افزودنی های متفرقه
در کنار افزودنی های شناخته شده و پر کاربرد مانند کاهنده های آب، هوازاها، کندگیر کننده ها، شتاب دهنده ها، حجم زاها، و پایاگرها که در بخش های پیشین به آنها پرداخته شد گستره دیگری از افزودنی های شیمیایی با عملکرد ویزه یا دامنه کاربرد محدود نیز وجود دارند که در دسته بندی افزودنی های بتن که کاربرد زیادی دارند، جای نمی گیرند.
از سوی دیگر، گسترش روزافزون دانش شیمی ساختمان و نوآوری های فنی و صنعتی در تولید افزودنی های شیمیایی در کنار رویکرد به مسایل زیست محیطی و توسعه پایدار سبب پیدایش و عرضه افزودنی های جدید با ویژگی ها و کارکردهای نوین شده است.
در این بخش کوشش شده است تا با شناساندن افزودنی های متفرقه که گاهی افزودنی های (با کارکرد) ویژه نیز نامیده می وشند، زمینه آشنایی دست اندر کاران صنعت بتن با این افزودنی ها و کاربرد آنها فراهم آید.
کاهنده های انبساط واکنش قلیایی – سیلیسی
متداول ترین واکنش بین قلیایی های سیمان و سنگدانه ها، واکنش بین اجزای واکنش زای سیلیسی سنگدانه ها و قلیایی های موجود در سیمان است که به نام واکنش قلیایی – سیلیسی شناخته می شود. این واکنش با حمله هیدروکسیدهای قلیایی، که از قلیایی های موجود در سیمان (K2O , Na2O) یا هر منبع دیگری مشتق می شوند، به کانی های سیلیسی واکنش زای موجود در سنگدانه ها شروع می شود. در نتیجه یک ژل قلیایی سیلیکاتی در صفحات ضعیف یا در منافذ سنگدانه ها (جایی که سیلیس فعال وجود دارد) یا بر سطح ذرات سنگدانه ها ایجاد می شود. در مورد اخیر، هاله ای از ژل در پیرامون دانه سنگی پدید می آید که در اثر مرطوب شدن می تواند پیوستگی بین سنگدانه و خمیر در برگیرنده آن را از بین ببرد.
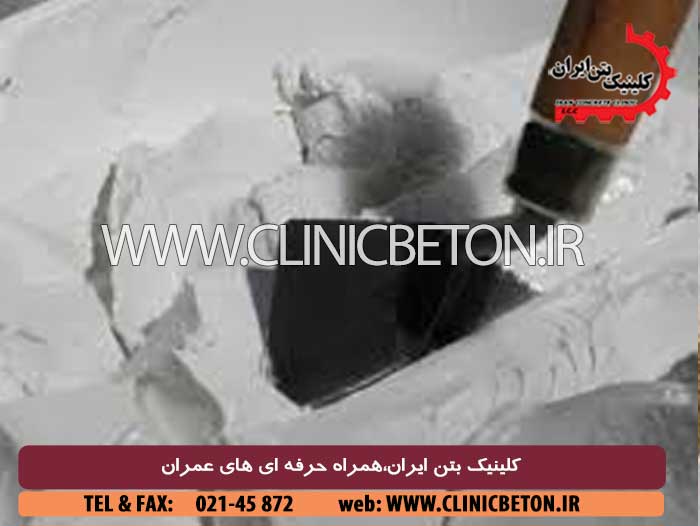
ژل حاصل از نوع "ورم کننده نامحدود" است که آب را به خود راه و در نتیجه افزایش حجم می دهد. از آنجا که این ژل به وسیله خمیر سیمان هیدراته اطراف خود احاطه شده است، انبساط ژل سبب ایجاد فشارهای داخلی در خمیر سیمان پیرامونی سنگدانه می شود که در نهایت به ترک خوردن و از هم پاشیدن خمیر سیمان منتهی می شود خلاصه این واکنش به شرح زیر است. واکنش قلیایی – سیلیسی بسیار کند است و روند انجام آن به مقدار کل قلیای موجود در بتن، میزان واکنش پذیری سنگدانه ها، و در دسترس بودن رطوبت بستگی دارد.
به دلیل اینکه واکنش قلیایی – سیلیسی درمان قطعی ندارد بهترین شیوه برای پرهیز از آن پیشگیری است. پرهیز از به کار بردن سنگدانه واکنش زا، استفاده از سیمان کم قلیا، جلوگیری از نفوذ رطوبت، و به کار بردن پوزولان ها از جمله راهکارهای پیشگیرانه هستند که اگر با دقت در عملیات ساختن و اجرای بتن همراه شوند می توانند کارآمد باشند.
