مدلسازی گردید؛ افزایش پیوستگی الیاف- خمیر با زمان، و کاهش «طول مهاری» Ls یک رشته خم شده از الیاف که در دهانه یک ترک خمیر، بر اثر نیروی وارده، خم شده است. مورد اخیر این فرآیندها ابتدا به عنوان عامل تخریب FRC (خصوصا FRC شیشه) پیشنهاد شد و توسط استاک و ماجومدار مدلسازی گردید، که آنها ریز تصاویر الکترونی تکیه گاهی بسیاری را که نشان دهنده روند این فرآیند بود نیز ارائه نمودند. با سخت شدن خمیر، ناحیه تکه گاهی (شکل 9-12) کوچکتر می شود، یعنی بخش کمتری از خمیر در زیر الیاف خرد می شود.
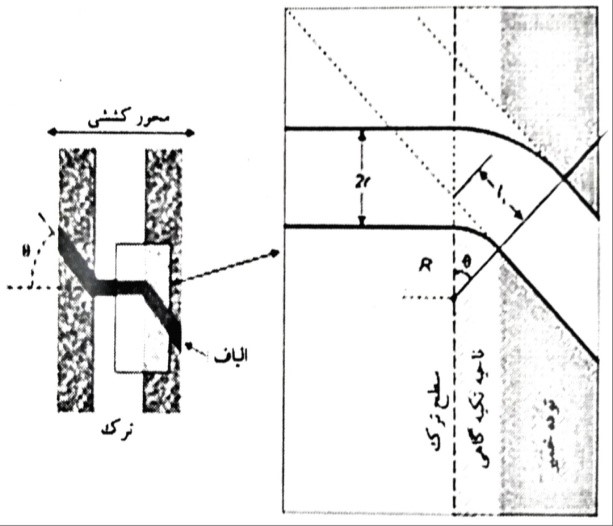
شکل 9-12- مدل توصیف خمش یک الیاف مایل قطع کننده ترک
شعاع انحناء R و طول مهاری Ls کاهش یافته و تنش خمشی در رشته الیاف ơB که به صورت زیر به دست می آید، افزایش می یابد.
(9-4) = (〖2E〗_f r sin〖0/2〗 )/(l_s+2r sin〖0/2〗 ) σ_B
مدل کاتز و بنتور همچنین عوامل دیگری مانند طول غیریکنواخت الیاف که بر اثر شکستگی حین اختلاط ایجاد می شود را نیز در نظر می گیرد. فرض می شود که پیوستگی و طول مهاری با سرعتی مشابه مقاومت فشاری، با زمان تغییر می کنند. مشخص گردید که فرآیندهای پیوستگی به تنهایی یک افزایش یکنواخت در کارآیی مقاومتی الیاف ایجاد می نمایند، در حالی که کارآیی طاقت پس از حدود 10 روز به حداثر خود رسیده و سپس هر دو این پارامترها در مدت 40 روز به مقدار ثابتی کاهش می یابند. فرآیند کاهش ناحیه تکیه گاهی به تنهایی موجب کاهش پیوسته «نسبت فعال الیاف» با زمان می گردد، اگر چه مشخص نیست که آیا این فرآیند پس از 60 روز به صورت مجانب خواهد بود. این شرایط موجب نقطه اوج های کوتاه مدت در کارآیی مقاومت و طاقت می گردد که تا 90 روز ادامه می یابد که باز هم مجانب بودن آنها مشخص نمی باشد. ترکیب این دو اثر، منحنی هایی را ایجاد نمود که به خوبی با رفتار ترکیبات FRC کربن واقعی تحت شرایط سالخوردگی تسریع شده تا 200 روز در دمای C°60 مطابقت داشتند (شکل 9-13).