چنانچه استفاده از سنگدانه واکنش زا یا مشکوک به واکنش زایی ناگزیر باشد، استفاده از افزودنی های کاهنده انبساط واکنش قلیایی – سیلیسی می تواند راهکاری پیشگیرانه به شمار آید. نمک های لیتیم (مانند نیترات لیتیم، کربنات لیتیم، هیدروکسید لیتیم) و نمک های باریم از جمله افزودنی های شیمیایی هستند که برای کنترل واکنش قلیایی – سیلیسی به کار برده شده اند. بررسی های آزمایشگاهی نشان داده است که با افزودن 1% نمک لیتیم و 2 تا 7 درصد از برخی نمک های باریم (نسبت به وزن سیمان) به مخلوط دارای سنگدانه واکنش زا، مقدار انبساط واکنش قلیایی – سیلیسی به نحوه چشم گیری کاهش یافت و وقتی که نسبت مولی لیتیم به سدیم به 67/0 افزایش یافت، انبساط واکنش قلیایی – سیلیسی مهار شد.
به نظر می رسد که با استفاده از نمک های لیتیک، در مایع منفذی بتن علاوه بر یون های سدیم، پتاسیم، و هیدروکسیل مقداری نیز یون لیتیم پدید می آید که در واکنش شیمیایی با یون های پتاسیم و سدیم رقابت می کند. چنانچه یون های لیتیم به مقدار کافی (نسبت به یون های سدیم و پتاسیم) در محیط واکنش وجود داشته باشند، با سیلیس واکنش می دهند و لیتیم سیلیکات پدید می آورند که در مقایسه با ژل قلیایی سیلیکاتی تمایل کمتری به جذب آب دارد و کمتر متورم می شود. افزودنی های پایه لیتیمی ممکن است زمان گیرش بتن را کاهش دهند و بنا به نیاز همراه با یک کندگیر کننده به کار روند.
اصلاح کننده های گرانروی (ویسکوزیته)
افزودنی های اصلاح کننده گرانروی (ویسکوزیته) افزودنی هایی هستند که برای اصلاح خواص رئولوژیک خمیر سیمان و بتن به کار می روند. گرانروی مقاومت یک سیال در برابر تغییر شکل و بیانگر اصطکاک درونی بین ذرات سیال است. رئولوزی، دانش و علم بررسی تغییر شکل و جریان یافتن مواد است و بیانگر رابطه بین تنش، کرنش، و آهنگ تغییرات کرنش نسبت به زمان است. رابطه بین تنش برشی (T) و آهنگ کرنش برشی (Y) به نام "منحنی جریان" شناخته می شود.
منحنی جریان خطی بینگهام برای توصیف رفتار رئولوژیک بتن تازه
تنش یا نقطه جاری شدن متناظر با حداقل تنش برشی مورد نیاز برای شروع جریان یا جاری شدن بتن است. در مقادیر تنش برشی کمتر از تنش جاری شدن، مخلوط تغییر شکل نمی دهد و جریان نمی یابد. تنش یا نقطه جاری شدن به کارآیی (کارپذیری) بتن بستگی دارد. ثابت تناسب (ضریب زاویه) بین تنش برشی و آهنگ کرنش برشی که به نام گرانروی خمیری شناخته می شود بیانگر مقاومت جریانی و حرکتی بتن در یک سرعت مشخص و در اثر اعمال تنش بیرونی است. سرعت جاری شدن بتن به گرانروی خمیری آن بستگی دارد.
تاثیر گرانروی خمیری بر چگونگی جریان یافتن بتن
نکته کلیدی برای دستیابی به بتنی با رئولوژی مناسب، ایجاد توازن بین تنش (نقطه) جاری شدن و گرانروی خمیری است. افزودنی های اصلاح کننده گرانروی با افزایش گرانروی خمیری، خواص رئولوژیک بتن تازه را تغییر می دهند. این افزودنی ها تنش جاری شدن را اندکی افزایش م یدهند. برای کاهش تنش جاری شدن بتن تازه از افزودنی های کاهنده آب استفاده می شود. افزودنی های اصلاح کننده گرانروی از دیدگاه سازوکار و چگونگی کارکرد به دو نوع 1) غلظت دهنده ها و 2) چسباننده ها تقسیم می شوند.
نوع غلظت دهنده با مهار مولکولی سبب افزایش گرانروی خمیر سیمان و بتن تازه می شود. غلظت دهنده ها از پلیمرهای با وزن مولکولی زیاد که میل ترکیبی شدیدی با آب دارند تشکیل می شوند. غلظت دهنده ها شبکه ای پلیمری با شاخه های آزاد در آب پدید می آورند که سر آزاد این شاخه های پلیمری با ربایش مولکولی به مولکول های آب، سیمان و ریزدانه ها می چسبد و ذرات را به یکدیگر می دوزد. به بیان دیگر، افزودنی اصلاح کننده گرانروی با اندرکنش گروه های عاملی مولکول ها غلظت دهنده با آب و با سطح ریزدانه ها در خمیر ساختاری سه بعدی در فاز مایع مخلوط پدید می آورد که مولکول های آب و ریزدانه ها را به یکدیگر پیوند می دهد و سبب افزایش گرانروی و تا حدودی افزایش تنش جاری شدن خمیر و بتن تازه می شود. افزایش گرانروی خمیر به افزایش چسبندگی درونی (قوام) ملات و بتن تازه می انجامد. غلظت دهنده ها شامل سلولز اِترهای محلول در آب، پلیمرهای آکریلیک، نشاسته های پیش ژلاتینه، پلیمرهای کربوکسی وینیل، و پلی وینیل الکل می شوند.