%20%D8%A8%D8%A7%20%D8%B1%D9%81%D8%AA%D8%A7%D8%B1%20%D9%85%D9%82%D8%A7%D9%88%D9%85%D8%AA%20%D8%AF%D8%B1%20%D8%A8%D8%B1%D8%A7%D8%A8%D8%B1%20%D8%B2%D9%85%D8%A7%D9%86%20%D8%AF%D8%B1%20%D8%A8%D8%AA%D9%86%20%D9%85%D8%B3%D9%84%D8%AD%20%D8%A8%D9%87%20%D8%A7%D9%84%DB%8C%D8%A7%D9%81%20%DA%A9%D8%B1%D8%A8%D9%86.jpg)
شکل 9-13- ترکیب اثرات پیوستگی و خمش (AAF) با رفتار مقاومت در برابر زمان در بتن مسلح به الیاف کربن
این مدل بعدا توسعه یافت تا اثر تغییرات مدول الیاف نیز در نظر گرفته شود و مشخص گردید که شدت مکانیزم آسیب ناشی از تراکم خمیر با افزایش مدول و شعاع الیاف، افزایش یافته و وابسته به الیاف «شکل پذیر» نمی باشد. این موضوع توسط آزمایشاتی بر روی FRC ساخته شده با محدوده ای از الیاف پلیمری و کربنی تایید گردید.
مدل کیم و همکاران که برای FRC سلولزی ارائه گردید، همچنین فرض می نماید که آسیب بر اثر افزایش پیوستگی با زمان ایجاد می شود. مدلسا��ی براساس مفهوم تقویتی طاقت شکست صورت می گیرد که برابر است با مجموع ضریب شدت تنش (SIF) ایجاد شده بر اثر بارگذاری و SIF منفی بر اثر کشش نگهدارنده الیاف که در عرض ترک ایجاد می شود. این بسط ایده ای است که اولین بار توسط نامن و شاه مطرح گردید. این مدل نیازمند 14 پارامتر ورودی جداگانه شامل انرژی شکست پیوند شیمیایی میانی و ضریب پهن شدگی الیاف می باشد که اندازه گیری برخی از آنها دشوار بوده و به صورت عددی حل می شود. این مدل روندهای وسیعی در سالخوردگی FRC سلولزی را پیش بینی می نماید، اما مبتنی بر فرض «گسیختگی با یک ترک» می باشد که برای اغلب FRCها با Vf > Vfc غیرمعتبر می باشد. همچنین با استفاده از ایده ارائه شده توسط نامن و شاه، مباشر و لی این مدل را براساس یک الگوی مکانیک شکست/ اجزاء محدود برای تغییر رفتار بیرون کشیدگی با سختی ناحیه میانی، توسعه دادند. این مدل برای FRC طراحی گردید. این محققین افزایش سختی ناحیه میانی، و پیوستگی و اصطکاکی به ترتیب در حدود 4 و 2 را پس از 3 روز سالخوردگی تسریع شده، محاسبه نمودند.
مدل های افت مقاومت الیاف
پرنل و همکاران روش متفاوتی را در یک مدل طراحی شده برای FRC شیشه، اما با کاربرد گسترده تر در پیش گرفتند. آنها افت مقاومت در الیاف (و در نتیجه ترکیب) را که نتیجه رشد آرام و زیر بحرانی نقص های سطحی بر روی الیاف می باشد، مدلسازی نمودند. فرض می گردد که یک فرآیند خوردگی تنش به نام «خستگی استاتیکی» این فرآیند را به وجود می آورد که در محیط های قلیایی می تواند باتنش های بسیار کوچکی (مثلا تنش های جمع شدگی یا ناسازگاری حرارتی) آغاز شده و ممکن است با رشد کریستال های پرتلندیت در ناحیه میانی، شدت یابد. با ترکیب روابط توصیف کننده مکانیک شکست الیاف، رشد درزها و تئوری «قانون مخلوط ها» این محققین به رابطه نسبتا ساده ای میان مقاومت نرمال شده S (مقاومت اولیه + مقاومت= S) و زمان t تحت کنترل پارامتر k دست یافتند که k تابعی از دمای T در یک رابطه آرهنیوس می باشد (روابط 9-5 و 9-6).
(9-5) S = 1/√(1+kt)
(9-6) k = k0exp ((-∆G)/RT)
به این ترتیب، این امکان فراهم می گردد که فرآیند سالخوردگی تسریع شده با آب گرم به صورت رابطه ای درآمده و برای پیش بینی منحنی های مقاومت- زمان برای فرمول های مختلف FRC شیشه، مورد استفاده قرار گیرد. این مدل به مجموعه بزرگی از داده ها شامل بیش از 1100 نمونه برازش داده شد که شامل داده های جدید، داده های موجود در مراجع و داده های تجاری بودند (شکل 9-14).
![نمونه برازش مدل پورنل (S=[1+kt]-0.5) به خمیر سیمان پرتلند بتن مسلح به الیاف شیشه.](/portals/0/img/GalleryImages/%D9%86%D9%85%D9%88%D9%86%D9%87%20%D8%A8%D8%B1%D8%A7%D8%B2%D8%B4%20%D9%85%D8%AF%D9%84%20%D9%BE%D9%88%D8%B1%D9%86%D9%84%20(S%3D%5B1%2Bkt%5D-0.5)%20%D8%A8%D9%87%20%D8%AE%D9%85%DB%8C%D8%B1%20%D8%B3%DB%8C%D9%85%D8%A7%D9%86%20%D9%BE%D8%B1%D8%AA%D9%84%D9%86%D8%AF%20%D8%A8%D8%AA%D9%86%20%D9%85%D8%B3%D9%84%D8%AD%20%D8%A8%D9%87%20%D8%A7%D9%84%DB%8C%D8%A7%D9%81%20%D8%B4%DB%8C%D8%B4%D9%87..jpg)
شکل 9-14- نمونه برازش مدل پورنل (S=[1+kt]-0.5) به خمیر سیمان پرتلند بتن مسلح به الیاف شیشه. داده های S در برابر زمان از منابع مختلف.
این کار موجب به روز شدن کار پراکتور و همکاران گردید و نشان داد که ضرایب تسریع به دست آمده توسط آنها، نمی تواند به FRC شیشه با خمیر اصلاح شده اعمال گردد، زیرا انرژی فعال سازی ΔG مربوط به فرآیند افت مقاومت در مقایسه با FRC شیشه OPC متفاوت می باشد (kJ/mol59 در برابر kJ/mol49). این نشان می دهد که یک فرآیند تخریب متفاوت در کار می باشد که به اعتقاد این محققین مربوط می شود به عدم وجود Ca(OH)2 در خمیرهای اصلاح شده. در حقیقت، استفاده از ضرایب پراکتور و همکاران برای بررسی و صحت سنجی FRC شیشه شامل خمیر اصلاح شده، ممکن است دوام را در دمای C°60 تا حدودی بیش از حد تخمین بزند (جدول 9-1). این مدل همچنین می تواند جهت پیش بینی «عمر شکل پذیر متوسط» استفاده شود، یعنی مدت زمان میان تولید الیاف و هنگامی که مقاومت الیاف تا نقطه ای کاهش می یابد که در آن نواحی رفتاری II و III (در شکل 9-2) از بین می رود. عمر شکل پذیر به نسبت مقاومت اولین ترک به مقاومت اولیه بستگی دارد که به نوعی به مقدار الیاف و دمای بهره برداری وابسته می باشد، اما برای GRC جدید مرسوم، برای FRC شیشه و OPC در حدود 60 سل و برای FRC شیشه شامل خمیر اصلاح شده با متاکائولین و یا سولفو- آلومینات در حدود 80 سال پیش بینی می شود.