نوع چسباننده افزودنی های اصلاح کننده گرانروی با ترکیبات آهکی محلول موجود در بتن یا با مولکئل های آب اندرکنش شیمیایی نشان می دهند و ژلی سه بعدی پدید می آورند که رفتار تیکسوتروپی خمیر را بهبود می بخشد و گرانروی خمیر سیمان و بتن را افزایش می دهد. تیکسوتروپی کاهش گرانروی یک خمیر تحت اثر تنش برشی ثابت است که با حذف تنش برشی به تدریج ساختار اولیه خود را باز می یابد. افزودنی های اصلاح کننده گرانروی نوع چسباننده از مواد معدنی ژل ساز تشکیل می شوند. از جمله این مواد معدنی می توان به سیلیس کلوییدی، ریزدانه های معدنی با سطح ویژه بسیار زیاد مانند بنتونیت و پنبه کوهی آسیاب شده، و به پرکننده های معدنی مانند آهک هیدراته، خاک دیاتومه، کائولین، و خاکستر بادی اشاره کرد.
ساختار سه بعدی یا ساختار ژلی که افزودنی های اصلاح کننده گرانروی پدید می آورند علاوه بر کنترل خواص رئولوژیک و بهبود چسبندگی درونی (قوام) مخلوط، به معلق ماندن دانه های سنگی کمک می کند و پراکندگی سنگدانه ها را در بتن یکنواخت می کند. پراکندگی یکنواخت و همگن سنگدانه ها در مخلوط بتن به کاهش جداشدگی وآب انداختن و به کاهش ته نشینی در بتن تازه می انجامد.
افزودنی های اصلاح کننده گرانروی گروهی از افزودنی ها هستند که برای کاربردهای ویژه طراحی شده اند. سه کاربرد اصلی این افزودنی ها عبارتند از:
- قوام بخشی و تنظیم ویژگی های رئولوژیک و حفظ همگنی و پایداری بتن خودتراکم
- کاهش آب شستگی بتن
- آسان سازی پمپ کردن بتن
- از این افزودنی ها در بتن پاشی، ملات تعمیری، بتن سبکدانه، قطعات پیش ساخته با بتن نیمه خشک، و اندودهای کف و پلاسترها نیز استفاده می شود.
1- قوام بخشی بتن خودتراکم
بتن خودتراکم (SCC) بتنی همگن و دارای قوام با روانی زیاد است که به آسانی جریان می یابد و بدون نیاز به هیچ عامل یا روش متراکم کننده اضافی تنها در اثر وزن خود متراکم می شود. این بتن به آسانی می تواند گوشه و کنار قالب را (حتی در آرماتوربندی های فشرده) پر کند و به دلیل درون چسبی و قوام مناسبی که دارد هیچگونه جداشدگی در آن رخ نمی دهد.
بتن خودتراکم دارای دو ویژگی اصلی 1) روانی زیاد و 2) درون چسبی (قوام) مناسب است. روانی زیاد و قابلیت جریان یافتن با کاهش تنش (نقطه) جاری شدن بیان می شود که با استفاده از فراروان کننده ها
(به بند 2-6-7 بخش دوم مراجعه شود) به دست می آید. افزایش روانی بتن به خودی خود می تواند تمایل به جدشدگی را (به ویژه در مخلوط های با دانه بندی نامناسب و با ریزدانه کم) افزایش دهد. بنابراین برای همگن ماندن مخلوط لازم است که بتن با اینکه بسیار روان است از درون چسبی و قوام مناسب و کافی برخوردار باشد. بهبود درون چسبی و قوام بتن با افزایش گرانروی خمیری آن و با استفاده از افزودنی های اصلاح کننده گرانروی یا قوام بخش ها به دست می آید.
بیشترین نوسانی که یک بتن خودتراکم با طرح اختلاط مناسب ممکن است با آن مواجه شود نوسان هنجار (معمول) مقدار رطوبت سنگدانه ها در زمان ساخت بتن است. برای نمونه، تغییر 5/1 درصدی در رطوبت سنگدانه ها می تواند به تغییری 10 تا 15 لیتری در آب آزاد هر مترمکعب بتن بیانجامد. این مقدار نوسان در آب آزاد م یتواند تغییرات چشم گیری در روانی و قوام بتن تولید شده به دنبال داشته باشد. افزودنی های اصلاح کننده گرانروی یا قوام بخش ها تاثیر پذیری بتن را در برابر نوسان و تغییرات مقدار آب مخلوط کاهش می دهند واز حساس بودن بتن خودتراکم به تغییرات رطوبتی سنگدانه ها می کاهند.
مزایایی که افزودنی اصلاح کننده گرانروی برای بتن خودتراکم دارند در زیر آورده شده است:
- بهبود قوام بتن و کاهش خطر جداشدگی
- بهبود پایداری مخلوط و کاهش ته نشینی سنگدانه های درشت
- کاهش آب انداختن
- نیاز کمتر به پرکننده
- حساسیت کمتر مخلوط به نوسان های رطوبتی سنگدانه ها در زمان ساخت بتن
- بهبود سرعت و آهنگ بتن ریزی
- امکان استفاده از مخلوط های پایدار با روانی بیشتر
- بهبود سطح نمای بتن
نکته- نبیاید انتظار داشت که افزودنی های اصلاح کننده گرانروی جانشین و جبران کننده کاستی هایی مانند طرح اختلاط نامناسب و ضعف عملیات اجرایی در بتن خودتراکم به شمار آید. استفاده بیش از اندازه افزودنی اصلاح کننده گرانروی می تواند به چسبناک شدن بتن و کاهش سرعت بتن ریزی بیانجامد. در چنین مواردی می توان با افزایش مقدار فوق روان کننده بتن مصرفی بر این مشکل چیره شد. بیشتر این افزودنی ها در مقادیر مصرف متعارف تاثیر اندکی بر ویژگی های بتن سخت شده دارند ولی در مقادیر مصرف زیاد ممکن است گیرش را به تاخیر اندازند یا در بتن هوازایی شده برمقدار و پایداری حباب های هوا تاثیر بگذارند. مناسب ترین روش برای تعیین مقدار مصرف افزودنی اصلاح کننده گرانروی، بهره گیری از مخلوط های آزمایشی است.
2- کاهش آب شستگی
برای بتن ریزی در زیر آب یا بتن ریزی و تزریق دوغاب سیمان در جاهایی که آب جاری وجود دارد (مانند پشت قالب برخی از تونل ها) همیشه خطر شسته شدن سیمان و ریزدانه بتن تازه ریخته شده وجود دارد. وجود آب در تماس با بتن تازه خطر افزایش نسبت آب به سیمان و افت ویزگی های بتن سخت شده را نیز در پی دارد.
برای جلوگیری از آب شستگی بتن یا دوغاب تازه در حین و پس از بتن ریزی لازم است که مخلوط بتن از درون چسبی و قوام بسیار خوبی برخوردار باشد. چنانکه گفته شد کارکرد اصلی افزودنی های اصلاح کننده گرانروی یا قوام بخش ها افزایش قوام بتن تازه و کمک به پایداری مخلوط است و از این رو برای بتن ریزی در زیر آب یا بتن ریزی در جاهایی که جریان آب وجود دارد بسیار مناسب هستند. به همین دلیل گاهی این افزودنی ها به نام افزودنی ضد آب شستگی یا افزودنی برای بتن ریزی زیر آّ نیز شناخته می شوند.
در مواردی که جریان آب شدید و احتمال شسته شدن بتن تازه زیاد باشد از نوعی افزودنی ضد آب شستگی استفاده می شود که از لخته کننده های الی تشکیل شده اند. این لخته کننده ها به سطح دانه های سیمان می چسبند و با تشدید نیروی ربایش بین ذرات سبب افزایش گرانروی مخلوط می شوند. لخته کننده ها از کوپلیمرهای استایرن دارای گروه های کربوکسیل یا از پلی الکترولیت های مصنوعی یا از صمغ های طبیعی تشکیل می شوند. چون ریختن بتن و متراکم کردن آن در زیر آب کاری دشوار است باید بتن علاوه بر دارا بودن قوام و پایداری مناسب از کارآیی بسیار بالایی نیز برخوردار باشد. بنابراین برای بتن ریزی در زیر آب به همراه افزودنی های ضد آب شستگی از یک کاهنده آب نیز استفاده می شود. استفاده از افزودنی های اصلاح کننده گرانروی یا قوام بخش ها برای بتن ریزی در زیر آب علاوه بر اینکه خطر آب شستگی سیمان و ریزدانه های بتن را کاهش می دهد، به کاهش آلودگی آب و حفظ محیط زیست کمک می کند و دید بهتری نیز برای غواصان و افزاد بتن ریز در زیر آب فراهم می کند.