جدول 9-1- عوامل تسریع کننده برای بتن مسلح به الیاف شیشه با توجه به آب و هوای انگلستان برای ترکیبات دما/ عمر تخریب، در مقایسه با موارد ارائه شده توسط پراکتور و همکاران. مثلا عمر 1 روزه در C°50 برای بتن الیافی با الیاف شیشه و سیمان پرتلند معمولی معادل است با 120 روز قرارگیری در معرض آب و هوای انگلستان (براساس پورنل و همکاران)، یا 101 روز (براساس پراکتور و همکاران)
دمای سالخوردگی |
---|
خمیر | C°50 | C°60 |
سیمان پرتلند معمولی سولفو- آلومینات سیمان پرتلند معمولی+ متاکائولین پراکتور و همکاران | 120 20 18 101 | 340 39 35 272 |
مدل اورلوسکی و همکاران تا حدی براساس مدل پرنل استوار می باشد که در آن فرض می شود افت مقاومت FRC تحت کنترل رشد درزها و نقص هایی است که به صورت اجتناب ناپذیری حین ساخت دسته رشته ها و فرآوری الیاف به وجود می آیند، که این موضوع منجر به ضعیف شدن الیاف می گردد. پس از آنکه رشته های شیشه AR در محلول های حفره ای شبیه سازی شده در دماهای مختلف در معرض سالخوردگی قرار گرفتند و مقاومت کششی کنترل گردید، ملاحظه شد که افت مقاومت حتی در غیاب نیروهای رانشی آشکار مربوط به خستگی استاتیکی، همچنان اتفاق می افتد (شکل 9-15، نقاط مربعی).
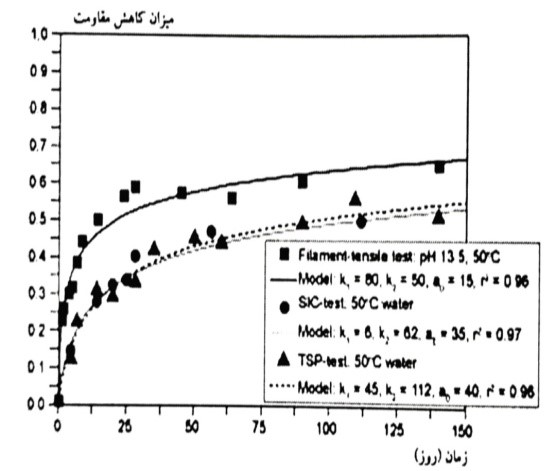
شکل 9-15- مقایسه نتایج آزمایش کشش دسته الیاف، SIC- و TSP- و کاربرد مدل خوردگی.
(مقاومت اولیه ÷ مقاومت) -1= درجه افت مقاومت.
به این ترتیب، این نتیجه به دست آمد که تخریب ناشی از نقص های ایجاد شده بر اثر تنها حمله شیمیایی بوده و هیچگونه تنش محرکی به وجود نیامده است. یک مدل سه پارامتری از افت مقاومت وابسته به زمان Δfl,t ((مقاومت اولیه ÷ مقاومت)-1= Δfl,t، یعنی S-1 با توجه به رابطه 9-5) ایجاد گردید. پارامترهای مورد نیاز عبارتند از عمق درز اولیه a0، امتداد درز X و ضرایب kl و k2، که مربوط می شوند به بخشی از واکنش های خوردگی که به ترتیب تحت کنترل محلول و انتشار قرار دارند:
(9-7) Δfl,t = 1- √(a_0/(a_0+ X ))
(9-8) - t = 0 (X/k_1 +X^2/〖2k〗_2 )
باید توجه نمود که رابطه 9-7 شکل گیری از رابطه 9-5 با kt = X/a0 بوده و هر دو براساس یک روش مکانیک شکست قرار دارند که رشد درز سطحی را به افت طول الیاف مربوط می سازد. شکل 9-15 مدل برازش یافته به داده های حاصل از نمونه های ترکیبی (TSP) و SIC که در آب دچار سالخوردگی شده و رشته هایی که در محلول قلیایی در دمای C°50 دچار سالخوردگی شده اند را نشان می دهد. مدلسازی نشان داد که نرخ حمله با زمان کند می شود که این امر ناشی از کند شدن انتشار یون های OH- بر اثر تشکیل یک لایه داخلی پایدار مملو از زیرکونیوم و یا تراکم مجدد گروه های سیلانول به عنوان یک لایه خارجی ممانعت کننده از رشد بیشتر درز می باشد. این مدل با کار قبلی در زمینه بررسی ترکیب سطحی شیشه AR دچار سالخوردگی در محلول های قلیایی، مطابقت دارد. آنها همچنین نشان دادند که یک مقدار رطوبت بحرانی وجود دارد -در محیط هایی که از این رطوبت تجاوز گردد، افت مقاومت مرتبط با دما خواهد بود- و یک حسگر رطوبتی مینیاتوری را جهت تعیین رطوبت در سطح شیشه AR در داخل بتن، ایجاد نمودند. با ترکیب اندازه گیری های حاصل از این دستگاه و روش مدل سازی بالا، امکان مدل سازی کامل شرایط هوازدگی پیچیده به صورت دلخواه (بعضی شامل دوره های تر و خشک) فراهم گردید. این روش بسیار نوید بخش و دارای قابلیت می باشد.
پربازدیدترین مطالب ما را از دست ندهید!
«صحت» مدل ها موضوع مرسومی که اغلب مورد بحث واقع می شود. در واقع، مناسب تر آن است که بهترین مدل برای یک نوع FRC مشخص، مورد بحث قرار گیرد. در صورتی که Vfcrit Vf ≈ باشد، یعنی ترکیب در درجه اول برای نشان دادن طاقت ناحیه IV (شکل 9-2) طراحی شده باشد، مدل های خوردگی الیاف چندان مناسب نیستند، زیرا وابسته به زمان بودن چنین رفتاری تحت تاثیر اثرات پیوستگی قرار دارد. در صورتی که طول الیاف بسیار بیشتر از طول بحرانی باشد، مدل های پیوستگی یا تراکم خمیر مناسب نخواهند بود، زیرا صرف نظر از سن، بیرون کشیدگی کوچک آشکار و مشخص خواهد بود (اگر چه اثرات قرارگیری الیاف در عرض ترک، باز هم تاثیرگذار خواهد بود). الیاف شکل پذیر (نرم) در معرض ضعیف شدگی ناشی از رشد درزها قرار نداشته و با قرارگیری در عرض ترک به حالت خمیده نیز مشکلی نخواهند داشت و بنابراین، هیچکدام از مدل ها ممکن است مناسب نباشند. بنابراین ملاحظات تئوری ACK می تواند کافی باشد. همچنین تقریبا مشخص شده است که ضعیف شدگی الیاف و تراکم خمیر با هم اتفاق می افتند و بنابراین هدف تحقیقات آینده مدلی است که اثرات هر دو را شامل شود.
پایداری حجمی و ترک خوردگی
بسیاری از مشکلات عملکرد بلندمدت ترکیبات سیمانی الیافی، نتیجه تغییرات خواص ااین ترکیبات نمی باشد، بلکه ناشی از تغییرات حجمی مصالح است که بر اثر تغییرات دمایی و رطوبتی به وجود می آید. احتمال جمع شدگی صفحات نازک سیمانی الیافی ممکن است به میزان قابل ملاحظه ای از جمع شدگی بتن تجاوز نماید. کرنش های معمول جمع شدگی برای بتن معمولا کمتر از 05/0% می باشد، در حالی که بای صفحات نازک FRC مقادیر تورم در محد��ده 1/0% تا 2% اندازه گیری شده است. بایستی توجه داشت که این وضعیت در صفحات نازک FRC وجود دارد، اما در بتن الیافی که جمع شدگی در آن برابر یا کوچک تر از بتن غیرمسلح است، اینگونه نمی باشد. تورم بیشتر در صفحات نازک کامپوزیت ها، نتیجه عوامل مختلفی بوده که عبارتند از مقدار سیمان بیشتر از مخلوط بتن معمولی (یعنی مصالح سنگی کمتر) و نیز وجود الیاف حساس به رطوبت مانند الیاف سلولزی یا طبیعی. به علاوه، هندسه نازک سیمانی الیافی منجر به خشک شدگی با سرعت بیشتر می گردد.