3- آسان سازی پمپ کردن بتن
بتن با قابلیت پمپ شدن باید دارای دو ویزگی اساسی باشد. اول آنکه به اندازه کافی خمیر داشته باشد که پیرامون سنگدانه ها را بپوشاند و لایه ای لغزنده بین بتن و جداره لوله پمپ پدید آورد تا اصطکاک بین بتن و لوله به حداقل برسد، راهکار شناخته شده ای که برای تامین خمیر کافی به کار گرفته می شود افزایش زیردانه ها در بتن است. دوم آنکه این خمیر از غلظت مناسب برخوردار باشد تا از یک سو عملکرد لایه لغزنده درست باشد و از سوی دیگر چسبندگی درونی و قوام بتن به اندازه کافی باشد تا خمیر و دوغاب در اثر فشار پمپ از بتن جدا نشود و پدیده فرار دوغاب رخ ندهد. در صورت جدا شدن و فرار دوغاب از بتن، دانه های درشت در یکدیگر چفت می شوند و بتن در لوله گیر خواهد کرد. هر قدر که مخلوط مستعد آب انداختن باشد، احتمال فرار دوغاب آن در اثر فشار پمپ نیز بیشتر می شود. این جداشدگی و فرار دوغاب بیشتر در زانویی ها و محل های تغییر مقطع لوله رخ می دهد. کم بودن قوام بتن به ویژه در زمانی که پمپ به طور موقت کار نمی کند (مانند توقف تخلیه بتن در فاصله زمانی بین دو تراک میکسر) و بتن در مسیر لوله بی حرکت مانده است احتمال ته نشینی دانه های درشت را در مسیر لوله افزایش می دهد و این جداشدگی برای ادامه و شروع دوباره عملیات پمپ کردن مشکل آفرین است. از سوی دیگر، قوام بیش از اندازه مخلوط بتن نیز می تواند به غلظت بیش از اندازه خمیر بیانجامد و چسبناکی بتن را افزایش دهد و منجر به افزایش اصطکاک بتن چسبناک و جداره لوله پمپ شود. افزودنی های اصلاح کننده گرانروی با افزایش غلظت و چسبندگی درونی خمیر از یک سو به بهبود یکپارچه و همگنی مخلوط کمک می کنند و قوام آن را افزایش می دهند و از سوی دیگر با کاهش ظرفیت آب انداختن مخلوط به کاهش احتمال فرار دوغاب در اثر فشار پمپ کمک می کنند. این افزودنی ها همچنین با بهبود یکنواختی و همگنی بتن تازه احتمال ته نشینی دانه های درشت را در مسیر لوله و در زمان توقف عملیات پمپ کاهش می دهند. این افزودنی ها در مقادیر مصرف مناسب می توانند به کاهش اصطکاک بین لئله و بتن نیز کمک کنند. افزودنی های اصلاح کننده گرانروی که برای بهبود ویزگی های بتن پمپ شونده به کار می روند به نام افزودنی های کمک کننده پمپ کردن نیز شناخته می شوند.
لاتک�� ها
لاتکس یا شیرآبه، ذرات معلق پلیمر در آب است. پس از آنکه لاتکس به اندازه کافی آب خود را از دست بدهد ذرات پلیمر به یکدیگر نزدیک و در اثر ربایش مولکولی به یکدیگر می چسبند و لایه ای پیوسته و کشسان پدید می آورند. ذرات پلیمر که در اثر از دست دادن آب سیستم به یکدیگر نزدیک شده اند علاوه بر یکدیگر به مولکول سایر ذرات و سطوح نیز می چسبند و چسبندگی خوبی به سطوح و دیگر مواد دارند.
در صورت مصرف لاتکس در بتن ویزگی های بتن به شرح زیر بهبود می یابد:
- تراوایی (گذرپذیری) بتن را کاهش و پایایی آن را بهبود می دهند
- پیوند و چسبندگی به بتن پایه و به میلگرد ها را بهبود می بخشند
- مقاومت خمشی بتن را افزایش می دهند
انعطاف پذیری و طاقت (چقرمگی) بتن وایستادگی سایشی (در برابر سایش) آن را افزایش می دهند مقدار مصرف لاتکس ها در بتن بین 5 تا 20 درصد وزن مواد سیمانی است و لازم است که آب مخلوط در زمان ساخت بتن اصلاح شود. ماده امولسیون کننده ای که در زمان تولید لاتکس استفاده می شود می تواند سبب هوازایی در بتن شود. برخی از لاتکس ها مانند استایرن بوتادین رابر کارآیی (کارپذیری) و روانی مخلوط بتن را بهبود می بخشند در حالیکه برخی دیگر مانند بعضی از آکریلیک ها ممکن است سبب کاهش روانی مخلوط شوند. لاتکس ها در بتن و ملات دارای سه کاربرد اصلی 1) پیوندزایی بین بتن تازه و سخت شده در کارهای تعمیر و مقاوم سازی، 2) کفسازی، و 3) پوشش های سیمانی لاتکس دار تقسیم می شود.
1- پیوندزایی
لاتکس ها امولسیون پلیمرهای آلی در آب هستند و برای افزایش چسبندگی و مقاومت پیوستگی بین بتن جدید و موجود در مخلوط های سیمانی به کار می روند به همین دلیل گاهی به نام افزودنی های پیوندزا نیز شناخته می شوند. لاتکس ها برپایه نوع پلیمر امولسیون شده به انواع لاتکس پلی وینیل کلراید (PVC)، پلی وینیل استات (PVA)، آکریلیک ها، کوپلیمرهای استایرن بوتادین، و لاتکس لاستیک طبیعی تقسیم می شوند. یکی از کاربردهای اصلی لاتکس، پیوندزایی و ایجاد لایه پیوندزا بین بتن موجود و بتن جدید در کارهای تعمیری و مقاوم سازی است. لاتکس ها به دو نوع بازپخش شونده و بازپخش ناشونده تقسیم می شوند. لاتکس های بازپخش شونده پیش از اعمال بتن یا ملات جدید به طور مستقیم بر روی سطح زیرین اعمال می شوند. لاتکس های بازپخش شونده در تماس با آب و رطوبت به تدریج با جذب کردن آب چسبندگی اولیه خود را به دست می آورند و برای کارهای داخل ساختمان که در تماس همیشگی با آب یا رطوبت زیاد نباشند مناسب هستند.