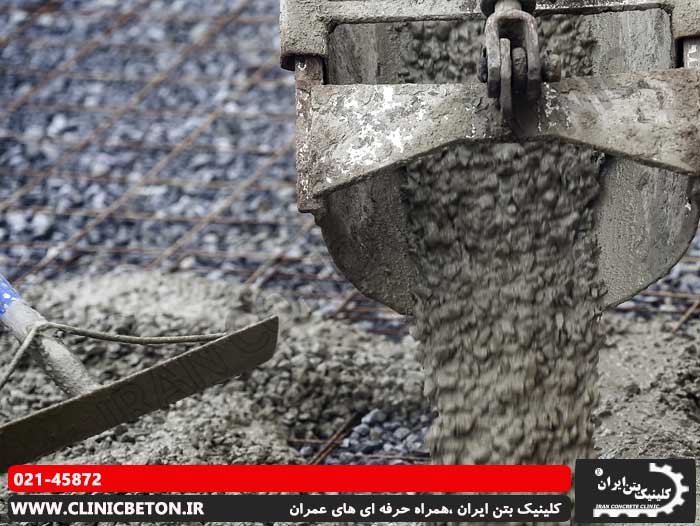
مقاومت بتن های الیافی
تغییرات حجمی به وجود آمده حین قرارگیری طبیعی در معرض تر و خشک شدن ممکن است موجب آسیب داخلی ناشی از ریزترک ها گردد. این موضوع برای سیمان مسلح به ذرات چوب به اثبات رسیده است که در آن سالخوردگی در آب منجر به افت مقاومت نگردید، درحالی که چرخه های تر و خشک شدن منجر به افت مقاومت گردید که میزان افت برای چرخه های خشک شدن شدیدتر، بیشتر بود. تخریب و آسیب به وجود آمده نتیجه آسیب داخلی ناشی از تغییرات حجمی بود. می توان انتظار داشت که این نوع آسیب برای آزمایش تحت شرایط مفید شده که در آن تنش های داخلی بزرگ تری در نتیجه تغییرات حجمی مقید شده انتظار می رود، بیشتر باشد. بنابراین، کاهش خواص و پیدایش ترک ها ممکن است حتی برای ترکیباتی که در آنها تغییرات حجمی نسبت به سیمان مسلح به ذرات چوب کوچک تر می باشند، مشاهده گردد.
تغییرات ابعادی می تواند مشکلاتی را ایجاد نماید که ارتباطی با افت خواص مصالح ندارند. در برخی کاربردهای صفحات نازک FRC مانند روکش نمودن، تغییرات ابعادی ممکن است منجر به قوس برداشتن صفحه و ایجاد ترک های ریز و درشت گردد. میزان آسیب، به تخریب مصالح و ماهیت اتصالات، قیدها و سازه زیرین بستگی دارد. این نوع مشکل عملکردی بلندمدت می تواند بحرانی تر از تغییر خواص مصالح در طول زمان باشد. متاسفانه این مشکل در مراجع علمی که معمولا مباحث دوامی مربوط به خواص خود مصالح را برجسته می نمایند، مورد توجه کافی قرار نگرفته است. راهکار موردنیاز عبارت است از مطالعه عملکرد جمع شدگی مقید شده خود مصالح و یا آزمایش صفحات با مقیاس کامل شامل اتصالات آنها به سازه، مطابق با توصیه های موجود در ISO 8336. جمع شدگی مقید شده FRC در سال های اخیر به صورت گسترده تری مورد مطلعه قرار گرفته است تا محدوده ای که وجود مقادیر کوچک الیاف می تواند جمع شدگی و ترک خوردگی مربوط به آن در بتن را کاهش دهد، مورد بررسی و ارزیابی قرار گیرد. این مطالعات اگرچه مستقیما به ارزیابی عملکرد بلندمدت صفحات نازک سیمانی الیافی نمی پزدازند، اما بستری را برای روش شناسی و زمینه علمی مورد نیاز جهت بررسی اینگونه موضوعات فراهم می نمایند. ایتاندارد نمودن چنین آزمایشاتی هم اکنون با استفاده از ساختارهایی مشابه آنچه توسط سی و همکاران گزارش نموده اند، در دست انجام می باشد.