نکته- یادآوری می شود که از لاتکس های بازپخش شونده می توان به عنوان ماده پیوندزا یا چسب بتن استفاده کرد ولی این لاتکس ها جزو افزودنی های پیوندزا به شمار نمی آیند. لاتکس های بازپخش ناشونده پس از آنکه در اثر از دست دادن آب خود تشکیل لایه (فیلم) دهند در برابر آب و رطوبت مقاومت خوبی دارند و برای کاربردهای بیرون ساختمان و جاهایی که در تماس با آب و رطوبت باشند مناسب هستند. این نوع لاتکس ها جزو افزودنی های پیوندزا به شمار می روند و همراه و در ترکیب با سیمان یا مواد سیمانی به کار می روند. به کاربردن این نوع لاتکس ها به تنهایی به عنوان ماده پیوندزا (چسب بتن) برای چسباندن بتن جدید به بتن موجود توصیه نمی شود و بهتر است آنها را به صورت دوغاب سیمانی لاتکس دار برای لایه پیوندزا به کار برد.
2- کفسازی
افزودنی های پیوندزا که لاتکس های بازپخش ناشونده هستند به تدریج آب خود را در بتن یا ملات (در اثر مصرف آب درونی برای واکنش های آبگیری سیمان یا مواد سیمانی) از دست می دهند. با از دست رفتن آب لاتکس به تدریج ذرات پلیمر به یکدیگر نزدیک می شوند و در اثر نیروهای بین مولکولی به یکدیگر و به سایر ذرات می چسبند و ساختاری سه بعدی از زنجیره های پلیمری در بتن یا ملات پدید می آورند. با پیشرفت واکنش آبگیری سیمان و با گذشت زمان به تدریج محصولات آبگیری سیمان زنجیره های پلیمری را در بر می گیرند. بنابراین می توان اینگونه انگاشت کهاین ساختار سه بعدی از زنجیره های پلیمری همانند ریزالیاف عمل می کند و خواص مکانیکی به ویژه مقاومت کششی و خمشی بتن را بهبود می بخشد. از سوی دیگر، زنجیره های پلیمری که با محصولات آبگیری سیمان در بر گرفته شده اند دارای ویژگی ترک دوزی هستند و از گسترش ریزترک ها وتبدیل شدن آنها به ترک در بتن و ترک های نمایان در سطح بتن جلوگیری می کنند. بنابراین استفاده از لاتکس ها می تواند به کنترل ترک های تکیدگی و جلوگیری از گسترش آنها کمک کند. به بیان دیگر، لاتکس ها نقشی در کاهش تکیدگی (جمع شدگی ناشی از خشک شدن) بتن ندارند و فقط پیامد آن یعنی ترک های تکیدگی را کنترل می کنند.
این دو کارکرد لاتکس ها در بتن یعنی افزایش مقاومت کششی و خمشی و نیز کنترل ترک های تکیدگی به همراه بهبود چسبندگی که لاتکس ها به بتن زیر فراهم می آورند، کاربرد لاتکس ها را در روکش های بتنی برای کفسازی بسیار سودمند و کارآمد کرده است.
3- پوشش ها
لاتکس ها در کنار کارکردهایی که به آنها اشاره شد یعین بهبود مقاومت کششی و خمشی، کنترل ترک های تکیدگی، و بهبود چسبندگی بتن و ملات سبب بهبود انعطاف پذیری ملات و بتن نیز می شوند. این کارکردها امکان استفاده از اندودهای رنگی سیمانی دارای لاتکس را برای پوشش های محافظ و پوشش های نماسازی فراهم می کنند.
ضدیخ
یخ زدن در بتن سخت شده، بتن جوام (نارس، نوگرفته)، و بتن تازه از سه دیدگاه گوناگون بررسی می شود. یخ زدن بتن سخت شده در مبحث پایایی بتن در برابر چرخه های یخ زدن و آب شدن مورد ارزیابی قرار می گیرد و همچنان که در فصل سوم (افزودنی های هوازا) اشاره شد، راه کار بهبود و افزایش پایایی بتن سخت شده در برابر چرخه های یخ زدن و آب شدن به کاربردن افزودنی های هوازا است. بتن جوان (نارس، نوگرفته) به بتنی گفته می شود که گیرش آن انجام شده باشد ولی هنوز سخت نشده است. به بیان دیگر، بتن از یک سیال خمیری به یک جسم جامد تغییر حالت داده است ولی هنوز نمی تواند بارها و تنش های وارده را به خوبی تحمل کند. بتن جوان (نارس، نوگرفته) در برابر یخ زدن بسیار آسیب پذیر است زیرا به آسانی ترک می خورد. راه کار بهبود توانایی بتن جوان (نارس، نوگرفته) در برابر یخ زدن همچنان که در بخش پنجم به آن اشاره شد، شتاب دادن به روند کسب مقاومت آن به کمک افزودنی های زودسخت کننده است تا بتواند تنش های درونی ناشی از افزایش حجم یخ را تحمل کند. یخ زدن بتن تازه اندکی پیچیده تر است و نیاز به بررسی بیشتری دارد.
آب در بتن تازه به دلیل وجود یون ها و املاح به صورت خالص نیست بنابراین بتن تازه در صفر درجه سانتی گراد یخ نمی زند. از سوی دیگر بخشی از آب بتن تازه که امکان یخ زدن دارد آب آزاد است و آب جذب شده به سطح دانه های ذرات و آب بین ژل ها به سادگی یخ نمی زند. پس انتظار این است که نقطه یخبندان بتن تازه حدود 2 تا 4 درجه سانتی گراد زیر صفر باشد. در حالت کلی با کاهش دمای بتن تازه و دمای عمل آوری بتن، واکنش شیمیایی آبگیری سیمان و روند کسب مقاومت بتن کند می شود. با افزایش دمای نگه داری بتن، واکنش آبگیری شتاب می گیرد و مقاومت بتن هایی که در ابتدا در دمای پایین ساخته و نگه داری شده اند رشد می کند و در درازمدت از مقاومت بتن هایی که در دمای متعارف (حدود 23 درجه سانتی گراد) ساخته و نگه داری شده اند فراتر می رود.
با کاهش دمای بتن تازه به حدود 9 درجه زیر صفر نیز به شرط آنکه آب بتن تازه یخ نزند، واکنش آبگیری متوقف نشده هر چند که بسیار کند می شود. حتی در دمای نگه داری نزدیک به یخبندان نیز مقاومت 28 روزه حدود نصف مقاومت فشاری نمونه نگه داری شده در دمای متعارف است.
بنابراین اگر بتن تازه یخ نزند با آنکه واکنش های آبگیری سیمان بسیار کند می شوند ولی متوقف نمی شوند و با افزایش دما در سنین بالاتر روند کسب مقاومت بتن شتاب می گیرد (شکل 8-6) و در درازمدت به مقاومت مورد نظر دست خواهد یافت. از آنجا که واکنش های شیمیایی آبگیری سیمان در ابتدا نیازمند انحلال و تجزیه ترکیبات و جابجا شدن یون ها در آب است، چنانچه بتن تازه یخ بزند می توان اینگونه انگاشت که هم واکنش آبگیری سیمان تقریباً متوقف می شود و هم به دلیل آنکه یون ها نمی توانند در یخ جابجا شوند آن بخشی از واکنش که پیش از یخ زدن آغاز شده است نیز ناقص خواهد ماند. ناقص ماندن فرآیند و روند واکنش های شیمیایی آبگیری سیمان به از هم پاشیدن ریزساختار بتن و به افت شدید ویژگی های بتن سخت شده خواهد انجامید.
افزودنی های ضدیخ که برای اولین بار در دهه 1950 میلادی در شوروی سابق به کار برده شده اند، به گونه ای طراحی شده اند که هم نقطه یخبندان بتن تازه را پایین بیاورند و هم امکان بتن ریزی و عمل آمدن بتن را در دماهای زیر صفر (یخبندان آّب) فراهم آورند. این افزودنی ها به نام افزودنی برای هوای سرد نیز شناخته می شوند. نمک های (املاح) نیتریت مانند نیتریت سدیم و کلسیم، محلول آمونیاک و برخی الکل ها با وزن مولکولی زیاد از شناخته شده ترین افزودنی های ضدیخ هستند که هم به تنهایی و هم همراه با افزودنی های دیگر به کار می روند. مشخضات فنی افزودنی های ضدیخ بتن باید با استاندارد ASTM C1622 (مشخصات فنی استاندارد برای افزودنی های هوای سرد) سازگاری و همخوانی داشته باشند.
رنگ بخش ها
افزودنی های رنگ بخش که برای رنگی کردن بتن و ملات به کار می روند از رنگدانه های طبیعی یا مصنوعی ناواکنشگر و خنثی تشکیل می شوند. افزودنی های رنگ بخش یا به تنهایی به مخلوط افزوده می شوند یا همراه و در ترکیب با افزودنی های دیگر مانند هوازداها، پخش کننده ها (به ویژه کاهنده های آب) و پایدار کننده ها به کار می روند. رنگدانه های طبیعی و معدنی به ریزدانگی و خلوص رنگدانه های مصنوعی نیستند و مقدار مصرف آنها چندین برابر رنگدانه های مصنوعی و آلی است. رنگدانه های طبیعی و معدنی در مقایسه با رنگدانه های مصنوعی و آلی در زمان بهره برداری و در درازمدت از پایداری و ثبات رنگی بهتری، به ویژه در برابر پرتوهای فرابنفش (UV)، برخوردارند. افزودنی های رنگ بخش از نوع افزودنی های با عملکرد فیزیکی هستند و در روند و واکنش آبگیری سیمان دخالتی ندارند. این افزودنی ها باید با ضوابط استاندارد ASTM C979 همخوان باشند و بر ویژگی های فیزیکی و مکانیکی بتن تاثیری نداشته باشند. از رنگدانه هایی که برای بتن رنگی به کار می روند می توان به دوده اصلاح شده، اکسید آهن، فتالوسیانین، گِل اُخرا، اکسید کُرم، اکسید تیتانیم، و پودر لاجورد اشاره کرد. رنگ بخش ها برای تولید بتن رنگی و اندود سیمانی رنگدار به کار می روند. از بتن رنگی برای تولید قطعات پیش ساخته رنگی و اجرای کفسازی رنگی (موزاییک درجا) استفاده می شود. روش دیگر اجرای کفسازی رنگی استفاده از خشکه پاشی است که در آن پس از ریختن و شمشه کشی بتن کف، مخلوطی از رنگدانه و ریزدانه خشک (با یا بدون سیمان خشک) بر روی سطح بتن تازه پاشیده و همراه با بتن ماله کشی و پرداخت می شود. اندودهای رنگی به دو روش پاشش یا اجرای دستی به سطح اعمال می شوند. در روش پاششی، سطح اندود بافت دار و نامنظم می شود. در روش دستی، سطح تمام شده ی اندود می تواند صاف یا بافت دار باشد. از آنجا که پرداخت بیش از اندازه سطح اندود ممکن است به چندرنگی (پررنگی و کم رنگی) سطح بیانجامد بهتر است از پرداخت و ماله کاری بیش از اندازه سطح اندود پرهیز شود. رنگ بخش های آلی بیشتر از رنگ بخش های معدنی مستعد چندرنگی در اثر پرداخت سطح هستند. برای بتن و اندود رنگی بهتر است از سیمان سفید استفاده شود.
اگر مقدار مصرف رنگدانه ها (به جز دوده) کمتر از 6% وزن سیمان باشد معمولاً اثری بر ویژگی های بتن تازه و سخت شده ندارند. در هر حالتی مقدار مصرف رنگدانه نباید از 10% وزن سیمان بیشتر باشد. دوده مقدار هوای بتن را در بتن هوازایی شده به شدت کاهش می دهد و بنا به نیاز باید مقدار مصرف افزودنی هوازا را در بتن رنگی هوازایی شده افزایش داد. استفاده از کلسیم کلراید (نوعی شتاب دهنده برای بتن غیر مسلح) همراه با رنگدانه ها سبب چندرنگی و بدرنگی بتن می شود.
هوازداها
افزودنی های هوازدا مقدار هوا را در بتن کاهش می دهند. این مواد زمانی مورد استفاده قرار می گیرند که مقدار هوا را نمی توان با تنظیم نسبت های اختلاط یا با تغییر مقدار مصرف مواد هوازا ودیگر افزودنی ها کاهش داد. هوازداها به ندرت به تنهایی استفاده می شوند و معمولاً به عنوان جزء تنظیم کننده مقدار هوا در دیگر افزودنی ها (به ویژه کاهنده های آّب) به کار می روند. کارآمد بودن ]اثرگذاری[ و محدوده مصرف آنها پیش از مصرف در ساخت بتن در کارگاه، باید براساس مخلوط های آزمایشی تعیین شود. تری بوتیل فسفات، دی بوتیل فتالات، اکتیل الکل، اسید کربنیک و اسید بوریک، استرهای انحلال ناپذیر در آب، و سیلیکون ها از جمله موادی هستند که برای هوازدایی و کاهش مقدار هوا در بتن تازه به کار می روند. این افزودنی ها گاهش به نام های کف زدا یا از بین برنده های هوا نیز شناخته می شوند.
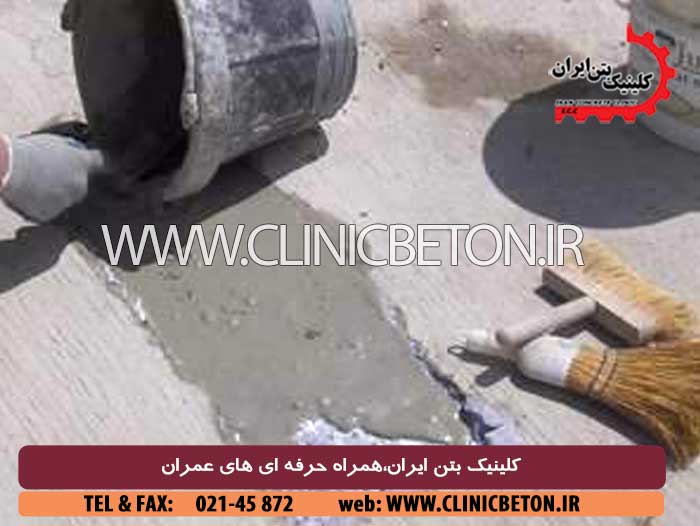
افزودنی های قارچ کش، میکروب کش و حشره کش
رشد باکتری ها و قارچ ها بر روی سطح بتن یا در درون بتن را می توان تا حدودی با بهره گیری از افزودنی های قارچ کش، میکروب کش و حشره کش کنترل کرد. کاربرد اصلی این افزودنی ها جلوگیری از رشد باکتری و قارچ روی سطح دیوار و کف های بتنی در مناطق مرطوب است. موثرترین مواد از این دسته، فنل های پلی هالوژنه، امولسیون های دی آلدرین، و ترکیبات مس (مانند کات کبود) هستند. اثرگذاری این مواد به ویژه ترکیبات مس عموماً موقتی است و به شرایط و نوع باکتری و قارچ موجود بستگی دارد و با توجه به روش های پاکسازی سطوح در زمان بهره برداری، میزان موثر بودن آنها تغییر می کند. مقادیر مصرف بیشتر از 3 درصد این افزودنی ها ممکن است مقاومت بتن را کاهش دهد.